Zwickau, Tyskland: Den østtyske småbyen Zwickau har lang erfaring med bilproduksjon – Sachsenring produserte sin Trabant i byen frem til 1991.
Nå er det elbiler det dreier seg om. Volkswagens Zwickau-fabrikk pumper ut biler bygget på bilgigantens MEB-plattform. Det går riktig nok i rykk og napp. Da Russland invaderte Ukraina stanset leveransene av kabler fra Leoni. Det kom på toppen av utfordringene bilindustrien har som følge av mangel på halvlederkomponenter.
Når vi slippes inn i fabrikken er det likevel ikke stillstand. Kabler leveres atter fra Ukraina, og det ruller 900 biler ut av fabrikken hver dag. Det er likevel ikke nok til å dekke etterspørselen, og fremdeles et stykke under målet om 1500 biler om dagen innen utgangen av 2020, som Volkswagen satt som mål i 2018.

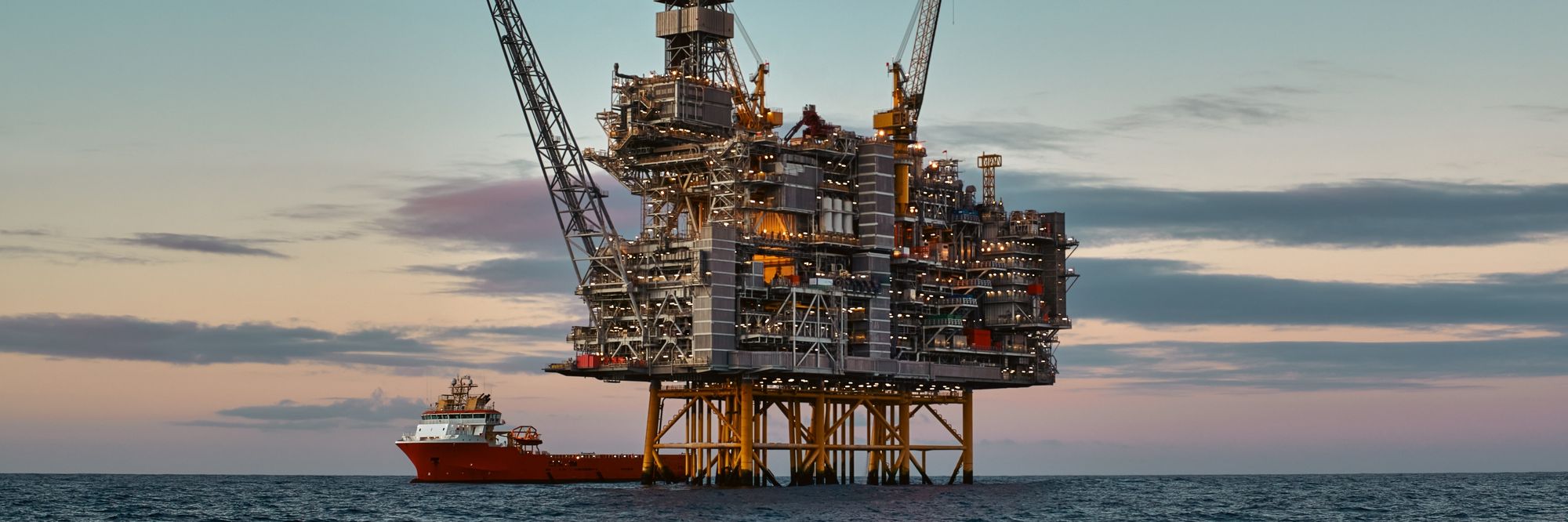
Fabrikken operer nå med to skift, og sikter mot å kunne komme tilbake til produksjonen på 1300 biler som de hadde før krigen i Ukraina brøt ut. Da hadde de tre skift om dagen, mens de nå er nede i to skift.
Oppdatert 15.6.2022: Volkswagen meldte 13. juni at de har innført et tredje skift, og at produksjonen er økt til 1300 biler om dagen.
At de enda ikke har nådd målet om 1500 biler om dagen handler om at de har startet produksjon av seks ulike kjøretøy de siste 26 månedene, og samtidig har måttet sjonglere pandemi og mangel på halvlederkomponenter.
