Endring av karbonstrukturen i rotorblad kan gi redusert belastning på rotorblader, vindmølletårn og fundament og redusere produksjonskostnadene for strøm.
Det er konklusjonen i en doktorgradsavhandling som struktur- og designingeniør Kevin Cox nylig disputerte for ved NTNU. Cox er ansatt i ingeniør- og konsulentselskapet Necon.
Les også: Denne flytende havvindmøllen kan bli sjøsatt i Norge

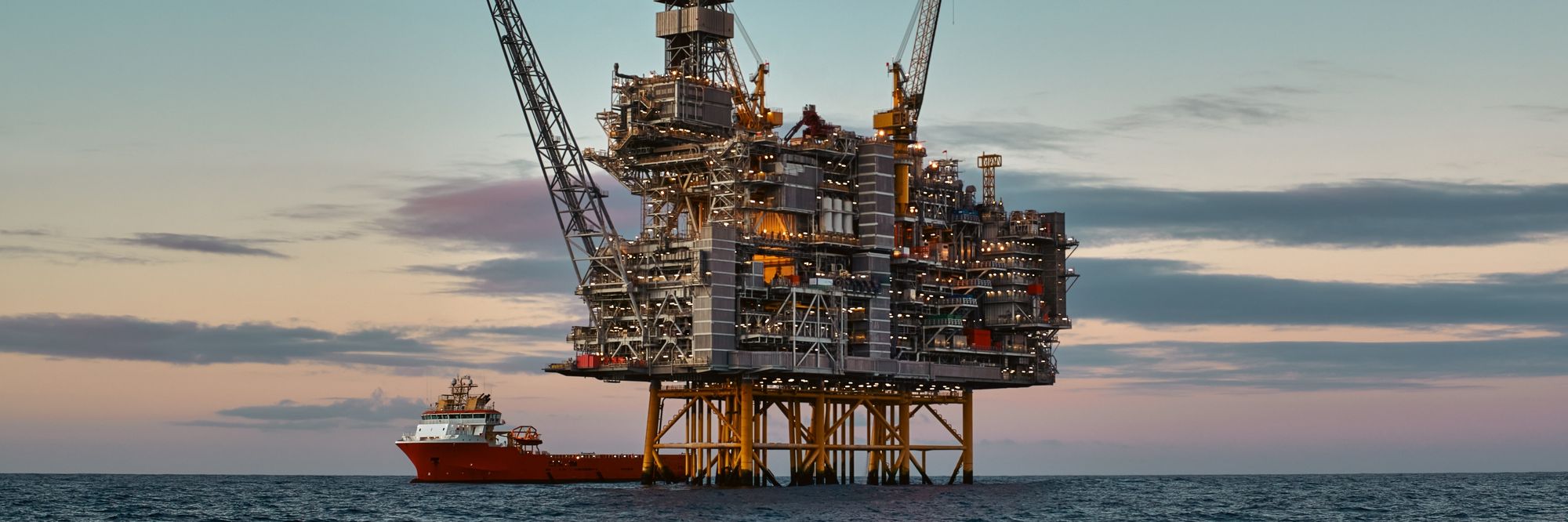
Stor slitasje
Når vinden blir kraftig, kan det føre til at belastningen på vindmølleblader og tårn blir svært stor.
For å unngå unødvendig slitasje sørger derfor sensorer og datamaskiner i dag for at vindmøllebladene vris ved hjelp av motorer for å fange opp mindre av vinden når den blir for kraftig.
Dette tar imidlertid flere sekunder. I sin doktoravhandling har Cox beskrevet en alternativ måte å hanskes med de kraftige vindkastene.
Ved å legge på lagene med karbonfiber i ulike retninger kan man gjøre bladene stivere på noen steder og mindre stive på andre. Dette kan utnyttes til å bygge blader som vrir seg automatisk når det kommer kraftige vindkast.
– Slik får du en umiddelbar, automatisk pitch control. De maksimale lastene reduseres med over 10 prosent, og utmattingsskadene reduseres, sier Cox til Teknisk Ukeblad.
Les også: Ny verdensrekord for vindmølle: 192.000 kWh på et døgn
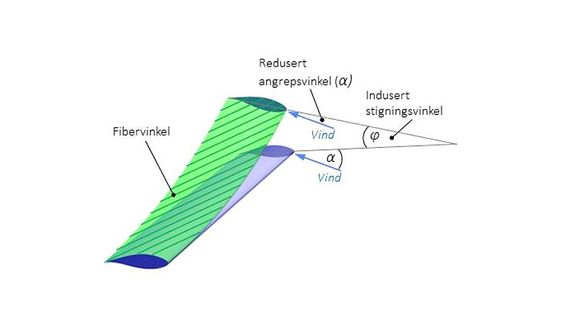
80 meter lange
Han er ikke den første som ser på dette. Det samme prinsippet ble først utviklet for rotorblader til helikoptre.
– Men de er langt mindre enn vindmøllebladene, og er utsatt for svært ulike belastninger til sammenligning. Vindturbinblader kan bøye seg flere meter fram og tilbake, sier Cox.
Offshoreturbinene blir større og større, og kan være 80 meter lange.
Det er ifølge Cox ikke dyrt å bygge på denne måten.
– Man trenger ingen nye materialer, så kostnaden ved å bygge bladene blir uforandret. Det handler kun om å endre fiberretningen i komposittmaterialene, sier Cox.
Les også: Kraftselskapene advarer mot å la plusskunder få redusert nettleie
Veier mindre
Den reduserte lasten gjør det mulig å redusere størrelsen og tyngden på turbintårnet og fundamenteringen, og man kan ifølge Cox gjøre bladene 2-5 prosent lettere.


Cox sier han ikke har gjort noen detaljert studie av hvor mye penger som kan spares, men basert på andre studier anslår han at besparelsene per kWh produsert blir seks prosent sammenlignet med teknologien som er vanlig i dag.
Teknologien passer ikke kun til store offshore-turbiner, den kan ifølge Cox også brukes på små turbiner på land med 5 meter lange blader.
Les også:
Fransk havvindpark skal teste nytt norsk fundament