Hammerfest: Fredag 25. januar startet StatoilHydro produksjonen på Snøhvit etter en lengre nedstengingsperiode. En ny oppstartsprosedyre, gav smertefri oppstart og anlegget kom i stabil drift allerede etter 25 timer. Etter 13 timer forsvat sotregnet og fakkelen ble redusert. Resultatet var at CO 2-utslippene ble redusert med 100 000 tonn.
– Vi har brukt tiden godt og kommet frem til en bedre oppstartsprosedyre som gir oss store fordeler. Vi brukte LNG fra tankene for å kjøle ned anegget før vi slapp gass fra brønnene inn i prosessen. Dermed ble driften stabil mye raskere, sier sjef for prosessanlegget, Sivert Vist.
Unngår sot
De nær 2,5 månedene StatoilHydro hadde Snøhvit-anlegget i drift sist høst, var nær en katastrofe for omdømme til StatoilHydro. Prosessen fungerte ikke som den skulle og store menger av gassen ble sendt ubehandlet rett opp i fakkelen.
Både Statens forurensingstilsyn, miljøorganisasjoner og ikke minst befolkningen i Hammerfest reagerte på den svarte røyken og store mengder av sot som dalte ned over det som en gang var verdens nordligste by. – Nå har vi fått reparert og utbedret prosessanlegget slik at ubehandlet gass ikke lenger føres til fakkel. Det som nå kommer i fakkelen er ren metansgass som ikke soter, sier informasjonssjef Sverre Kojedal.
I løpet av uke seks kommer alle prosessdelene i drift. – Fra da av vil fakkelen i prinsippet være slukket og kun brenne når det er nødvendig av sikkerhetsmessige grunner for prosessen, sier Kojedal.
Søkt om ekstra CO 2-utslipp
Til tross for de prosessmessige forbedringene, har StatoilHydro allikevel søkt om en ekstra utslippstillatelse på hele 1,5 milloner tonn CO 2 i innkjøringsperioden av anlegget. – Vi regner ikke med at vi kommer til å brenne så mye gass at vi kommer opp i denne mengden CO 2. Vi har lagt inn betydelige reserver dersom det skulle oppstå uforutsette hendelser i prosessanlegget som vil medføre fakling, sier Kojedal.

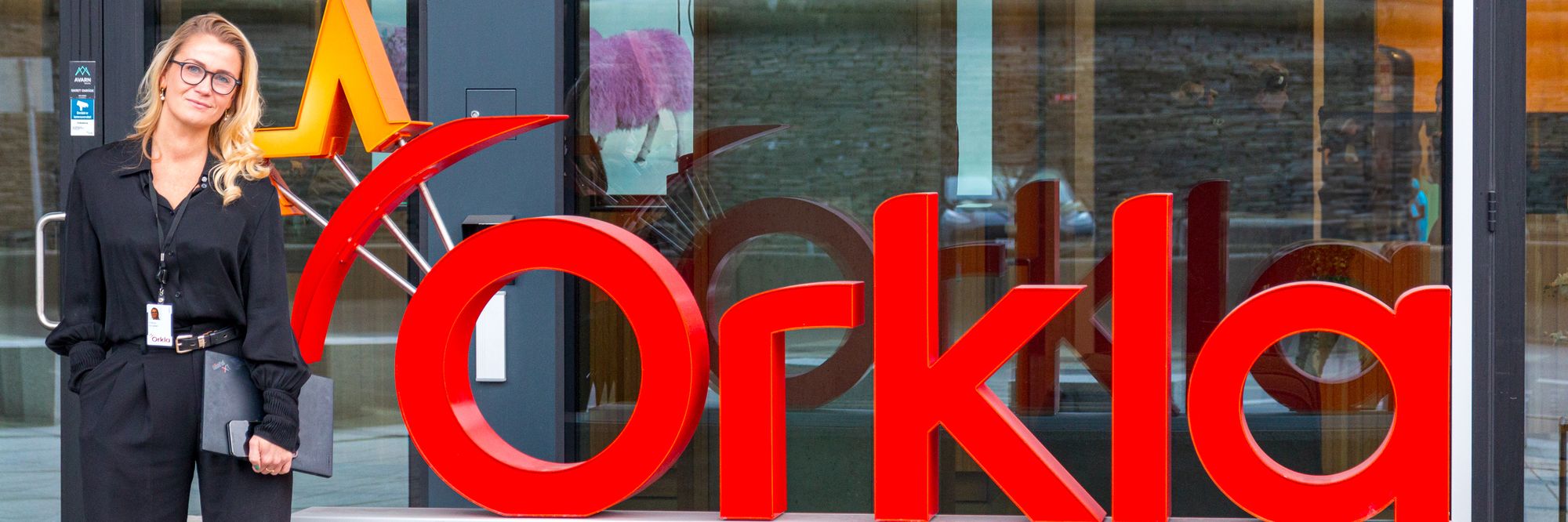
Stengt i 2,5 måneder
Oppstart fra brønnene på Snøhvit-feltet var 21 august. 3. september kom første LNG til lagertank. I alt to laster med LNG ble fraktet ut fra Melkøya. Hver av disse lastene var verd rundt 200 millioner kroner.