Om det går som planlagt skal produksjonen gå for fullt neste år, med en maks kapasitet på over 300.000 biler produsert i Zwickau.
– Etterspørselen er høyere enn hva vi klarer å produsere. Vi har 12 måneders venteliste. Det er første gang jeg opplever det. Det er jo ekstremt gode nyheter for oss. Ikke for kunden som må vente på bilen, men for oss er det veldig gode nyheter, sier fabrikksjef Dr. Stefan Loth.
Loth styrer en fabrikk med 9000 ansatte, som dekker et areal på 1,8 millioner kvadratmeter. Transformasjonen til en ren elbilfabrikk startet i 2017, og den siste fossilbilen – en Volkswagen Golf stasjonsvogn – forlot samlebåndet sommeren 2020.
Elektrisk friksjon
I 2021 produserte de nær 180.000 elbiler her. Sjefen kaller det en av de største transformasjonene som noen gang er gjort i bilindustrien. Sånt skjer ikke helt uten friksjon.
– Da Herbert Diess (VW-direktør, red.anm.) i 2017 sa at elektrisk mobilitet var fremtiden var det noen av våre folk som ristet på hodet og sa «aldri i verden». Har vi infrastrukturen? Hva gjør de som bor i leilighetskomplekser, skal de ha skjøteledninger ut av kjøkkenvinduet?
I dag er alle ansatte enige om at Volkswagen har valgt rett strategi, hevder Loth.
Den enigheten har de måttet jobbe for å oppnå. Volkswagen har etablert et treningssenter for elektrisk mobilitet hvor alle ansatte må innom. Så langt har 8000 fabrikkarbeidere vært igjennom programmet, hvorav 1500 har fått sertifisering som kreves for arbeid på elektriske komponenter i spenningsnivået i bilene. Totalt er det gjennomført 20.000 treningsdager.
