Når vi puster ut og CO2 går ut gjennom lungene, så er det resultatet av en av de raskeste kjemiske reaksjonene vi kjenner.
Reaksjonen er avhengig av en gruppe enzymer kalt karbonisk anhydrase som omdanner CO2 til HCO3 når fukt er tilstede.
Vil fjerne 95 prosent
Denne prosessen har professor May Britt Hägg og hennes forskerteam brukt 15 år på å etterlikne og overføre til en membran. Nå er målstreken svært nær.
I disse dager blir et pilotanlegg montert på Norcems sementfabrikk i Brevik, et pilotanlegg har vært forsøkt med hell på et kullkraftverk i Portugal.
Testingen er en del av et FoU-prosjekt for å redusere CO2-utslippene fra sementproduksjon. Fra fabrikken i Brevik slipper Norcem ut anslagsvis 950 000 tonn av klimagassen hvert år.
Målet er å fjerne 95 prosent av utslippene. Etter forberedelser og vurderinger valgte Norcem fire forskjellige teknologier som alle skal testes, tre ved fabrikken i Brevik og en i Tyskland, se faktaboks.
– Det målet er det de bak membranteknologien som har satt, ikke vi. Vi vet ennå ikke hvor mye CO2 vi kan fjerne, det skal testene vise, sier Liv-Margrethe Bjerge, prosjektleder for forsøkene i Heidelberg Cement.
Membraner: Det lille skillet som gjør den store forskjellen
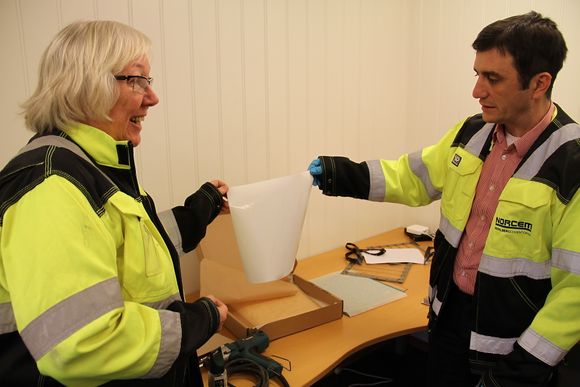
Fukt viktig
Hägg er først ute med sin løsning. Hun bruker en polyvinylmembran som ligger på en porøs bærestruktur av polysulfon. For et uøvet øye ser membranen nærmest ut som et glanset papirark.
På polysulfonen blir det påført en meget tynn polyvinylaminhinne der aminet fungerer som en katalysator for den samme kjemiske reaksjonen som skjer i lungene når vi puster.
Røykgassen føres inn med et overtrykk på om lag halvannen bar. På baksiden av membranen er det plassert en vakuumpumpe som gir et undertrykk på 300 mbar.
Fukt er en av nøklene til at denne metoden kan vise seg å bli løsningen. For membraner er fukt ofte ødeleggende for prosessen. I Häggs membranløsning er fukt en forutsetning.
– Røykgassen er stort sett mettet med fukt, og det er bra, sier Hägg.
Hulfiber eller rull
Hun forteller at når gassen har vært gjennom membranmodulen, som ikke måler stort mer enn 50x50x50 cm, regner hun med at opp til 65 prosent av karbondioksidet er tatt ut.

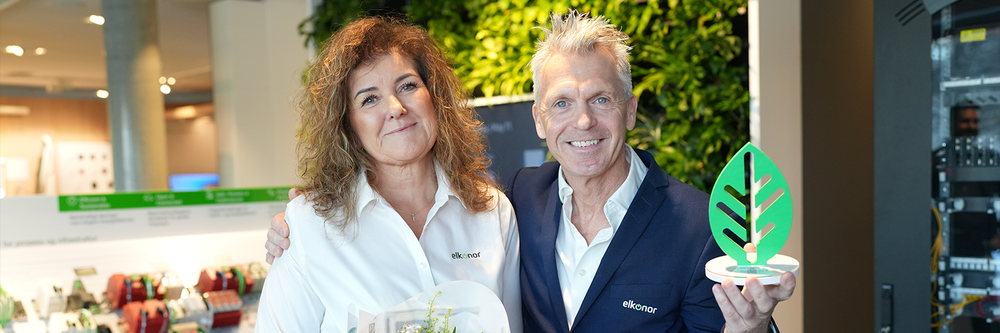
Hver modul inneholder 24 membran-ark. Gassen fra kullkraftverket inneholdt 12-13 prosent CO2 mens avgassene fra sementproduksjonen i Brevik inneholder 18-20 prosent.
– Det er nesten bedre med høyere konsentrasjon. I dette forsøket bruker vi kun en modul, for ordinær drift og store gassvolumer må vi ha flere moduler. Etter at gassen har vært gjennom den første må vi bygge opp et nytt overtrykk og så kjøre den gjennom en modul til.
Til testingen i Brevik er alle membraner håndlaget. For ordinær bruk må en membranprodusent med på laget.
Hägg forteller at de også kan benytte membran på rull, eller hulfiber, som brukes blant annet i inertgass-anlegg for å hindre brann.
Les også: Disse dyrene har superkrefter som industrien streber etter å gjenskape
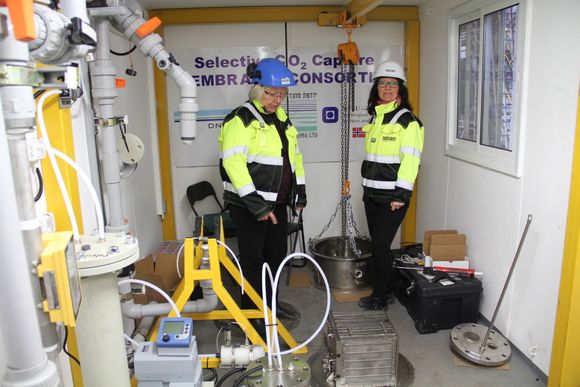
Temperaturutfordring
Membranene skal tåle eksponeringen over tid. Ved testingen i Portugal ble membranene brukt først i seks måneder for avgassene og deretter ble de utsatt for to måneder med syntetisk røykgass – dette tålte membranene godt uten å miste separasjonsegenskapene.
Men det er noen usikkerhetsmomenter. Et av dem er temperaturen, og kostnader knyttet til kjøling. Gassen fra Norcems produksjon holder en temperatur mellom 80 og 180 grader.
– Gassen må kjøles, helst ned til 40 grader, men vi har testet opp til 70 grader. Reaksjonen går hurtigere ved høyere temperatur. Vi må imidlertid finne det optimale krysningspunktet mellom temperatur og fukt helst uten å få kondensering på membranen. Det optimale er en relativ fukt på 90-100 prosent, og der ligger en usikkerhet, sier Hägg.
Sannsynlig videreføring
Liv-Margrethe Bjerge som er prosjektleder, på vegne av morkonsernet Heidelberg Cement forteller at forsøkene nå skal pågå i et halvt år. Deretter skal det vurderes om forsøkene blir videreført.
– Det ligger en fase II i planene, noe må gå galt hvis vi ikke tar dette videre. I en fase II vil vi bruke to moduler, sier Bjerge.
For Heidelberg Cement er kostnadene en viktig faktor. Membran-løsningen krever strøm til å drive viftene, eventuelt kommer kostnader til kjøling i tillegg. Flere av de øvrige teknologiene krever både damp og varme i tillegg.
Les også:
Norsk membran setter verdensrekord