Teknologien er tiltenkt store skip, men viste seg å gjøre produksjonen av armeringsstål i Mo i Rana mer lønnsom
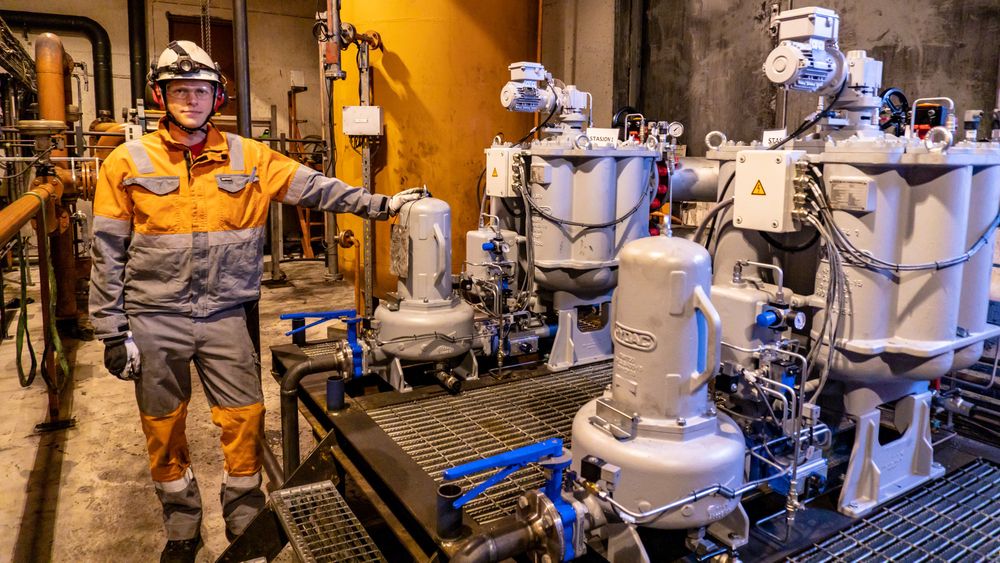
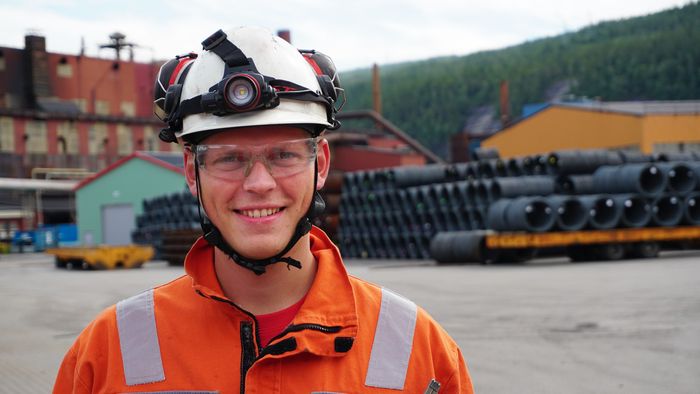
– Den nye filterløsningen har vært enormt gunstig og kostnadsbesparende for oss. Både innkjøp av utstyr og montasje vil sannsynligvis være tjent inn på under ett år.
Det forteller Henrik Limstrand, som er teknisk sjef i Celsa Armeringsstål. Her i Norges største gjenvinningsbedrift i Mo i Rana produserer de massive mengder armeringsstål som er 100 prosent skrapbasert. Årlig gjenvinner de cirka 700.000 tonn armeringsstål, eller to Eiffeltårn ukentlig.
– Denne leveransen må jo være dårlig butikk for Hydac, sier han med et glimt i øyet bak vernebrillene, mens han viser vei gjennom det 87.000 kvm. store valseverket. Celsa har nemlig vært en storforbruker av Hydacs filterelementer i en årrekke.
Enormt forbruk av filterelementer og olje
Som teknisk sjef i Celsa har Henrik jobbet mye med effektivisering og forbedringsarbeid knyttet til utstyr her på valseverket. Under et besøk fra Hydac for to år siden fortalte han om de store utgiftene de hadde knyttet til filterelementer som måtte byttes opptil flere ganger daglig.