Men i begynnelsen av november inntraff det som ikke skulle skje. Sjøvann kom inn i en av kjølekretsene på LNG-fabrikken, og hele anlegget måtte stenges ned. Først fredag 25. januar kom driften i gang igjen.

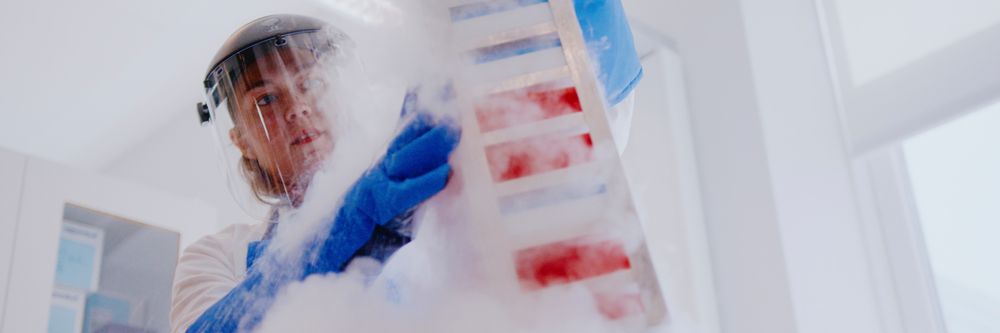
Rask oppstart, redusert produksjon
Men denne gang med en langt roligere oppstart uten problemer av betydning. Allerede etter 25 timer kom LNG inn på lagertankene, og anlegget gikk med en produksjonskapasitet på nær 60 prosent. – Nå går anlegget stabilt uten feil, og vi regner med å kunne øke produksjonen til noe over 60 prosent i løpet av begynnelsen av februar, sier Sivert Vist. Han er ansvarlig for prosessanlegget.
Under StatoilHydro kapitalmarkedsdag kunne ikke konsernsjef Helge Lund love full produksjon fra Snøhvit før i 2009. Det skyldes i all hovedsak problemer med nedkjølingsprosessen i LNG-anlegget hvor gassen bringes ned fra + 10 0C til – 163 0C ved atmosfærisk trykk, for å holde naturgassen (metan) flytende slik at den kan transporteres med skip.
Tre trinns nedkjøling
LNG-prosessen på Snøhvit går over flere trinn, hvorav de tre separate kjølekretsene i kjøletårnet er sentrale. Først ankommer renset naturgass inn i kjøletårnet med en temperatur på + 10 0C. Gjennom to store plate-finne varmevekslere så senkes temperaturen ned til minus 55 0C.
Det neste trinnet er å gjøre metangassen flytene. Det skjer i spiralvarmeveksler hvor temperaturen senkes ned til minus 90 0C. Før metanet føres inn i en ny spiralvarmeveksler for etterkjøling. Ut fra dette trinnet er temperaturen redusert til minus 155 0C
Det er med disse varmevekslerene i kjøletårnet, hvor StatoilHydro opplever prosessmessige begrensinger. – Varme-kuldefordelingen særlig i plate-finnekjølerne er gal. Dermed oppstår termdynamiske spenninger som kan skade kjølerne dersom vi kjører på full produksjon. Derfor er 60 prosent produksjonskapasitet det vi klarer, eller muligens noe over, sier Vist.
