Åndalsnes: Plasto er en bedrift som sprøytestøper plastdeler, kundene er hovedsakelig innen olje- og gass, fiskeoppdrett og marin sektor. For neste år regner administrerende direktør Lars Stenerud med at 30 prosent av omsetningen er hentet hjem fra Kina.
Forskningsbasert innovasjon
– Vi har utkonkurrert en kinesisk produsent. Vi vant på pris og ytelse for produkter til fiskeoppdrett. En fjerdedel av produksjonen vår er eksport til Asia, forteller Stenerud.

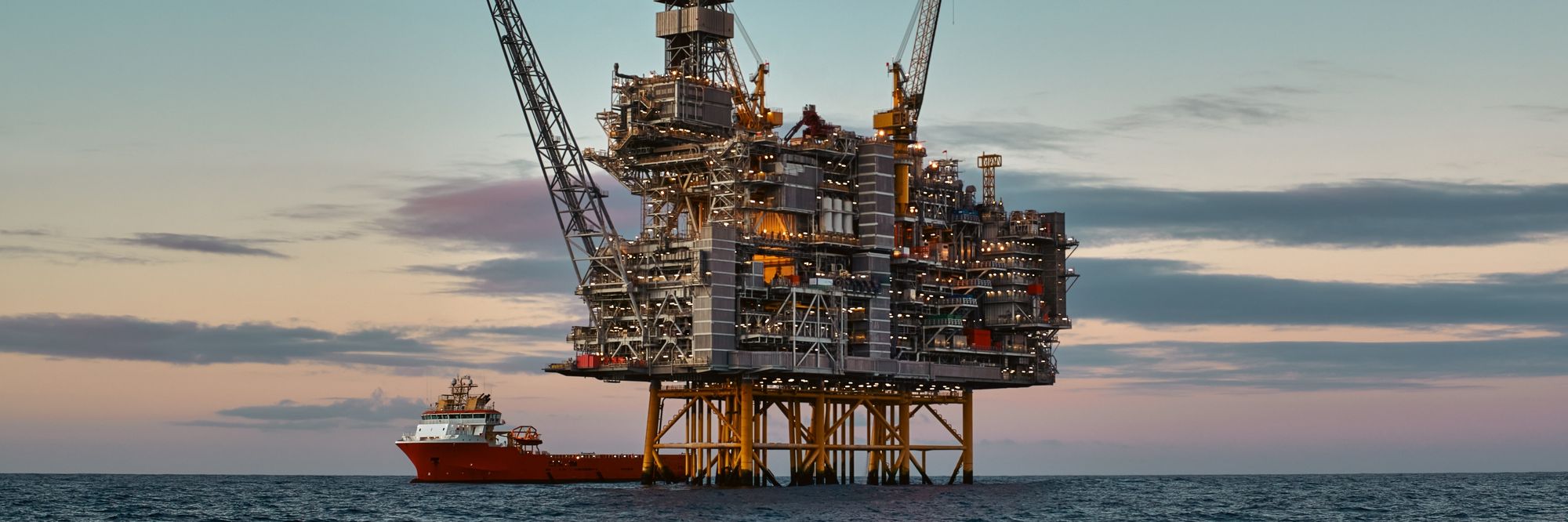
Stenerud mener det er to viktige faktorer bak suksessen. Det ene er å kunne levere produkter basert på kunnskap og forskningsbasert innovasjon, det andre er moderne og automatisert produksjon.
En statistikk fra Credit Suisse og Company Data viser at gjennomsnittet i verden er en robottetthet på 50 roboter per 10 000 ansatte. Norge er ikke med i oversikten, men Stenerud tror det her også ligger på maksimalt 50. Hos Plasto er robottettheten 13 000.
– Vi har tredoblet omsetningen i løpet av de siste årene med nesten samme bemanning. I 2009 omsatte vi for 36 millioner kroner, i 2013 var den på 77 millioner og i år passerer vi 100 millioner. Vi har bygget opp en egen automasjonsavdeling som kan bygge og integrere systemer.
70 prosent av omsetningen til Plasto er produkter som har vært i salg i mindre enn fem år.
– Å bare lage det du blir bedt om gir et smalt vindu. Vi kan, med vår kunnskap, skape merverdi både for kundene og for oss selv. Så må det kobles med råeffektiv produksjon.
Les om: Det er mye å hente – med automatisering
Må se behovet
Åndalsnesbedriften bruker 15 prosent av omsetningen på FOU, og har egen forskningssjef med kontor på Sintef Manufacturing. Ledelsen mener at for å utnytte mulighetene som ligger i kunnskapen trenger bedriften høy kompetanse innen automatisering og produksjonsteknikk. Få industribedrifter har så høy grad av automatisering som Plasto.
Satsingen har blant annet ført til at deler av produksjonen går 24/7. De deler av produksjonen som tikker og går gjennom hele helgen foregår helt uten noen til stede, kun vakthavende som må være forberedt på å rykke ut hjemmefra om noe skulle gå galt.