Målinger de har gjort viser at ansatte som på forhånd var skeptiske til elektrisk mobilitet er mye mer positive etter å ha gjennomgått treningsprogrammet. Ikke gjennom tvang, forklarer Matthias Roth, som leder Volkswagens utdanningsprogram.
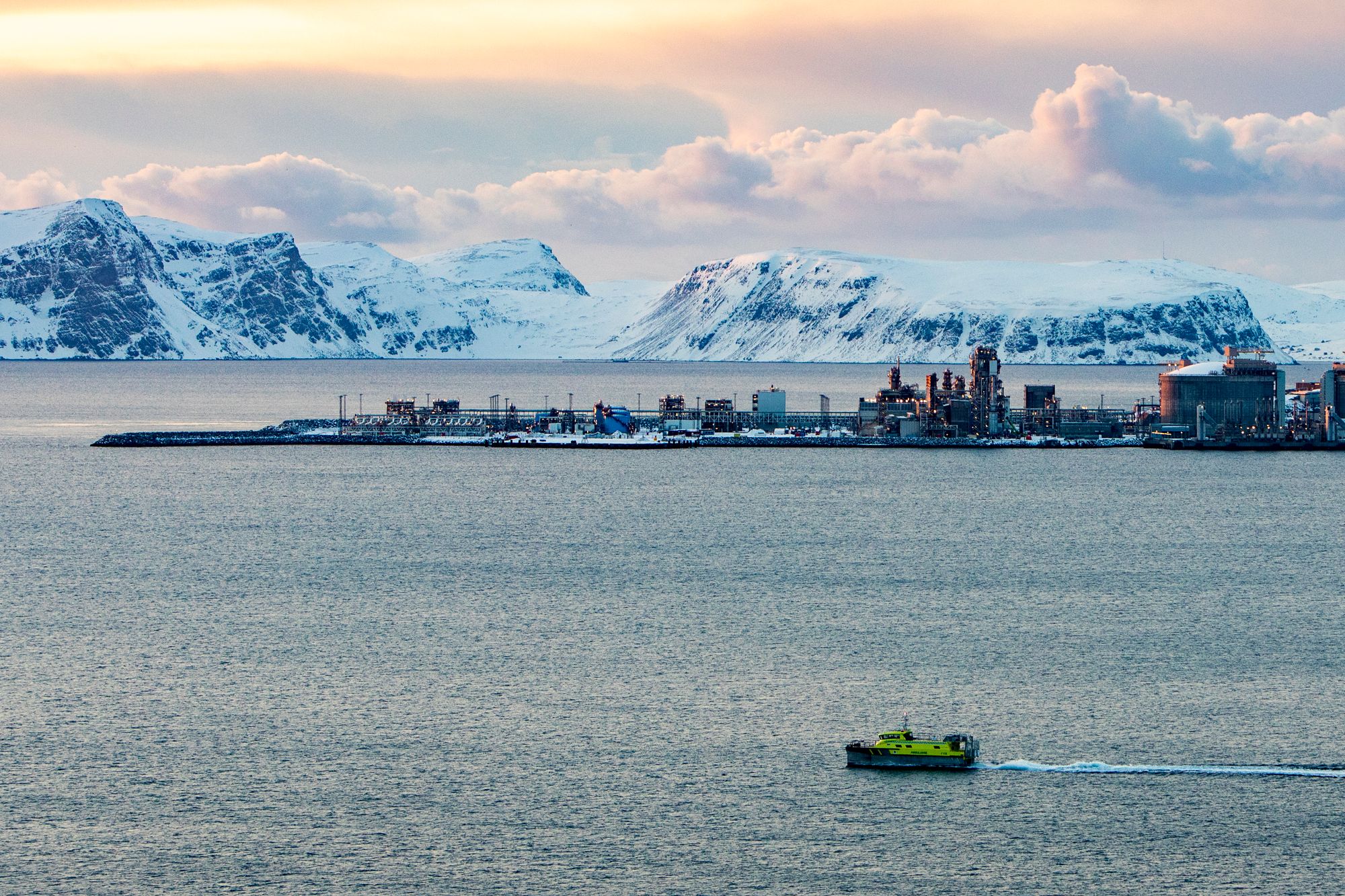
Aasland: Ulovlig å reversere elektrifiseringen av Melkøya
Det var ikke bare hos fabrikkarbeiderne det var skepsis til endringene. Spredningen i holdningene var like store hos fabrikkledelsen, forklarer Roth. De ble også pålagt å delta på treningsprogrammet.
Vi spør om treningen har gjort at alle nå er positive til endringene. Roth sier at de har høy motivasjon, at de har kommet lenger enn de forventet i 2017, og at troen på elektrisk mobilitet er høy i dag.

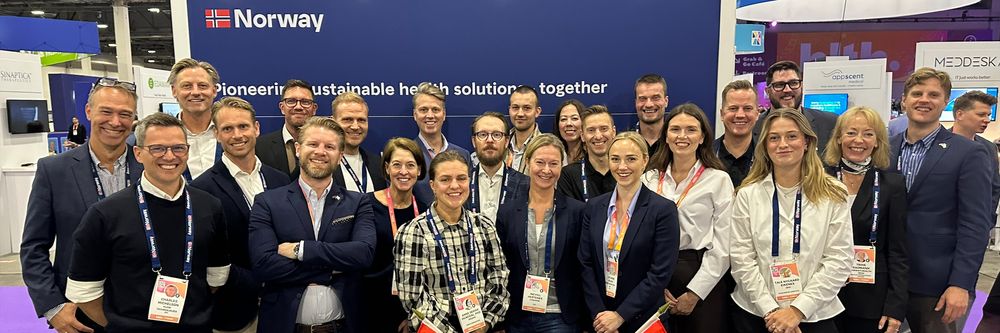
Den tekniske fremgangen har vært høy, og troen er sterk i Volkswagen. Treningsprogrammet eksporteres til andre Volkswagen-fabrikker.
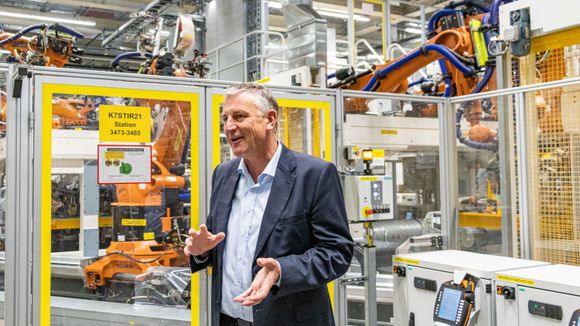
Som å pusse opp badet
Zwickau er et eksempel på den gamle måten å gjøre ting på i Volkswagen-gruppen. Å konvertere en fabrikk fra å bygge fossilbiler til elbiler må gjøres i steg og over lang tid. Elbilproduksjonen må til en viss grad tilpasses eldre produksjonsmetoder.