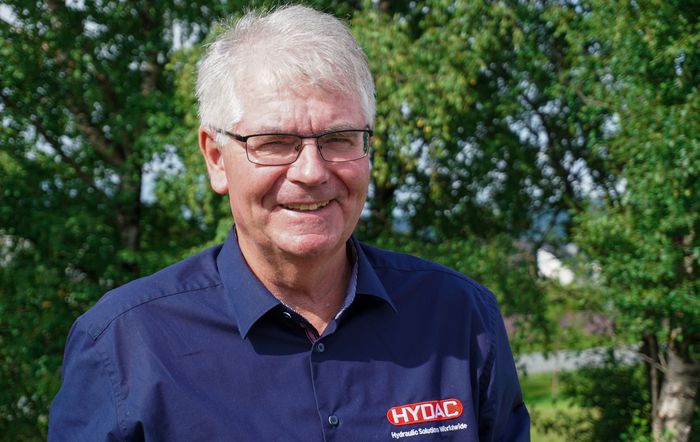
– Det gamle oljesystemet vårt var fra 1995, og hadde med årene fått betydelig større oljegjennomstrømning på grunn av økt produksjon. Filterenheten vi hadde gikk veldig fort tett. Det gjorde at vi måtte kaste veldig mye olje, og hadde enorme utgifter knyttet til bytte av filterelementer, som ikke var en bærekraftig løsning for Celsa, sier Henrik.
– Vi snakker nok kostnader på godt over millionen i året bare på dette, røper han.
Han legger til at bare én times produksjonsstopp kan bety opptil 140 tonn i tapt produksjon for valseverket.
Henrik tok derfor kontakt med deres salgsansvarlige i Hydac, for å høre om han hadde noen tips til produkter som kunne få ned både utgiftene og oljeforbruket deres.
– Da Henrik fortalte meg om det voldsomme filterforbruket deres, skjønte jeg at dette var en situasjon som de ikke kunne leve med over tid. Løsningen deres med det gamle filteret var nødt til å byttes ut, forteller salgsingeniør i Hydac og kundeansvarlig for Celsa, Tom Levorstad.
Hydac Norge er heleid av det tyske familieselskapet Hydac International, som leverer egenutviklede, patenterte løsninger innen hydraulikk. Det gamle filteret hos Celsa, NFD5200, var også levert av Hydac i sin tid.
Monterte automatfilter for store skip på valseverk
Tom tok utfordringen fra Henrik på strak arm, og hentet med seg filtereksperter fra både den tyske fabrikken og det norske kontoret til Hydac. De gjorde en rekke oljeanalyser, som viste at det var de litt større partiklene i oljen som var hovedproblemet.
– Etter hvert kom ideen: Hva med å sette inn et automatfilter? spør Tom retorisk.
Videre forteller Tom at neste steg ble å involvere en kollega som jobbet med store skip og hadde utviklet automatfilteret RF9, for å se om det var mulig å bruke på valseverket. Automatfilteret var i utgangspunktet utviklet for smøreolje på store skip og andre tjukke oljer.
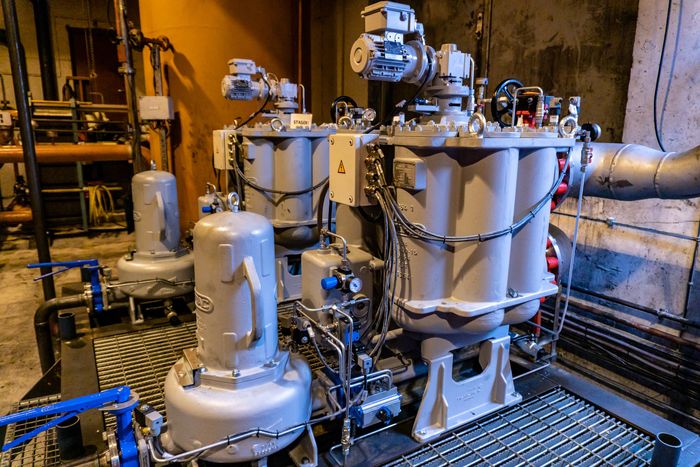
– Samtidig som filterløsningen skulle fungere tilfredsstillende og filtrere godt nok, så var hele tiden hovedmålet å gi økonomisk gevinst for Celsa. Vi holdt på i to år fram og tilbake, så Celsa fikk tid til å vurdere løsningen på en teknisk god måte.
Celsa landet til slutt på løsningen med automatfilteret RF9, og monteringen ble gjennomført under ferieavviklingen i påsken i år. De gjorde flere oljeanalyser både før og etter installasjonen for å se effekten.
