Aker Solutions gruppe for flytere har kommet opp med en ny plattformløsning som de mener vil gjøre marginale felt lønnsomme. Løsningen trenger kun et personell på 20 mann.
Nå satser selskapet på at både norske og utenlandske aktører vil ta i bruk konseptet.
– Det har vært tradisjon på norsk sokkel å bruke mye skreddersøm, og mindre felt har ikke blitt prioritert. Vårt mål var å finne en løsning som kan gjøre disse mindre feltene lønnsomme. Det har vi klart nå, forteller Lars Laukeland, avdelingsleder for flyteprodukter og Per Kristian Bruun, avdelingsleder for teknologi i Aker Solutions.
I arbeidet med prosjektet, som startet tidlig i 2016, kombinerte de skroget fra en ubemannet plattform med et flatt, enkelt toppdekk med lette utstyrsmoduler.
Redusert vekt med 30 prosent
Konseptet har fått navnet Lean Semi, og er beregnet på små og mellomstore felt opp til 300 millioner fat.
– Dette er et forsøk på å adressere kostnadsnivået i industrien. Vårt mål var å kunne gjøre marginale felt lønnsomme ved å lage en billigere plattform. Det mener vi altså at vi har klart å få til, sier Bruun.
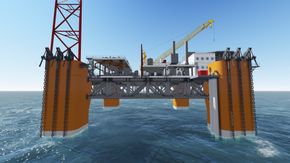
Han peker på at løsningen i seg selv ikke representerer ny teknologi, men at kombinasjonen er unik og svarer direkte på kostnadsutfordringene i industrien.
– Vi har benyttet allerede utprøvde byggeklosser. Ved å sette det sammen slik vi har gjort her, mener vi at vi har klart å få ned vekten på topsiden med om lag 30 prosent sammenlignet med en konvensjonell nordsjøplattform.

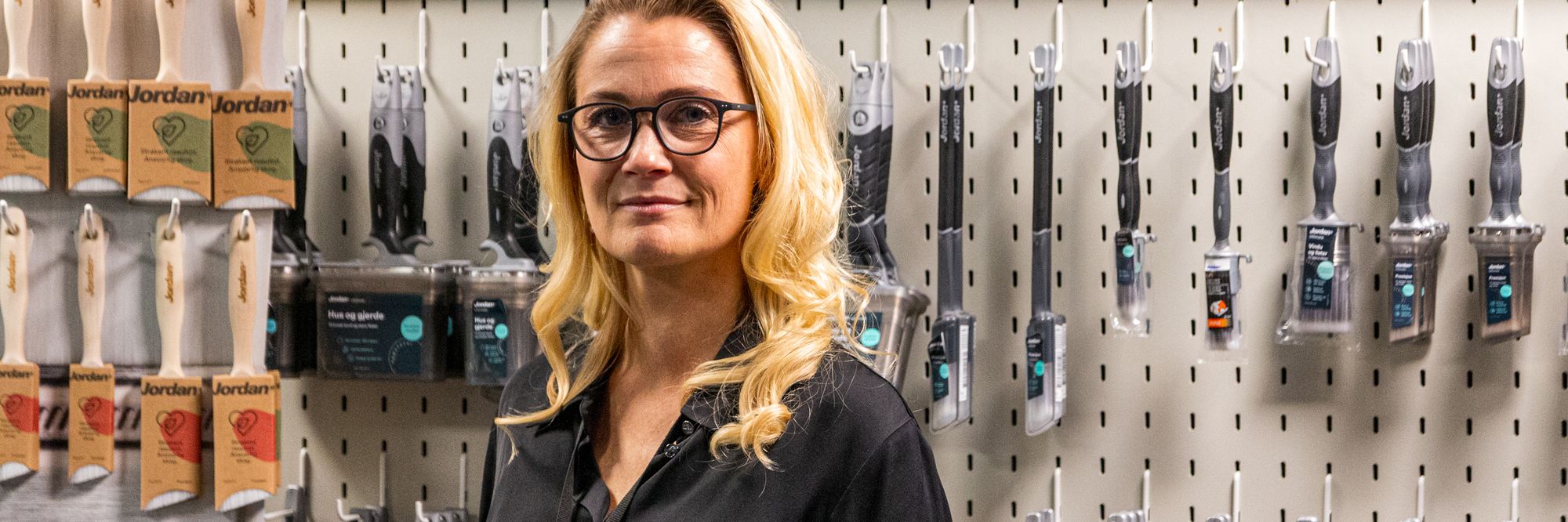
Aker Solutions ønsker foreløpig ikke å si noe konkret om hvor mye de ser for seg at konseptet kan spare i kroner og øre, men sier at det ser ut til å bli betydelig.