Det er en av grunnene til at Volkswagen-gruppens neste generasjon elbiler skal bygges i nye fabrikker bygget fra bunnen av. Den første skal komme i Wolfsburg, hvor den såkalte Trinity-generasjonen av elbiler skal i produksjon.
Vi spør fabrikksjef Dr. Loth om hvilke begrensninger de må forholde seg til når de konverterer en eksisterende fabrikk sammenlignet med å bygge en helt ny.
– Det er litt som med badet ditt. Bygger du nytt hus er det jo enkelt å bygge bad. Har du et gammelt hus må du flytte alt ut, og det nye inn. Alle som har renovert et gammelt hus vet at det er mye mer arbeid enn å sette opp et nytt hus. Det er det samme i fabrikken. Du må flytte ut, ha en strategi for menneskene og hva de skal drive med mens du bygger opp en ny produksjonslinje, du må synkronisere opptrening av folk med den nye generasjonen roboter i karosseriverkstedet, og det må synkroniseres med ferie.
– Det er ganske mye arbeid, sier Loth.
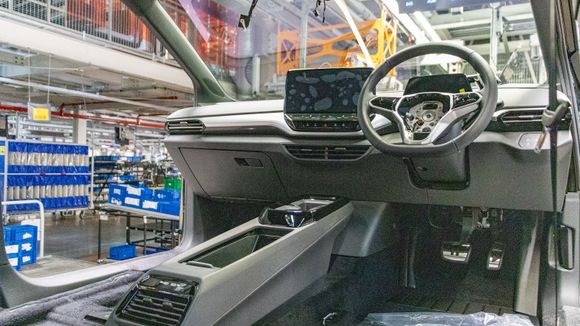
Store oppgraderinger
Det er ikke bare å bytte ut eksisterende samlebånd og produksjonslinjer med nye. Blant annet trengte de et helautomatisert system for håndtering av batterier. De måtte ha automatiserte lagringssystemer for deler. Karosseriproduksjonen måtte også utvides. Volkswagen har fått på plass en presse som kan lage karosserideler på stedet i stedet for å få dem tilsendt fra Wolfsburg.
Zwickau-fabrikken har også oppgradert samlebåndsproduksjonen med økt grad av automatisering. Før forvandlingen var 18 prosent av produksjonen automatisert med roboter. Nå er nær 30 prosent automatisert.
Blant annet gjøres nå montering av blant annet cockpit og vinduer helt og holdent av roboter. Det er produksjonssteg som normalt er arbeidskrevende når det gjøres med manuelt arbeid.
Volkswagen-sjef Herbert Diess sammenlignet høsten 2021 Zwickau med Teslas nye fabrikk i Brandenburg, og pekte på at amerikanerne brukte 10 timer på sine biler, mens Volkswagen brukte over 30. Målet er å redusere produksjonstiden til under 25 timer i løpet av året. Akkurat nå bruker de 28 timer – et godt første steg, mener Diess.