Et annet problem er at det oppstår forskjellige trykk på forskjellige steder i kjøleren. Dette medfører at det dannes væske av kjølemediet på steder hvor det ikke skulle vært væske. Kjølemediet består av propan og etan, hvor propan har en høyere væsketemperatur enn etan,og dermed kondeserer inne i kjøleren.
Må endres
Linde har en EPC-kontrakt med StatoilHydro for kjøletårnet. I denne ligger produksjonsgarantier og det er Lindes ansvar løse utfordringen med plate-finne varmeveksleren. – Linde har frist til 25 mars med å løse problemet. En annen opsjonen er å bytte den ut. Når det skjer har vi ikke bestemt, men nødvendige forbedringer vil bli gjort så snart det åpner seg en mulighet for det, sier Kojedal.
Han utelukker ikke at det først kan skje i 2009. – Vi vet at Linde arbeider på spreng med å løse problemet. Vi har ikke sett på den kommersielle siden av dette enda, fordi vi konsentrerer oss først og fremst med å få anlegget i orden, understreker Kojedal.
Kan droppe planlagt stans
Også i de store spiralrørskjølerne er det termodynamiske problemer. Temperaturen er for høy i kjernen av kjøleren og for lav i ytterkant. – Vi har identifisert årsaken til problemet og er i en fase hvor vi må kvalifisere de tekniske utbedringene som må gjennomføres, sier Vist.
Han forteller at endringsarbeide vil gjennomføres i to faser. Først vi de se på om det er mulig å oppnå bedre kjøling ved å endre rørarrangementet, deretter å få inn nytt og forbedret utstyr. Det vil i så fall ikke skje før første halvår 2009. Endringer i rørarangementet kan gjøres under den planalgt revisjonsstansen i sommer.
– Det er ennå ikke bestemt om vi skal gennomføre denne revisjonsstansen, siden mesteparten av det arbeidet vi plana ble gjennomført under stansen nå i vinter. Derfor kan det være like viktig å kjøre anlegget slik det nå er for å sikre produksjon og inntekter, sier Kojedal.
Aminet drepte vannrenseanlegget
Den første oppstartsfasen avdekket en rekke problemer. Det var pumper som ikke virket som de skulle. Det oppstod lekkasjer i ventiler og i rørkoplinger og aminrensekolonnen fungerte ikke som den skulle. – Vi var forberedt på at det skulle oppstå lekkasjer og problemer med pumper og utstyr. Det skjer alltid ved oppstert av nye prosessanlegg, men at aminrensetårnet ikke fungerte som forutsatt overrasket oss, forteller Sivert Vist.
Problemet med aminrensetårnet som skal fjerne CO 2 fra brønnstrømmen, var ikke at det ikke fjernet CO 2, men at aminet forurenset det vannet som ble brukt i å vaske gassen med. Dette vannet blir siden renset i et biologisk vannrenseanlegg, og aminet tok livet av de bakteriene som renser vannet.
Årsaken er selve konstruksjonen av aminrensetårnet som består av to deler. Øverst er selve apsorpsjonsonkolonnene som tar ut CO 2 fra gassen, mens det neders er en vannvaskerdel som renser ut de siste former for urenheter fra gasstrømmen. Disse to seksjonene er delt med en klokkeformet skilleplate, som brukes for å fange opp aminenet. Denne var ikke helt ett slik at amin rant inn i rensevannet og forurenset dette. – Vi modifiserte aminkollonen under driftsstansen, slik at nå er det tett, forteller Vist.
Sjøvann inn i kjølemediet
Hovedårsak til stansen i november var sjøvannslekkasje i en varmeveksler som står i kjølekretsen for etterkjøling. Dette er en spiralkjøler hvor det oppstod lekkasje i åtte av rør. Nærmere 50 m 3 sjøvann strømmet inn i selve kjølekretsen, som dermed måtte tømmes for kjølemedium. StatoilHydro har plugget 80 rør i kjøleren for å unngå nye lekkasjer.
Det tok lag tid å tømme og tørke ut kjølekretsen, før anlegget igjen kunne settes i drift. – Denne kjøleren skal vi bytte ut. Heldigvis ligger ikke kjøleren i kjøletårnet slik at det er forholdvis grei tilgang, forteller Sivert Vist.
