En kombinasjon av eksperimenter og datasimuleringer har kunnet forklare hvorfor 3D-trykte titan- og stållegeringer har sine respektive høyeste og laveste styrke vinkelrett på trykklagene.
3D-printing eller lagvis produksjon er en raskt voksende og svært lovende teknologi som har vært gjennom en betydelig utvikling de siste årene. Spesielt innen metalliske komponenter er det et veldig stort potensial, men også betydelige tekniske utfordringer.
En lagdelt produksjonsprosess, hvor hårtynne lag av metallpulver smeltes sammen av en laser, muliggjør kompliserte komponentgeometrier som man hittil ikke har kunnet produsere. Men også fra et miljøperspektiv åpner 3D-print av metall for vidtrekkende materialbesparelser som kan ha en betydelig effekt på globalt ressurs- og energiforbruk.

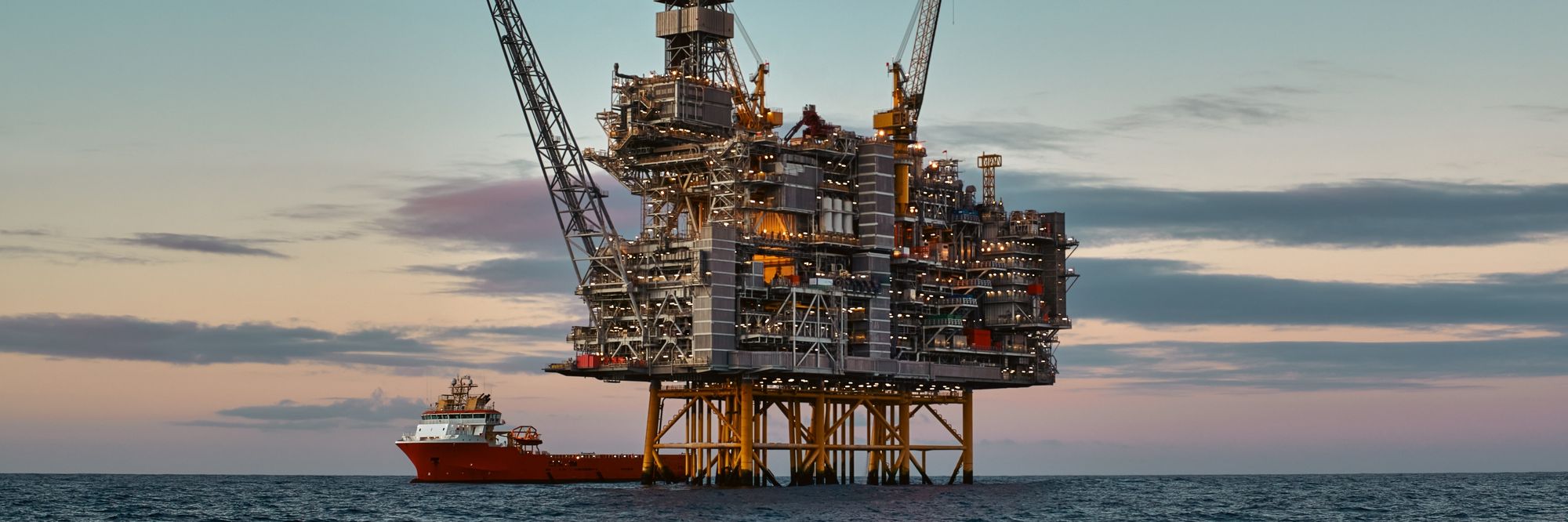
Å bygge lett er ikke bare et spørsmål om vekt eller økonomi alene, men også av miljømessig betydning.
Paradigmeskifte
Metall 3D-printing muliggjør et paradigmeskifte, som gjør at komplekse lettvektskomponenter ikke lenger er dyrere å produsere enn enkle geometrier, tvert imot.
Produksjonskostnadene her bestemmes hovedsakelig av materialvolumet, nesten uavhengig av den geometriske kompleksiteten.
