Den aktuelle modellen er den lille elbilen Strati, som er deres første beregnet på masseproduksjon. Hele karosseriet med chassis er printet i ett stykke, en prosess som tok 44 timer. De mekaniske delene er hentet fra Renault Twizy.
Pressekontakt Kate Hartley i Local Motors forteller at de regner med å ha bilen klar for markedet i løpet av neste år.
– Den vil koste mellom 18.000 and 32.000 dollar per kjøretøy, forteller hun.
Før den sendes ut på markedet skal den testes grundig på veien og gjennomgå noen krasjtester før den blir godkjent for kjøring på veien.
Les også: Nytt system kan forutsi filbytte
En begynnende revolusjon?
Hun forteller at denne måten å produsere biler på har mange viktige fordeler, først og fremst når det gjelder produksjonsomkostninger.
– Verktøykostnadene for en 3D-trykket bil utgjør praktisk talt ingenting, og materialene som brukes for å printe bilen kan gjenbrukes. Man kan også enkelt gjøre modifiseringer, sier hun.
I tillegg blir bilen veldig lett. Bilen er printet i ABS-plast og veier ikke veier mer enn 860 kg.
Local Motors satser på å bygge mikrofabrikker forskjellige steder i verden. Til nå har selskapet tre i USA, men planlegger produksjon i flere land.
Karosseriarkitekt Arjan Strating i den tyske bilprodusenten Audi AG sier til Teknisk Ukeblad at han ikke frykter konkurranse fra Local Motors. Han har liten tro på at 3D-print kan erstatte dagens metoder i bilproduksjonen.

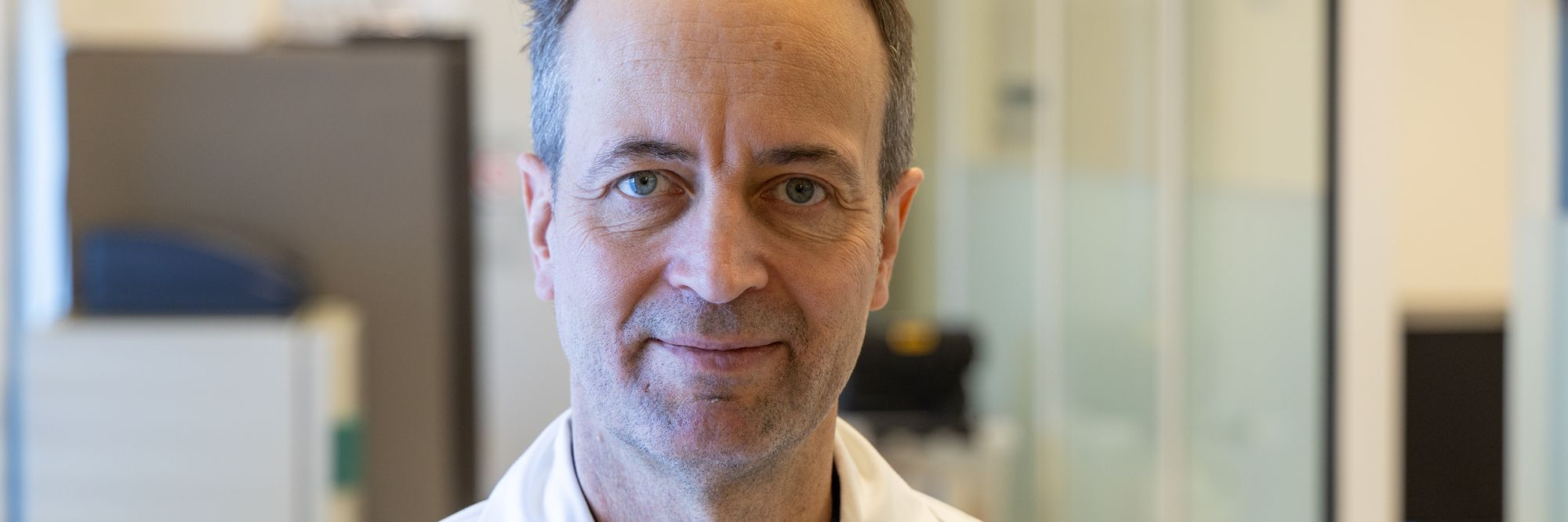
Les også: Så mye lengre bremselengde får du på glatt føre
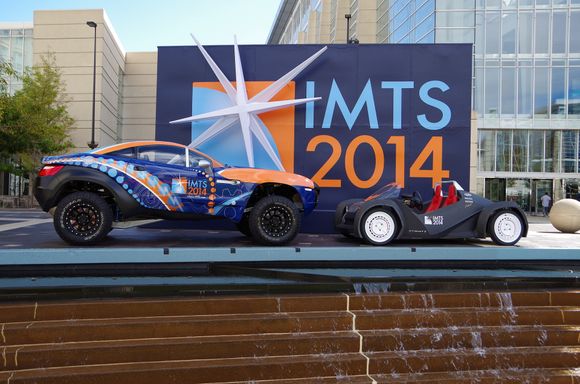
Skeptisk
Strating mener likevel at denne måten å produsere biler på kan brukes til å lage spesielle kjøretøy til spesielt bruk, der det ikke stilles de samme krav som til klassiske biler. Teknologien i seg selv ser han på som svært interessant, men til å lage en komplett bil er det ennå langt igjen.
