Forestill deg at bedriften Rottefella har en banebrytende ide de vil ha testet ut før en viktig skisamling i neste uke. Hvor skal de henvende seg for å få en funksjonell prototyp raskt? Å bruke vanlige støpeformer i stål vil ta alt for lang tid.
Unge kreative gründere opplever et lignende problem: Siden støpeformer i stål er dyre, blir usikre prosjekter lagt på is. Gründere klarer rett og slett ikke å finansiere en slik produksjon.
Nå vil en rekke industri- og forskningspartnere finne en løsning på problemet. De har gått sammen i prosjektet AddForm for å utvikle best mulig 3D-printede støpeformer i plast.

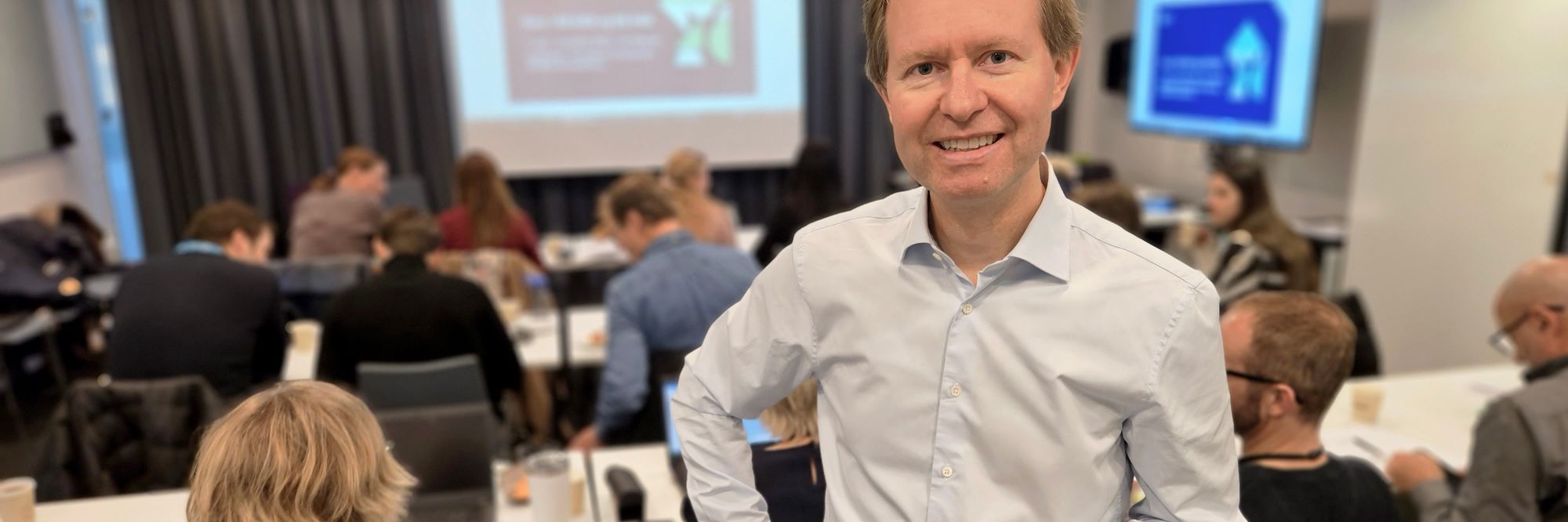
Les også: Elleve dingser som kan bli bedre med grafén
Fra stål til plast
– Ved store kvanta egner maskinert stål og også 3D-printede stålformer seg godt. Som når Lego lager klosser i millionantall, forteller Erik Andreassen på SINTEF Materialer og kjemi.
– Men skal man støpe få enheter og drive prøvestøping, kan 3D-printede støpeformer i plast, eller rettere sagt polymermaterialer fylt med keramiske partikler eller metallpartikler, være tingen. Slike former kan lages i løpet av en dag eller to, og så kan produktet sprøytestøpes i riktig plastmateriale.