Men et høyt ambisjonsnivå når det gjelder materialbesparelser gjør styrken til de trykte komponentene mer kritisk.
Det innovasjonsfondstøttede prosjektet AM-LINE 4.0 har bl.a. finansiert ph.d.-prosjektet «Mikromekanikk av 3D-printede metaller» som en del av DTUs forskningsaktiviteter innenfor opprettelsen av en såkalt digital tvilling av lagvis produksjon av metalliske komponenter.
Doktorgradsprosjektet fokuserte på å lage digitale modeller av et representativt utvalg av 3D-printede metaller (se figuren under) som kan brukes til å simulere den mekaniske oppførselen til det virkelige materialet, selv når belastningen overstiger materialets flytegrense.
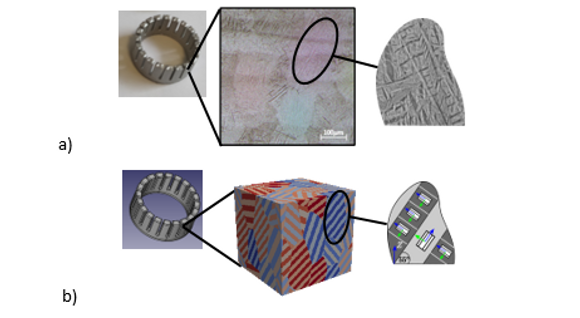
På denne måten kan styrken til lagvis produserte komponenter forutses med større sikkerhet ved å ta høyde for en betydelig retningsbestemt materialstyrke. Dette forutsetter imidlertid en dyp forståelse av materialenes indre mikrostruktur.
Metaller som brukes som byggematerialer består av korn som typisk har en størrelse mindre enn 0,1 mm. Hvert korn er en krystall hvor atomene i metallet er ordnet i et såkalt gitter. Men selv om alle korn har samme enkle og veldefinerte gitterstruktur, er gitterorienteringen forskjellig fra korn til korn.
Irreversible deformasjoner
Disse orienteringene er viktige fordi krystallene deformeres som en bunke med spillkort, der atomene glir i forhold til hverandre i bestemte retninger. Når en ytre belastning påvirker et metall over dets flytegrense, oppstår således irreversible deformasjoner hovedsakelig i korn med en spesiell orientering av de såkalte glideplanene i forhold til belastningen.
I lagvis produserte metaller, hvor kornoppbyggingen er et komplisert resultat av den lagvise produksjonsprosessen, forekommer visse krystallorienteringer i forhold til utskriftsretning oftere enn andre orienteringer. At kornene ikke lenger er tilfeldig orientert er altså årsaken til retningsavhengige materialegenskaper.
Denne såkalte materialanisotropien er typisk i størrelsesorden 5-10 %, noe som betyr at hvis du tester de printede metallene i en tilfeldig retning, er det en sjanse for at du enten under- eller overvurderer den faktiske bæreevnen.

Prosjektets konklusjoner er derfor spesielt viktige når det gjelder kvalitetssikring, fordi retningsavhengige materialegenskaper av hensyn til sikkerheten skal måles og karakteriseres i mest kritisk retning. Men når man kjenner materialets anisotropi, kan man også utnytte den.
Du kan skrive ut en komponent i én retning slik at styrken på materialet er høyest i den retningen hvor den største belastningen oppstår. Videre kan anisotropien som observeres i materialtester brukes til «reverse engineering» av materialets indre struktur.