– Så lenge industrien ikke har sett behovet for høy automatisering er det kapasitet nok hos integratorene. Men i det øyeblikket vi erkjenner at vi skal ha industri i dette landet også i fremtiden, da mangler vi nok både kompetanse og kapasitet hvis vi ikke gjør noe med det. Men det fordrer at industrien faktisk ser behovet, sier Stenerud.
Les om: Automatisert merking til Nammo
Utdanning for fremtiden
Mange av de eldre ansatte startet uten utdannelse og har fått sin kompetanse via bedriften. Slik er det ikke lenger, nå kreves fagbrev eller teknisk fagskole innen automasjon for å bli ansatt.
– Det er en bransjenøytral utdannelse og jeg tror at i fremtiden vil det være svært attraktiv arbeidskraft.

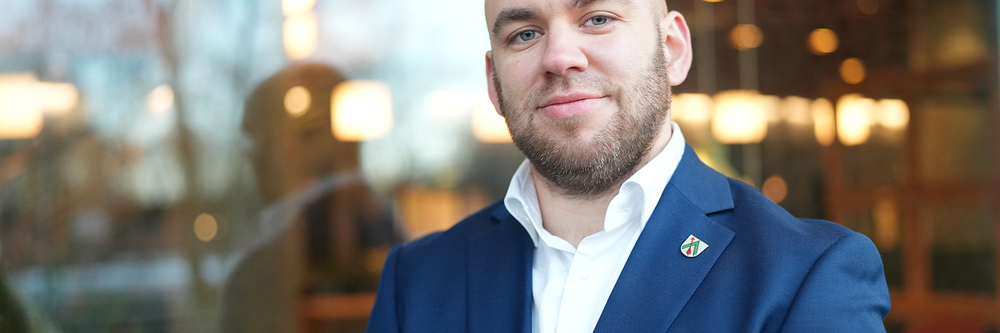
Ute i produksjonshallen viser fabrikksjef Knut Johan Stenerud frem hva Plasto har. Han starter ved en maskin som legger en to-komponent polyuretanpakning på en skjerm til lysarmatur for Glamox. Nå bruker han en mann til å produsere 250 000 stykker på et år. For tre år siden, før produksjonen ble så automatisert, brukte han fire mann til den samme jobben.
– Først støpes plasten, så legger vi på pakningene. Vi bruker tre roboter, og så har vi kjemibiten. Detaljene ønsker vi å holde for oss selv, sier fabrikksjef Stenerud.
På vei gjennom hallen passerer vi en liten 3D-printer. Plasto benytter den til å lage prototyper og små modeller. Det vil ikke gå mange år før slike brukes i produksjonen, tror han.
Så kommer vi til en stabel med ganske store sorte plastkomponenter, de veier over 40 kg hver. Det er elementer til en mære til et oppdrettsanlegg. Når det er ferdig montert får det en omkrets på 200 meter.
Les om:
Modifisert maskin
Delene kommer ut ferdig pallet og strappet, urørt av menneskehender. Tradisjonelt ville det vært en operatør bare til stablingen og pallingen. Produksjonen av disse delene starter med at råvarene trekkes inn med undertrykk fra to siloer, deretter går produksjonen sin gang og avsluttes med et par runder nedkjøling før palletering.
I løpet av vinteren skal de to robotene som håndterer delene etter at de er støpt erstattes med en ny og kraftigere robot som kan håndtere 250 kg. Det gjør det mulig å bedre utnytte kapasiteten de har bygget inn i støpemaskinen. I tillegg kommer det enda et kjøleanlegg som vil bidra til å øke produksjonen ytterligere.
– Jeg vil ikke ut med produksjonstiden, men jeg er ganske sikker på at vi bruker halve tiden som kineserne vi konkurrerte mot, og vi bruker ingen folk.
Lærebok om sprøytestøp
Støpemaskinen er laget av Wittmann Battenfeld i Østerrike. I original stand klarer den produkter opp til 12 kg.
I samarbeid med maskinleverandøren har Plasto modifisert den, og bygget en ekstra sylinder på toppen, for å lage plastkomponentene som er nesten fire ganger så store som maskinen opprinnelig hadde kapasitet til. Nå klarer den å produsere produkter opp til 120 kg.
Knut Johan Stenerud er stolt av hva han kan vise frem. Han har også hatt besøk fra den østerriske produsenten.
– De sa at de kom for å skrive neste kapittel i læreboken om sprøytestøping. Vi har satset veldig mye på å bygge egen kompetanse, det er viktig. Vi tar også det meste av vedlikeholdet selv.
I produksjonshallen, som ikke er veldig stor, kan Plasto ha produksjon av 20 forskjellige produkter samtidig.
På veggen kaster en projektor et bilde med en rekke tall og koder. Der blir det markert så fort noe ikke går som forutsatt i produksjonen.
– Den samme informasjonen går også til mobiltelefoner, og vi har en applikasjon som vibrerer når noe skjer. Det betyr at de ansatte kan gå med øreklokker, og høre på musikk. Det var ikke mulig tidligere, for da måtte de være oppmerksomme hvis det gikk en alarm.