ÅRDAL: Dersom materialteknolog Kati Tschöpe virkelig brenner for en idé om å gjøre en elektrolysecelle noen milliampere mer effektiv, kan det fort koste Hydro fire–fem millioner kroner.
– Da sover jeg ikke godt før jeg ser at det fungerer, sier Tschöpe.

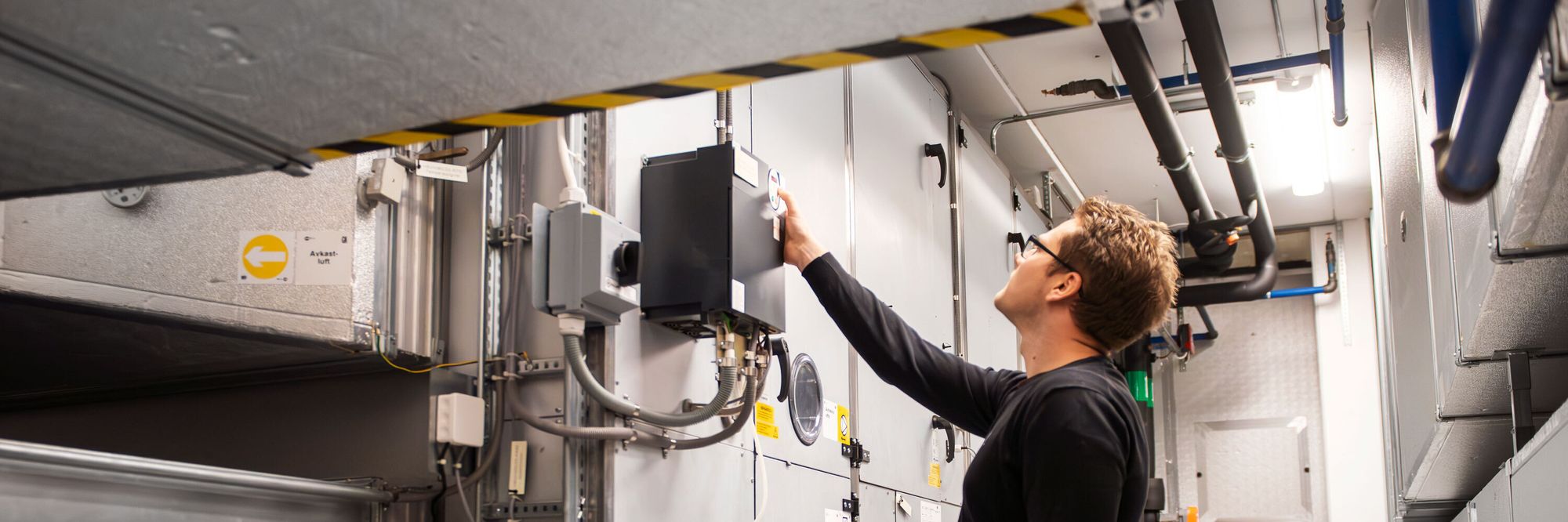
Før hun kommer så langt at en celle skal bygges om, må hun imidlertid klare å vise at ideen er forretningsmessig gunstig. Noen mikroskopiske energieffektiviseringsgevinster på en celle ved Referansesenteret i Årdal, kan bety store besparelser for resten av Hydro-systemet.
Les også: Daewoo skal bygge verdens største isbrytende tankskip
Brubygging
I Årdal er det bygget opp et tungt forskningsmiljø rundt primærmetallproduksjon.
– Det har alltid vært en sterk kultur for å forske og komme noen solide skritt framover, sier Johannes Aalbu, leder for teknologiutvikling i forretningsområdet Primærmetall i Hydro.
Han har ansvar for en forskerstab på rundt 50 som ikke bare jobber med neste teknologigenerasjon for aluminiumverk, men også to generasjoner framover. Fullskalaanlegget for forskningen og testing, Referansesenteret, ligger i Årdal. Alle forbedringer som kvalifiseres her, tas derfra ut til de andre anleggene i Hydro.
– Vi bygger bru mellom FoU og full produksjon. Her får vi testet ut teknologi, og vi kan lære opp operatører, sier han.
– En godt opplært operatør kan få en dårlig designet celle til å fungere bra, men verre er det at en dårlig opplært operatør kan ødelegge en godt designet elektrolysecelle i løpet av kort tid. Derfor er erfaring, opplæring og drift veldig viktig.
Det kan driftssjef av referansehallen, Håvard Gikling, bekrefte. Han har vært i alle avdelinger og kjenner produksjonen fra A til Å. Han sier fra om noe av det FoU-folkene ønsker seg er umulig eller mulig å få til med tanke på produksjonen.
Les også: Slik kan skip seile lydløst i Arktis
Tilsynelatende like
Ser man på de 12 cellene i Referansesenteret, er det for et utrent øye umulig å vite hvilke som skjuler prosessene og generasjonene fra hverandre. Bak dekslene finner vi både neste generasjon, HAL4e, og neste generasjon deretter, HAL 4e Ultra.
I HAL4e skal Hydro presse grensen for energiforbruk ned til 12,3 kilowattimer per kilo produsert aluminium (kWh/kilo), samtidig som produktiviteten ved cellen holdes på et veldig høyt nivå. I dag ligger verdensgjennomsnittet på 14 kilowattimer per kilo produsert, med en strømtetthet og dermed produktivitet, som er mye lavere enn den som Hydro jobber med å realisere.