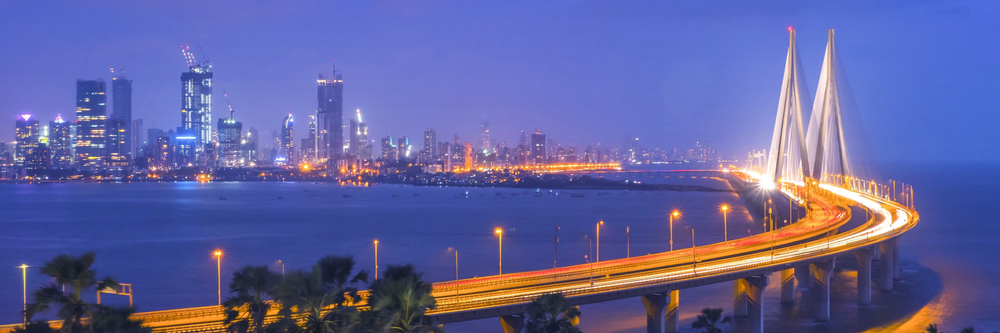
Ved å kombinere input fra materialtester og mikroskopibilder har doktorgradsstudent Kinga Somlo, som nå er ansatt ved Institutt for konstruksjonsteknikk ved NTNU, faktisk klart å utvikle modeller av mikrostrukturen til materialene for to typiske lagvis produserte legeringer, nemlig for titan og rustfritt stål.
De utviklede materialmodellene inneholder informasjon om den statistiske fordelingen av krystallorienteringer i materialenes korn, men også om krystallenes indre styrke.
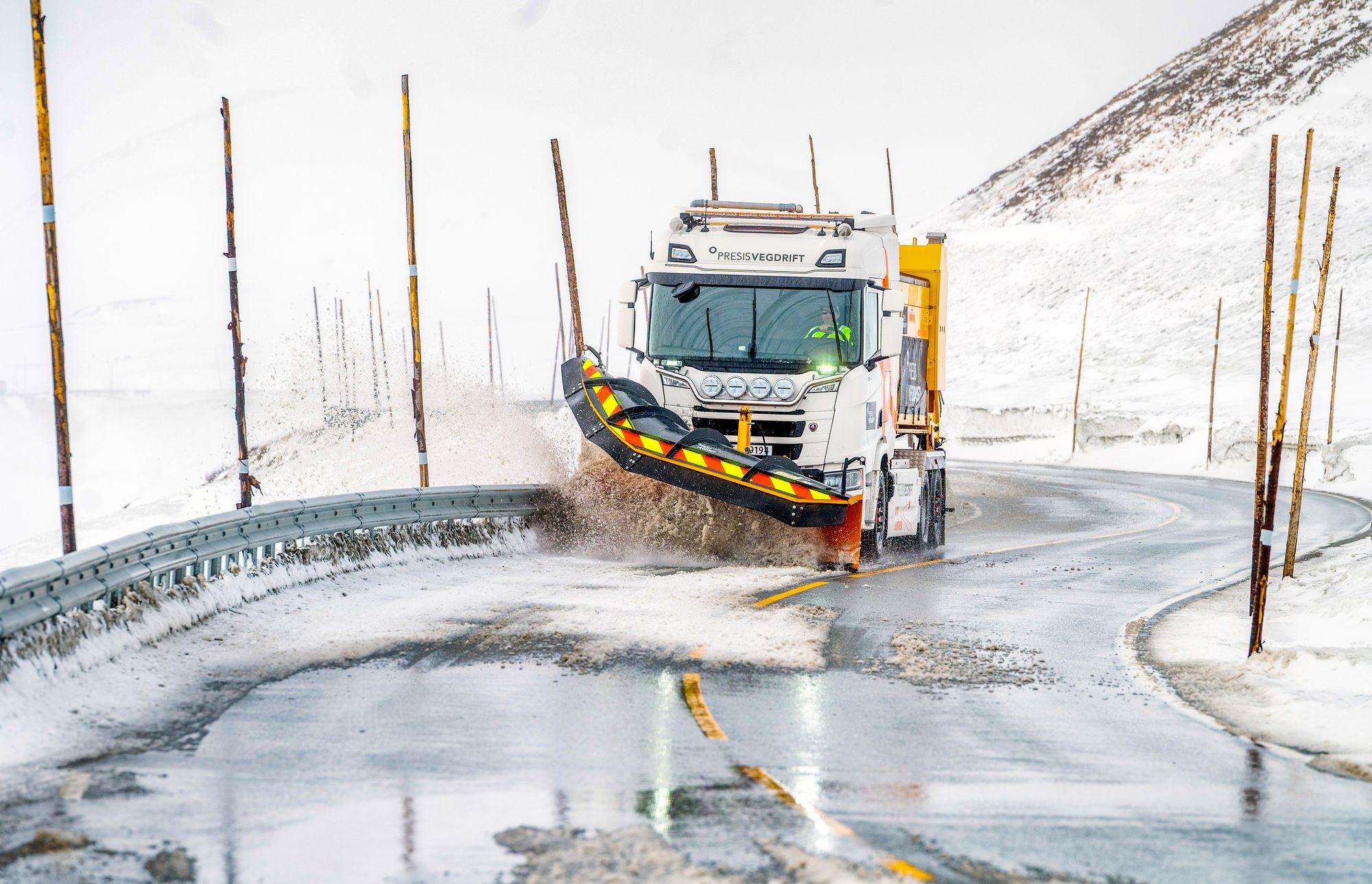
El-brøyting: Effektiv på en av Norges tøffeste fjelloverganger
Stor betydning for virtuell testing
PhD-prosjektet har konkludert med at den 3D-printede titanlegeringen er sterkest vinkelrett på retningen til printlagene, mens stållegeringen er sterkest parallelt med disse lagene. Disse observasjonene kan underbygges av datasimuleringer.
Den grunnleggende forståelsen av styrkeforholdene til lagvis produserte materialer er også av stor betydning for såkalt virtuell testing. Her simuleres et representativt utsnitt (en liten terning) av materialet under et stort antall lastkombinasjoner som er vanskelige eller umulige å gjennomføre eksperimentelt.
Denne omfattende virtuelle testingen har ført til styrkemodeller som dekker komplekse lasttilfeller langt utover de enkle eksperimentelt testede lastene, og de kan brukes til dimensjonering og simuleringer av virkelige komponenter.