StatoilHydro har funnet en ny kjøler som er bestilt og som skal settes på plass. Den nye kjøleren har tilkoplingspunktene for rørsystemene på samme sted som den som må byttes ut. Dermed slipper StatoilHydro å bygge om rørsystemene i tillegg.
Slukker fakkelen
I løpet av uke 5 og 6 regner Vist med at det siste anleggsdelen startes opp. Det er system 27, den såkalte Lindeprosessen, hvor nitrogenet skilles fra resten av gassen. Forut for denne prossenen så kjøles naturgasssen ned med flytende nitrogen på minus 193 0C. Dette nitrogenet fjernes i en stående prosesstank, hvor gassen på minus 163 0C føres til lagertank, mens nitrogenet slippes til luft. – Når denne prosessen settes i drift, kan vi stenge ned faklingen. Fra da av vi klare oss uten at vi brenner opp varelageret vårt, sier Vist.
Undersak 1
LNG-prosessen på Snøhvit
Fordelen med den tredelte kjøleprosessen er at den er mer energieffektiv. Hver kjølekrets og kjøletrinn kan reguleres for seg. Dette blir enda enklere ved at det er elektrisk drift på kompressorene, i stedet for gassturbindrift som er det vanlige. Det krever mindre energiforbruk og gir enklere regulering av kompressorene.
Ut fra kjøltårnet kommer gassen med en teperatur på minus 155 0C. med ett trykk på 4 bar. Den siste temperatursenkingen tas ved en trykkreduksjon over en liten turbin. Den energien som tas ut her gjennvinnes med en generator.
Kjølerne er bygget i i et 67 meter høy tårn, kjøleboksen. Denne er i tillegg fyllt med pertitt, som er et slagst knust leirmateriale, som har meget gode isoleringsegenskaper.
Kuldeboksen eller kjøletårnet er kompakt, og by7r på utfordringer med vanskelig adkomst og servicevennlighet. I tilleg til at rørinstallasjonene inne i denne følger en DIN-norm som er i millimeter, mens resten av prosessystemene følger godkjent offshorespesifikasjoner som er i tommer.
Fordelen ved å ligge ved Melkøya er det konstant kalde kjølevannet på pluss 6 0C. Det gir mindre behov for kjøling av gassen. En tommelfingerregel er at for hver grad kjølevannstemperaturen senkes, forbrukes en prosent mindre av gassen for å omsettes til LNG.
Undersak 2
Reguleringstekniske utfordringer
For å starte opp anlegget bruker StatoilHydro en prosessimulator fra Kongsberg Maritime (Fantoft). Denne brukes også for å lære opp operatørene og for å finne mer optimale driftsforhold.
Prosessimulatoren er ennå ikke koplet til den aktive prosessreguleringen. De kjøres fortsatt på tradisjonelt vis, men StatoilHydro planlegger å bruke multivariabel predektiv kontroll i selve kjøringen av LNG-fabrikken etterhvert. Sivert Vist håper at det kan medføre mer stabil drift og en større produksjon enn de 2,5 millioner tonn i året som er planlagt.
Undersak 3
Hvorfor så stor fakkel
Snøhvit er et såkalt subsea to shoreanlegg hvor gassbrønnene står 143 kilometer ute i havet. Selve prosessanlegget står på land. Brønnstrømmen består av flere komponenter, blant annet naturgass, kondensat (lettolje) og propan og butan. For å hindre at det dannes hydrater (ispropper) i røret inn til land, må det ha en minimums brønnstrøm på 60 prosent av full kapasitet pluss at det tilføres frostvæske.
Da anlegget ble startet opp fikk ikke operatørene prosessanlegget til å behandle så store mengder gass. Dermed måtte store deler av brønnstrømmen sendes i fakkel, til ergrelse for mange i Hammerfest.
En følgene har vært at båteiere i distriktet har fått nye kallesjer på grunn av at de gamle ble sotet ned.
Faklingen kunne for en stor del vært unngått dersom det hadde vært to gassrør fra Snøhvit inn til Melkøya. Da kunne StatoilHydro ha kjørt overflødig gass i retur, og dermed også opprettholdt full brønnstrøm. Dette er en løsning som er brukt på Ormen Lange under oppstarten av anlegget Gossen.