CO2-utslippene skal samtidig ned til omtrent 1,5 tonn per tonn aluminium. Allerede før teknologien er implementert i ordinær drift, jobber forskerne med neste versjon av teknologien, HAL4e Ultra. Der er målet å komme ned mot 11,5 kWh/kilo og 1,5 tonn CO2.
Les også: Så godt presterer Norge innen forskning
.png)
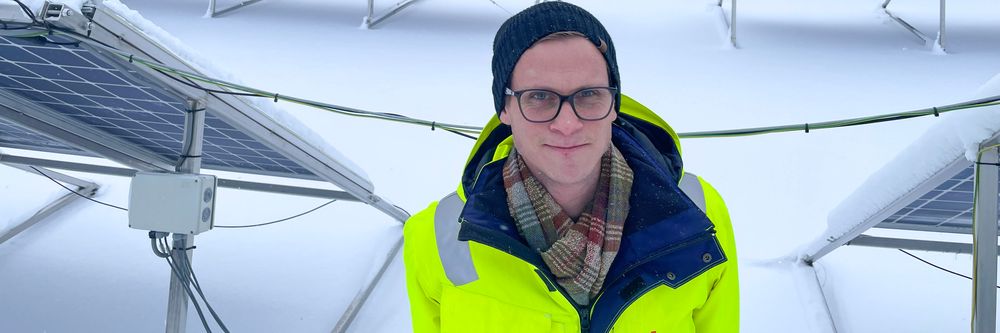
Mål: 10 kWh
– Vi har satt oss enda mer hårete mål. På sikt skal vi ned i 10 kilowattimer per kilo aluminium, sier Hans Erik Vatne til Teknisk Ukeblad.
Han er ansvarlig for teknologiutvikling i hele konsernet. Det er omtrent 250 ansatte som forsker og utvikler i Hydro på heltid. Budsjettet er på cirka 350 millioner kroner.
Vatne har ikke satt opp det hårete målet for å imponere konsernsjef Svein Richard Brandtzæg.
– Det var han som formulerte målet, sier Vatne og smiler.
– De gliser og ler, rister på hodet og tror ikke det er mulig. Men for bare få år siden trodde heller ikke vi at det var mulig å komme ned til 11,5 kWh/kg. Det ser vi nå er innen rekkevidde, så her er det viktig med hårete mål, sier Vatne.
Brandtzæg har doktorgrad i materialteknologi og kan aluminiumframstilling ned på detaljnivå. Han er i stand til å stille detaljerte spørsmål det kun er få som kan svare på.
En av dem som kan svare er Kati Tschöpe. Også hun har en doktorgrad i materialteknologi fra Trondheim, har jobbet på NTNU som post doc og vært i Sintef. Ikke nok med det: Hun har sittet på samme kontor på Gløshaugen som Brandtzæg hadde da han tok sin doktorgrad.
Ikke rart mange fleiper med henne om at hun står for tur til å overta som konsernsjef en dag. Tschöpe smiler forlegent. Det inngår ikke i hennes planer. Hun er opptatt av å løse de mange utfordringene som står for tur dersom målene til Brandtzæg skal nås.
Les også: Her bråbremser en F-35 - endelig
Ovnsdissekering
En av oppgavene hennes beskriver hun som patologi. Når en testcelle som måler cirka 4 x 16 meter rives, går materialdoktoren ned på knærne og jobber som en blanding av arkeolog og patolog som skjærer og lager snitt for å se hva som har skjedd med de ulike elementene en elektorlyseovn er bygget opp av.
Det er både kjemiske og termiske reaksjoner som skal kontrolleres. Gjøres det en endring, kan det få andre konsekvenser enn først forutsatt.
– En elektrolyseovn er utrolig komplisert, og det som skjer i og rundt ovnen krever kompetanse på alle mulige fagfelt, sier hun entusiastisk.
Derfor har Hydro trukket til seg doktorander, sivilingeniører, kjemikere, fysikere og kybernetikere og flere andre fagfelt fra 13 ulike land til sine forskningsaktiviteter i Årdal. I tillegg har selskapet utstrakt samarbeid med både NTNU, Sintef og Ife (Institutt for energiteknikk) i Norge og lokale universiteter i alle land selskapet har produksjon.
Blant områdene det fokuseres på, er økt bruk av simulering for å slippe å rive og bygge opp ovner til fem millioner kroner for ofte. Ideell levetid for en celle er seks til sju år.
Les også: Er dette den stiligste flygende bilen som er laget?
ESA-behandling
Neste generasjon elektrolyseteknologi, HAL 4e, skal etter planen benyttes i et pilotanlegg med 60 celler på Karmøy, en investering på 3,6 milliarder kroner som tidligst kan begynne produksjon i 2017. Hydro har søkt og fått støtte på 1,5 milliarder kroner fra Enova. Søknadene er nå til behandling hos Eftas overvåkingsorgan Esa.
Fortsatt er det et stykke fram til teknologien er klar for implementering i fullskala.
– Men når det skjer, vil aluminiumframstillingen kreve brøkdeler så mye energi som for bare få tiår siden, sier Vatne.
Les også:
Slik kan 3D-printing endre industrien for alltid