Det er ikke bare flytegrensene til de 3D-printede materialene som viser anisotropi. Sprekkvekst under syklisk belastning (se figur 2) avhenger også av sprekkens retning i forhold til printlagene.
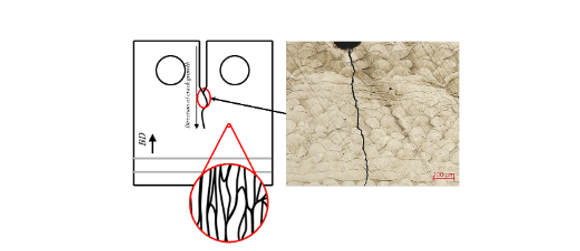
Eksperimentelle undersøkelser ved DTU har avslørt at for både titan og rustfritt stål vokser sprekker, under syklisk belastning, mer enn to ganger raskere i et plan vinkelrett på printlagene enn i et plan parallelt med disse.
Kunnskapen kan minimere risiko
Når man foretar bruddmekaniske forsøk for å sikre kvaliteten er det altså viktig å gjennomføre dem i den mest kritiske retningen for å sikre en konservativ vurdering av materialegenskapene.
Denne kunnskapen om de retningsavhengige materialegenskapene kan også utnyttes til å velge spesifikke retninger som en komponent skal produseres i, for å minimere risikoen for vekst av sprekker og dermed oppnå lengre levetid.
I tillegg til å forstå og kvantifisere de grunnleggende mekaniske egenskapene til 3D-printede metaller, som beskrevet i denne artikkelen, tar ytterligere forskningsaktiviteter ved DTU sikte på å optimalisere utskriftsprosessen, samt å forbedre 3D-printede komponenter gjennom termiske behandlinger.
Artikkelen ble først publisert av Ingeniøren.