- Skulle installere brannpumper: Måtte ha 1000 sider dokumentasjon
6000 tonn, 60.000 fat olje
Utgangspunktet for prosjektet var å lage en rimeligere plattform, med en topside (plattformdekk) som skulle veie maks 6000 tonn. Plattformen skulle ha en levetid på om lag 10-15 år, og skulle kunne produsere 60.000 fat olje om dagen.
– Vi tok utgangspunktet i en antakelse om at det er mer kosteffektivt å bygge noe som er nøyaktig hva man trenger, og heller ta plattformen til kai for ombygging etter 10-15 år, om levetiden på feltet skal økes. Alternativet er å bygge ut med en masse fleksibilitet, noe som gjør det hele mye dyrere, ifølge Bruun.
Et annet utgangspunkt for utviklingen av Lean Semi, var at det skulle være et tenkt oljefelt, og at transporten av hydrokarbonene skulle gå gjennom allerede etablert infrastruktur.
– Men selve filosofien og Lean Semi-metoden vil selvsagt fungere overalt, sier han.
Bruun og Laukeland sier dog at det er én ting som kan ses på som et skjær i sjøen for Lean Semi: Hvis kundene ønsker å legge på en rekke selskapsspesifikke krav.

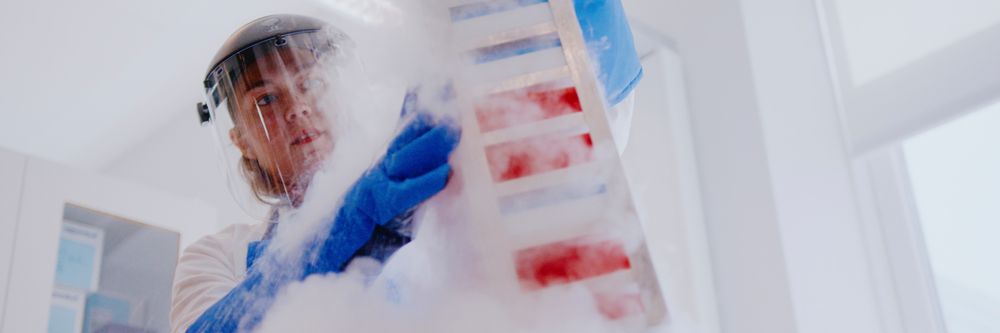
– Hvis kundene kommer med den vanlige shoppinglisten, vil det være kostnadsdrivende og ødelegge selve konsepttanken. Vi har sett på det man faktisk trenger, kontra det som er kjekt å ha. Kjekt-å-ha-lister kan vi ta inn, men da blir det en annen plattform, ifølge Laukeland.
- Her tester de en 13 år gammel ide: I en av Norges sterkeste tidevannsstrømmer
Minimalt utstyr i skroget
Skrog-løsningen Aker Solutions har benyttet hentet de fra et prosjekt de leverte for Chevron i Mexicogulfen, kalt Blind Faith. Det er et ubemannet skrog med lite utstyr, noe som gjør at behovet for personell blir betydelig mindre.