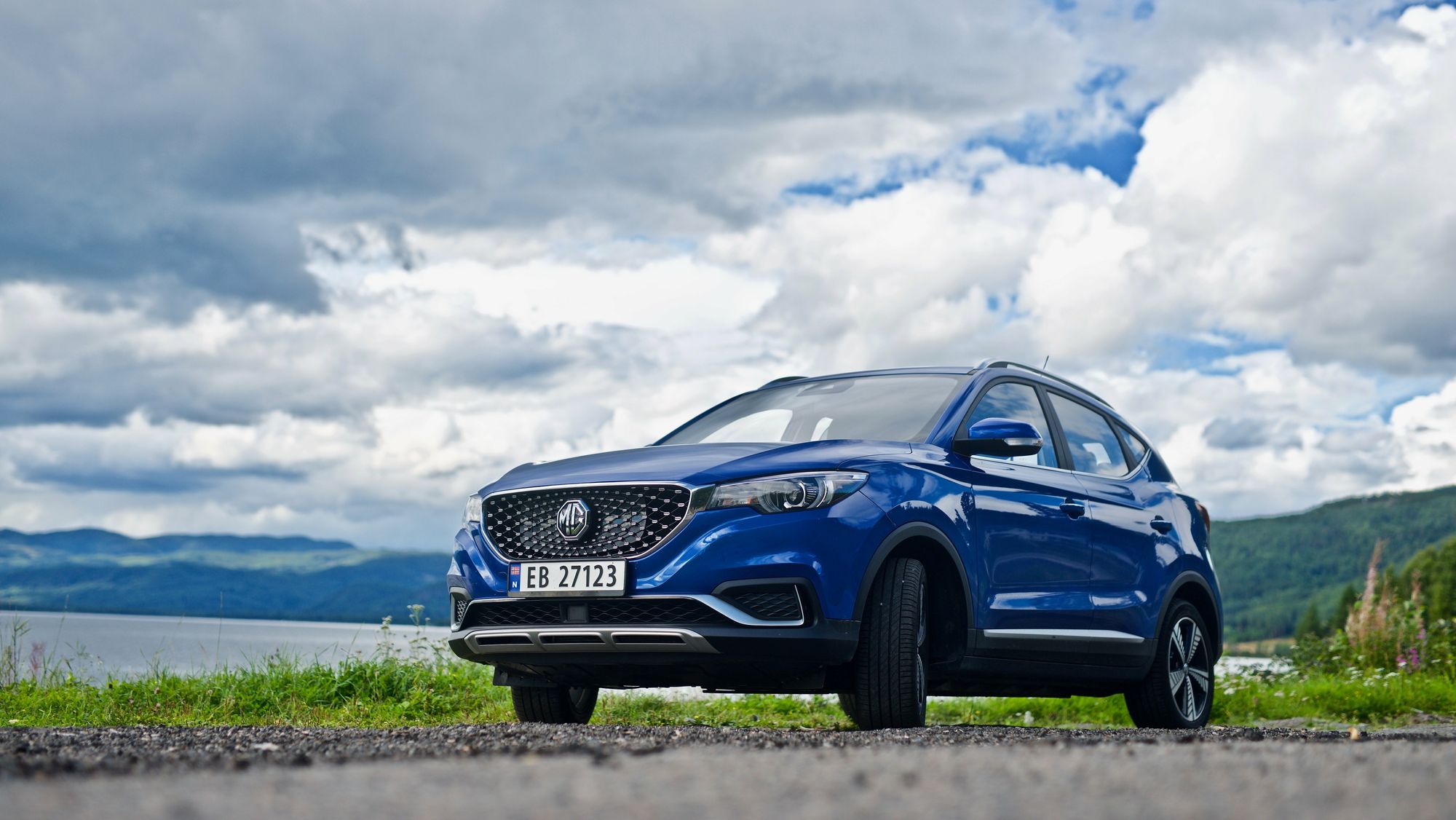
Kinesiske biler gjør det spesielt godt i Norge
Det er for så vidt uklart om Diess sammenligner epler og pærer, siden det er ukjent når Tesla regner at produksjonen av en bil starter og når den er avsluttet.
Tesla benytter store støpemaskiner som kan produsere store deler av bilene, og hevder at dette bidrar til at bilproduksjonen går i mye høyere tempo. Slike maskiner finner man ikke i Zwickau. I alle fall ikke enda.
Går over til store støpte deler
Når Volkswagen skal bygge neste generasjon elbiler i Wolfsburg fra 2026 skal også de ta i bruk såkalt «megacasting». De jobber allerede med å utvikle slike produksjonsmetoder ved sitt støperi i Kassel, til bruk i fremtidige modeller.
At det er produksjonsteknikker som er ment for kommende biler på nye plattformer betyr ikke nødvendigvis at det er umulig å integrere det i produksjonen i Zwickau. Vi får likevel ikke noe svar når vi spør direkte om dette er noe som ligger i kortene her.