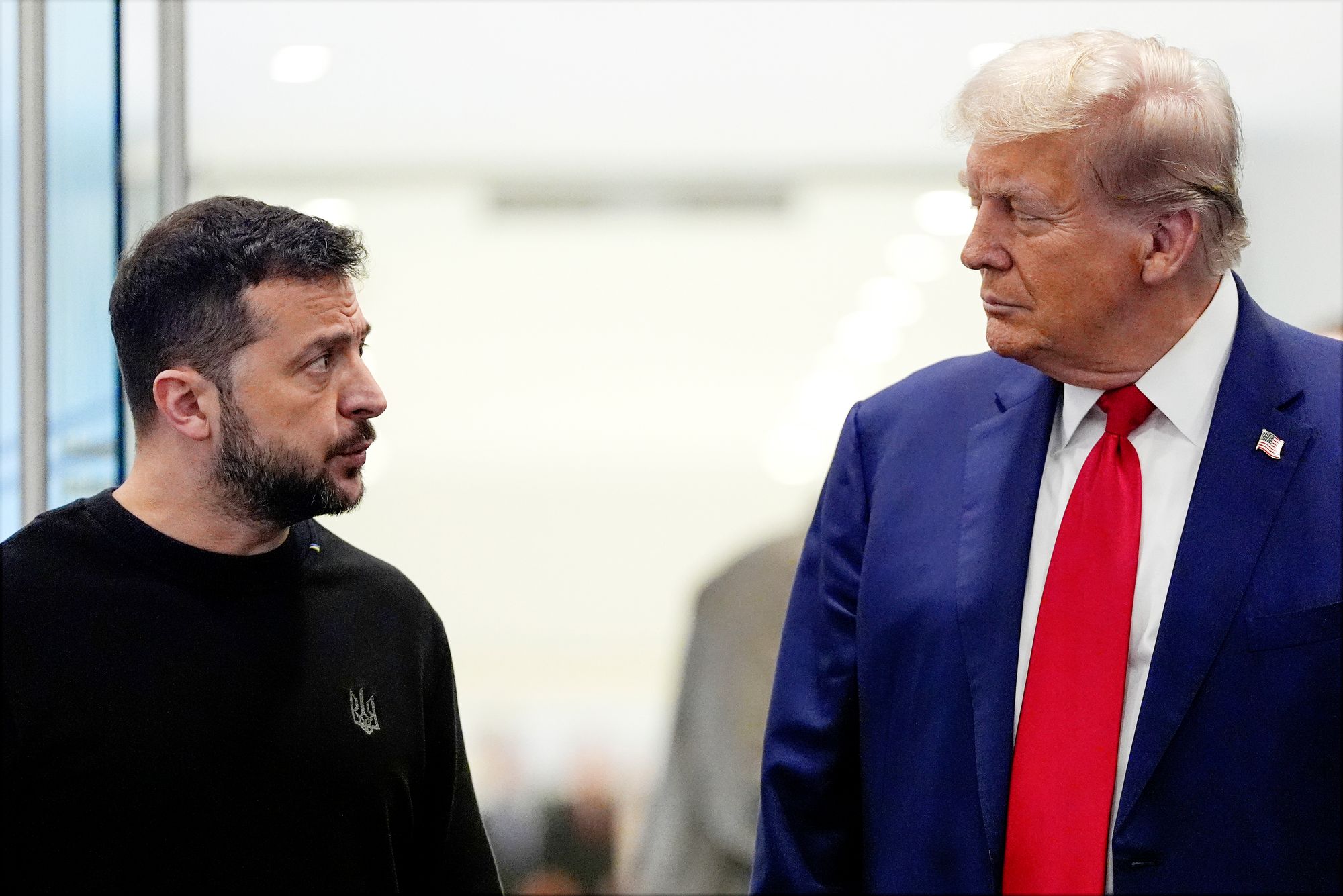
Mineral-ekspert om Trump-utspill: – Jeg forstår det ikke