Det har blant annet med tilgjengelige materialer å gjøre. Han har liten tro på at ABS-plast er godt nok til å produsere biler med internasjonale krav til sikkerhet og komfort.
– Det trengs masse ingeniørarbeid for å gjøre dette ordentlig, sier han.
Derimot har han tro på at 3D-print kan bli brukt til å lage enkelte komponenter, noe bilprodusentene faktisk gjør allerede.
Stratings viktigste innvending mot denne metoden er at metoden er for langsom.

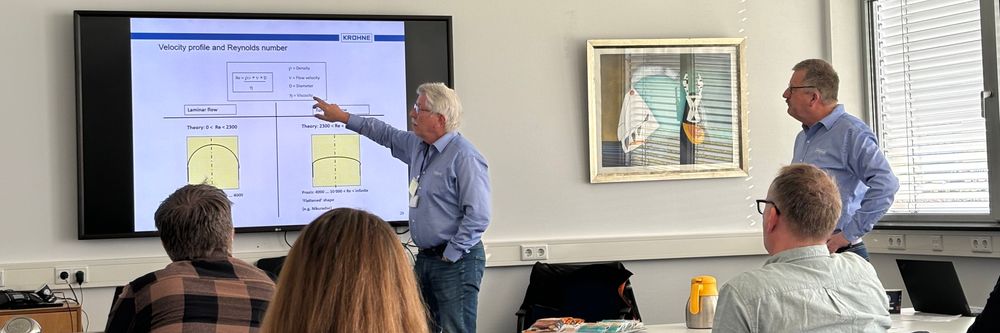
– Vi produserer 2000 biler per dag med dagens metode, mens Local Motors bruker nesten to dager på å lage et karosseri, sier han.
Les også: «Strikket metall» kan gi lavere bensinforbruk
Konkurransedyktig?
Et selskap som jobber med produksjon av bildeler i Norge er Benteler Aluminium Systems Norway A/S, som blant annet produserer støtfangere for de store bilprodusentene.
Anders Artelius, som representerer selskapet, presiserer at han ikke er noen ekspert på 3D-printing, men ut i fra det som er trenden blant kundene, har han ikke tro på 3D-print av hele karosserier. Selv kjenner han teknologien kun for stykkproduksjon hvor komplekse geometrier søkes.
Han forteller at trenden i bilindustrien er globale plattformer som for eksempel Volvo SPA eller VW MLB.
– I tillegg er design med flere materialer etterspurt. Det stiller da krav til sammenføyningsteknologier, stål mot aluminium, aluminium mot FRP, FRP mot stål, og så videre, sier han.
Ut i fra dette mener han one-piece-design er en tanke, men han er usikker på om dette er konkurransedyktig. Validering av for eksempel krasjytelse er ifølge ham noe som krever mye ressurser.
Les også:
Tesla-sjefen: – Vi skal lage billigere elbil enn GM