– Den gamle løsningen filtrerte på 10my, mens dagens filtrerer på 15my. Alle partiklene som blir filtrert ut spyles ut av automatfilteret og over i et eget manuelt STU-filter levert i samme delen, mens den rensede oljen går tilbake til tanken for gjenbruk hele tiden, forklarer Levorstad.
– Vi har fortsatt ikke hatt behov å bytte STU-filteret nå et halvt år etter installasjonen, skyter Henrik fornøyd inn.
– Den nye løsningen krever også mye mindre oppfølgning av operatørene, og leverer minst like god kvalitet på rengjøringa, fortsetter han.
– En skikkelig vrien problemstilling
Forretningsutvikler og produktekspert i Hydac, Hans-Jacob Samuelsen, forteller at utfordringen i dette prosjektet var at det gamle filteret “spiste opp” altfor mye av trykket Celsa trengte ute i smøresystemet.
– Dette er et svært smøreanlegg til valseverket, og for at smøresystemet skal virke må de ha et visst minimumstrykk på oljen ut i systemet. De filterelementene som sitter inne i filtrene får høyere motstand jo mere møkk de fanger opp. For å unngå å tape for mye av trykket de trengte, måtte elementene kastes når de var fylt opp til bare 20 prosent av kapasiteten, forteller han.
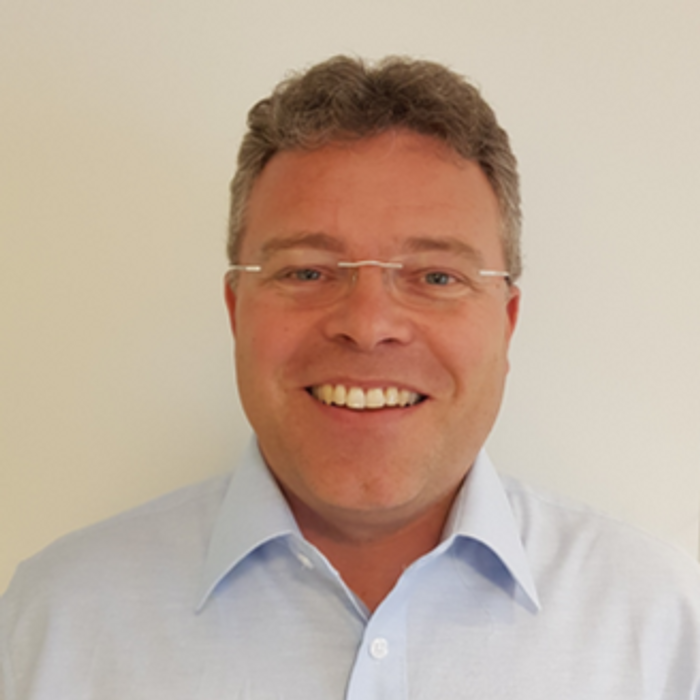
Celsa hadde ikke mulighet til å kjøre pumpetrykket høyere, slik at trykktapet i filteret ble et problem som måtte løses.
– Dette var en skikkelig vrien problemstilling. Først prøvde vi å bytte filterelementene til et annet materiale som skulle håndtere dette bedre, men det ble ikke bra nok, erkjenner han.
Å tenke kreativt, utenfor boksen, ble løsningen på problemet med filteret som hadde altfor høyt forbruk av filterelementer.
– Filteret vi satt inn var egentlig tiltenkt andre applikasjoner som smøreoljer på skip og ganske tjukke oljer, men viste seg å passe godt inn her, forklarer Samuelsen, og fortsetter:
– Måten det selvrensende filteret virker på, er at det bruker litt av smøreoljen til å rense elementene. Du hiver egentlig litt olje for å rense disse elementene, og det er jo ikke spesielt miljøvennlig – den vil man gjerne ta vare på. Så da går renseoljen gjennom et finere filter, så oljen kan tas tilbake i kretsen og brukes igjen.
Han forteller videre at Celsa også hadde utfordringer med masse vann i oljen som kom i retur, som gjør at slike filterelementer tetter enda raskere.
– Derfor har vi også levert en enhet for å fjerne vann og senke vannivået i oljen, sier han.
Henrik forteller at de er ikke kunne vært mer fornøyde med leveransen.
– Hydac har vært til god hjelp under monteringen og til å forstå systemet i etterkant. De svarer alltid momentant på henvendelser våre når vi har spurt om hjelp, avslutter Henrik i Celsa.