På Lean Semi har Aker Solutions tatt utgangspunkt i at personellet teller 20 mann.
– En normal semi (halvt nedsenkbar enhet, red.anm.) har mye utstyr nede i skroget og man har full tilgang til skroget i det daglige. Det går heis ned, og man kan gå dit for å inspisere pumper og ventiler.
– Det vi gjorde på Blind Faith som vi har videreført hit, er at vi ikke har noe særlig utstyr i skroget. Det eneste vi har er stål, rør for ballastsystemet, ventiler og ventilstyring. Det eneste behovet for å gå ned, er for å inspisere, sier Lars Laukeland.
Han forteller at man da har installert utstyr for ventilering slik at det blir frisk luft i skroget.
– Deretter åpner man en luke, så er det trygt å gå ned for inspeksjon og vedlikehold. Om du skal vedlikeholde en pumpe, er det en løsning for at du kan stå på toppen og trekke opp pumpene med en vinsj, omtrent som med en borestreng. Da kan man vedlikeholde pumpen uten å gå ned i skroget.
– Poenget er at med et konvensjonelt skrog har du en rekke systemer, kontinuerlig lufting, lys, og andre ting. Med denne løsningen blir utstyrsbehovet mye mindre, og det blir som å entre et lukket rom. Det blir en svært planlagt operasjon, med sikker utføring, sier Laukeland.
Senker tyngdepunktet
Flytergruppen valgte å kombinere Blind Faith-konseptet med en annen løsning som blant annet er kjent fra Njord-feltet i Norge: Et såkalt flat-top-dekk.
– Det er et flatt dekk på ett plan, støttet av en fagverksstruktur. Etter erfaringer på Njord vet vi at fagverksrammen tåler bølgeslag.
– Fordelen dette gir oss er at vi får senket dekket ned så mye som mulig. Da får vi ned tyngdepunktet på plattformen. Når dette blir mindre, blir også skroget mindre. Det er dette som har vært nøkkelen, sier Bruun.
Laukeland legger til:
– Fagverket utgjør styrken i dekket. Alternativet er å ha moduler som i seg selv bidrar til global styrke for å holde hele plattformen sammen. Da blir det mer stål i modulene og de blir mer komplekse.
– Med dette alternativet får du mer fleksibilitet. Du får lette moduler som er uavhengig av styrken til plattformen, sier han.
- Den har ikke produsert en dråpe olje: Nå krever en «armada av advokatfirmaer» milliarder etter Yme-skandalen
Flere interessenter
Ideen er videre at man setter topsideutstyr rett på det flate dekket i små moduler. Å ha ett plattformdekkdesign der utstyret blir plassert rett på det flate dekket gir ifølge Aker Solutions fleksibilitet i designprosessen, samt i prosessen med bygging og sammenstilling av topsiden.
– I stedet for de svære systemmodulene som er kjent fra Nordsjøen, gjerne på flere tusen tonn, så får vi flere tilbydere fordi vi separerer utstyret fra hverandre i små utstyrsmoduler. Dette vil kunne gi prosjektet konkurransefortrinn med tanke på innkjøp av modulene, ifølge Bruun.
Han sier at dette også mest sannsynlig reduserer sannsynligheten for forsinkelser i prosjektet.
– Alt utstyret er separat i små utstyrsmoduler. Det betyr at dersom du får forsinkelser på ett utstyr kan du likevel plassere det som faktisk er ferdig på topsiden, uten at du må vente på det som er forsinket, sier han.
Aker Solutions lanserte konseptet under årets ONS, og forteller at de har fått mange interessenter, både i inn- og utland. Men de ønsker ikke å si noe konkret om hvem det er og hvor det er snakk om.
– Men det er flere aktuelle prospekter i Norge der dette kan passe inn, sier Bruun.
- Fossilbilen er ferdig: – Kommer ikke til å bli produsert biler med forbrenningsmotor etter 2025