Les også: Denne 3D-printeren koster bare 1450 kroner
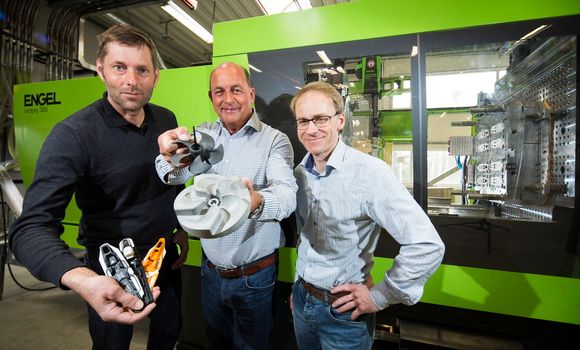
Får ut produktene i riktig materiale
3D-printing eller additiv tilvirkning startet opp kommersielt for drøyt 25 år siden, og forskere ved SINTEF har jobbet med temaet i mange ulike sammenhenger.
I AddForm-prosjektet er jobben å forstå egenskapene til formmaterialene med tanke på belastningene de utsettes for ved sprøytestøping. For at industrien skal få et raskt og godt resultat, må materialene testes opp mot hverandre for å sjekke ulikheter.
– Det finnes en rekke prosesser for 3D-printing og ulike materialtyper, og alle har sine styrker og svakheter med tanke på å lage forminnsatser, forklarer Andreassen.
Forskerne vil jobbe for å finne raskere måter å montere formene på, og effektive overflatebehandlinger for å gi overflaten i formen en ønsket finish.
Ikke bare skal industrien få sprøytestøpt prototyper raskt og billig, men de skal også få ut produktene i riktig materiale; det materialet som skal brukes i fullskalaproduksjonen og som har de spesielle egenskapene som er ønsket.
– Det er viktig å merke seg at for de fleste industrielle anvendelser kan man ennå ikke 3D-printe deler i plast med "riktige produktegenskaper", som slagstyrke eller brannhemming. Man må gå veien via sprøytestøping for å få til dette, sier Andreassen.
Les også: Volvo vil spraylakkere syklister
Forsprang internasjonalt
Prosjektet AddForm er satt i gang av OM BE Plast og SINTEF – og har bedrifter som Rottefella, Stokke, Eker Design og Lærdal Medical med på laget.
.png)
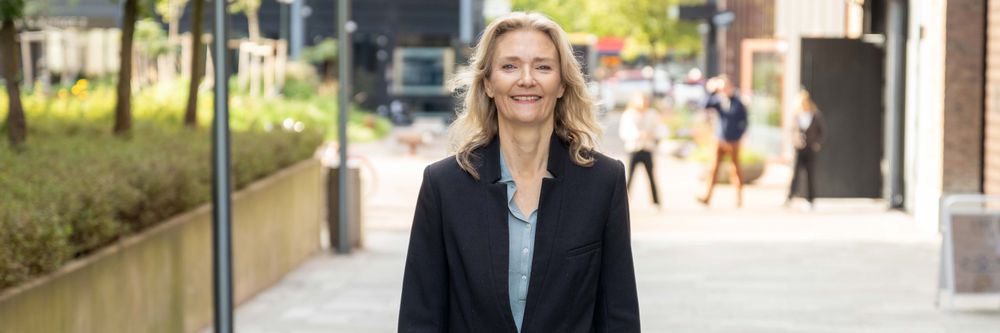
Internasjonalt er det flere FoU-miljø som arbeider med støpeformer som dette, men den norske prosjektgruppa mener de har et forsprang: De har allerede kommet fram til flere gode løsninger som ikke er kjent i markedet.
Det er også et pluss at samtlige industripartnere driver med produktutvikling på høyt nivå, og at flere jobber med krevende produkttyper. En god del av partnerne har også egne 3D-printere.
OM BE Plast har allerede fått mange henvendelser om framstilling av nye støpeformer.
– I noen tilfeller er teknologien klar, men mange henvendelser må vente til vi har fått de svarene vi venter oss fra dette FoU-prosjektet, sier Erik Andreassen.
Les også: Intels 3D-kamera kommer til mobiler