Zwickau-fabrikken er det som i industrisjargongen heter et «brownfield»-anlegg. Motsetningen er «greenfield», hvor fabrikken bygges fra bunnen av og man ikke trenger å ta hensyn til eksisterende begrensninger.
Zwickau fungerer nå som en slags plantegning for resten av Volkswagens brownfield-anlegg som skal konverteres til elbilproduksjon.
En slik transformasjon er krevende, og det er ikke mulig å stanse opp, forklarer fabrikksjefen. De sluttet aldri å bygge biler underveis. Det har vært en krevende logistikkjobb. Produksjonsvolumene gikk ned i perioden, men det stoppet aldri opp.
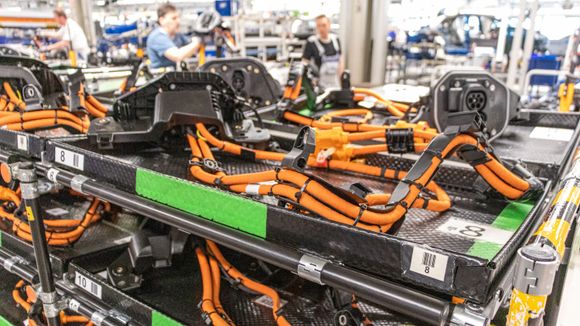
Delemangel fortsetter å stikke kjepper i hjulene
Men smertefritt har det likevel ikke vært. En stor utfordring har vært litt over tre ukers produksjonsstans på grunn av delemangel. Delene fra ukrainske underleverandører har skapt hodebry, men dette har gått bedre enn de trodde.
– Vi får ledningsnett fra Ukraina, og i begynnelsen hadde vi noen utfordringer, men de er løst og vi får nå deler fra Ukraina igjen, sier Loth.
Utfordringene står fremdeles i kø. Enten det er snakk om halvlederkomponenter eller situasjonen i Kina, hvor Shanghai har vært i fullstendig lockdown i en lengre periode.
Fabrikksjefen sier at de akkurat nå med sikkerhet vet at de har nok kabler fra Ukraina til å opprettholde produksjonen i tre til fire uker.
Det er en reell utfordring i mange industrier, og løsningen er å være forberedt på at flaskehalser kan dukke opp. For eksempel jobber de kontinuerlig med å ha alternative transportmuligheter klare dersom transport skal bli et problem. De er i tett kontakt med sine underleverandører for å komme leveranseproblemer i forkjøpet.
Dersom en leverandør helt uforutsett ikke kan levere deler, som i tilfellet Leoni i Ukraina, har de beredskapsplaner klare.
– Logistikken jobber 24 timer i døgnet for å holde fabrikken gående, forklarer Loth.
Raskere enn ventet
Selv om produksjonen ikke er helt på det nivået Volkswagen indikerte i 2018, med 1500 biler om dagen, har det gått bedre enn de trodde for noen år siden, sier fabrikksjefen.
Han er selvsagt full av godord om hvor fremragende bilene de lager er, men understreker at det bare blir bedre. De skal produsere biler med rekkevidde på over 700 kilometer. Om de ville kunne de i dag produsert en ID.4 som går fra null til hundre på 5,5 sekunder (ID.4 GTX bruker 6,2 sekunder). Loth er snar med å undetreke at dette ikke er noe som er på produksjonsplanen.
Det som imidlertid vil komme er produksjonsutgaven av ID.6, hittil presentert som konseptbilen ID. Vizzion, som skal hete ID.6, og ID.6 Shooting brake i stasjonsvognutgave. ID.6 er så langt bare lansert i Kina.
Målet er at 30 prosent av bilsalget skal være helelektrisk i EU i 2025, og 70 prosent i 2030. Deretter skal alle bilene Volkswagen selger være elbiler fra perioden 2033–2035.
Da må fabrikkene bygges om. Produksjon av ID.4 har allerede startet i deres fabrikk i Emden.
Må forstå prosessene
– Er du noen gang nede i produksjonshallen og deltar i produksjon selv?
– Ja. Særlig når vi starter ny produksjon. Noen ting kjenner du, noen ting må du lære, noen ganger må du observere hvordan andre opplever og gjør ting. Det er ikke bare meg, men hundrevis av andre kollegaer også. Det er sånn du forstår prosessene i detalj.
