KONGSBERG: I prosjektet Knowledge Based Development (KBD) har man tatt det beste fra bilindustri, forsvarsindustri og subsea.
De fire bedriftene Kongsberg Devotek, Kongsberg Automotive, Kongsberg Defence Systems og FMC Technologies har i tre år samarbeidet med forskere for å utvikle KBD-programmet.
Resultatene er så oppsiktsvekkende gode at bedriftene nå vil implementere dette på verdensbasis.
Les også: Er ineffektive ingeniører årsaken til høye kostnader i Nordsjøen?
Færre ingeniørtimer
– Vi har oppnådd raskere produktutvikling og klart å gjøre kunnskapen mer uavhengig av enkeltpersoner i bedriftene, sier Leif Næss i NCE Systems Engineering. Han har vært koordinator for programmet. Daglig leder Torkil Bjørnson i NCE Systems Engineering som tok initiativet er ikke snauere:
– Denne nye arbeidsmetodikken kan bidra til å effektivisere hele den norske teknologiindustrien. Og samarbeidet er nå utvidet til å inkludere de sterke industriklyngene på Møre, Raufoss og Sørlandet.
Direktør i Kongsberg Devotek, Frode Bergan, har ledet forskningsprosjektet. Han sier at målet med programmet ikke har vært å kutte antall ingeniørstillinger, selv om dette handler om effektivisering.
– Da vi startet, var det mangel på ingeniører, så målet vårt var å få gjort mer med de samme folkene. Ved å etablere grupper fra flere bedrifter oppdaget vi at vi slet med mange av de samme problemene. Jo fortere vi kan identifisere kunnskapsgap, jo raskere oppnår vi innovasjon, sier Bergan.
Les også: Statoil: – Nå gjør våre ingeniører mye av jobben vi tidligere satte ut


Intern motstand
KBD-programmet er egentlig en videreutvikling av Lean Product Development som har vært mye brukt av Toyota i Japan og i amerikanske bedrifter.
– Vi har en helt annen og flatere struktur. Selv om de fire bedriftene vi representerer ville det samme, hadde vi helt forskjellig angrepsvinkel. Kongsberg Defence jobber mye ovenfra og ned fordi forsvarsprodukter har lang omløpstid, FMC jobber mer på prosjektbasis, mens Kongsberg Automotive har et sterkere komponentfokus, sier Bergan.
Han legger ikke skjul på at det har vært noe motstand mot denne måten å jobbe på blant noen ansatte.
– Det vil alltid være en kamp mot endringer og nye prosjekter, men etter hvert har samtlige involverte forstått at dette har stor effekt.
Programmet startet med små team i hver bedrift og involverte etter første året 50–60 ansatte. Etter tre år er 250 ansatte involvert i programmet. Samtlige bedrifter er enige om at en viktig betingelse for å lykkes er å ha forankring i toppledelsen. Samtidig mener de en viktig suksessfaktor er at dette er et program som blir implementert først på mellomledernivå.
– Til å begynne med ville ingen si noe om egne problemer, men nå vil alle dele alt. Alle har en forståelse for at dette handler om å bli mest mulig konkurransedyktig per ingeniørtime, sier Bergan.

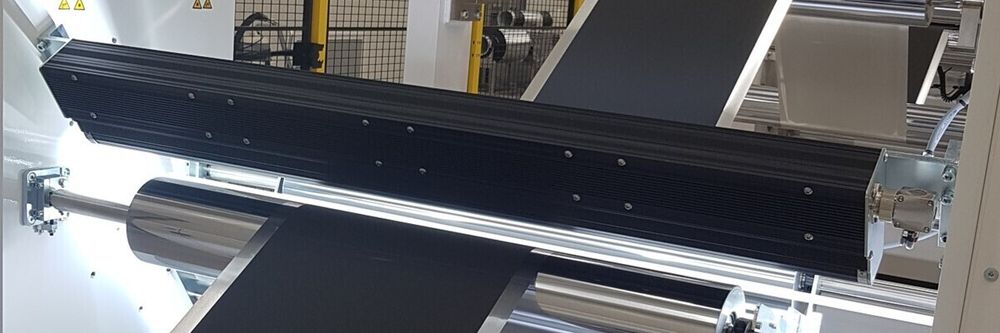
Les om: Dette er Norges smarteste industribedrift
Alt på A3-ark
Det har vært arrangert opp til 200 møter i prosjektgruppa. Hver bedrift har hatt sin pilot. Metodikken har derimot vært ulik fra bedrift til bedrift. All metodikk er blitt oppsummert på et A3-ark. At det skal oppsummeres så kort og konsist, er et viktig poeng.
– Vi hadde ikke peiling på dette før vi begynte i 2008. Finanskrisen utløste behovet, vi hadde behov for å ivareta kunnskap, sier Ivar Haug som har ansvaret for forskning og utvikling i Kongsberg Automotive (KA).
Selskapet har nå ca. 10.000 ansatte i 25 land.
– Hvordan måler dere effekten på dette?
– Det er en utfordring, men viktigst uansett er bunnlinja. Vi har fått nye store ordrer ved å bruke denne metodikken. Når vi viser A3-arket med fakta til kunder og forklarer dem fordeler og ulemper med et nytt girsystem, er det lett å forstå, sier Haug. KA leverer utstyr til alle de største bilfabrikantene, både laste- og personbilfabrikanter.
Les om: 9 grunner til at prosjektet feiler før det engang har begynt
Lært av Toyota
Både Haug og Bergan har hentet erfaringer fra Toyota som regnes som verdensledende på arbeidsprosesser. For noen år siden var Devotek invitert til Toyota for å utvikle et girskiftesystem på et såkalt «hemmelig prosjekt».
– Vi var der en uke, men måtte jobbe alene i et rom for oss selv. De ville ikke vise oss sine A3-ark til tross for at vi var invitert fordi de ville lære av oss. Vi var med helt til siste pilot, men da fikk vi ikke være med lenger, sier Bergan.
Artikkelen fortsetter under bildet.
Direktør for forretningsutvikling i Kongsberg Defence Systems, Torfinn Tobiassen, sier at KBD-programmet nå blir implementert i missildivisjonen. Der jobber 250 ingeniører med utviklingen av Joint Strike Missile (JSM) for kampflyet F-35. 90 prosent av bedriften dreier seg om dette produktet.
Les hvordan: Slik kan norske bedrifter frigjøre tusenvis av arbeidstimer
Dokumentbasert
– Vi jobber veldig dokumentbasert og med det vi kaller «amerikanske» prosesser innen systems engineering. Folk sliter med å finne igjen det de søker etter. Nå har vi etablert færre strukturer og gjort det enklere å skrive dokumenter. Vi har også bestemt at alle fagdisipliner skal ha innsyn i dokumentbasen, for første gang sitter nå software- og hardwaremiljøene sammen for å diskutere. Det gjorde de aldri før, sier Tobiassen.
Han tror Kongsberg Defence først om fem–seks år vil se den største effekten av denne måten å jobbe på siden de har så lang tidshorisont på sine produkter.