– Så kanskje du også kan bygge en bil?
– Ja, med litt hjelp, humrer Dr. Loth.
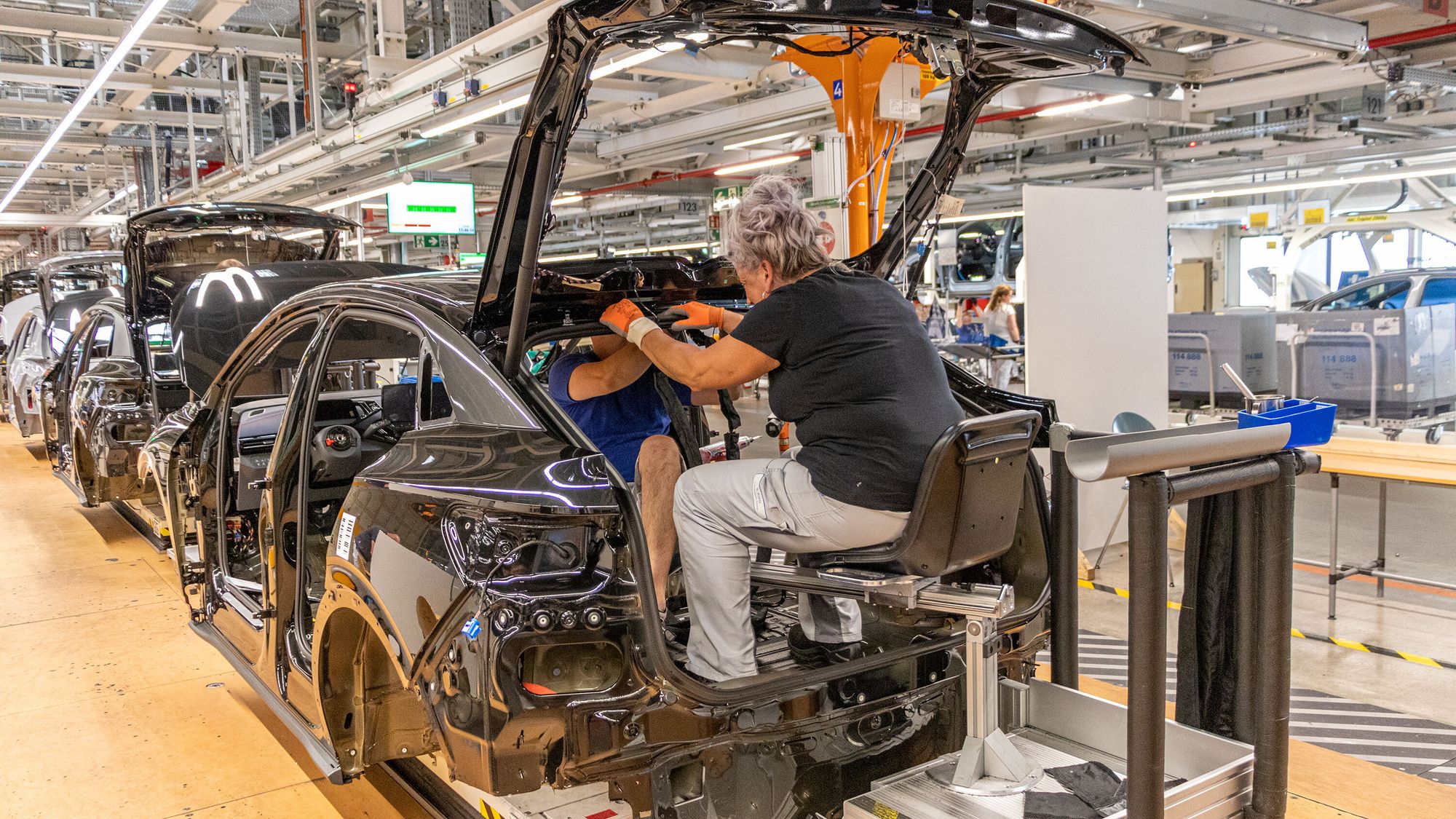
Norske bedrifter rammes av krisen i tysk bilindustri