Tau har vært brukt som forankring på dypvannsprosjekter i Mexico-golfen og andre steder i snart 20 år, men ikke på norsk sokkel fordi de fleste prosjektene her er på grunnere vann hvor kjetting er det mest holdbare.
– Hovedgrunnen til at man bruker fibertau laget av polymermaterialer på dype vann er vektbesparelse på forankringssystemet. Et polyestertau er nærmest vektløst i vann og krever derfor mindre dimensjoner på krav og vinsjer på plattformen. Det er også lettere å håndtere. På den måten sparer man kostnader og man kan forankre på dypt vann hvor løsninger med kjetting ville blitt for tunge, sier Mads Arild Eidem som leder seksjonen for Materials & Subsea Operations ved DNV GL i Bergen.
Selskapet har flyttet sin oppgraderte snart 40 år gamle legendariske strekkmaskin med en kapasitet på 2900 tonn til nyere og større lokaler.

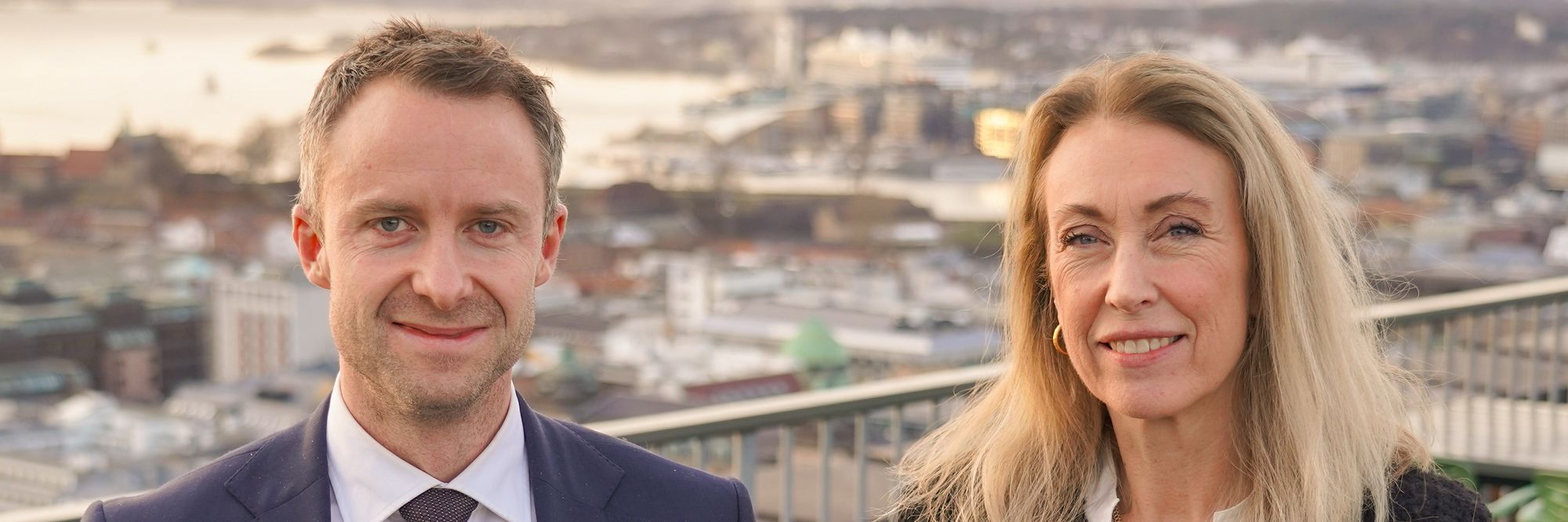
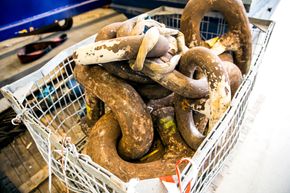
I forbindelse med Underwater Technology Conference i Bergen arrangerte DNV GL en demonstrasjonstest for operatører og utstyrsleverandører. Testen gjaldt et polyestertau tilsvarende det som nå er installert på Aasta Hansteen.
- Les også: Slik ser de for seg at grunne dybder på norsk sokkel skal passe for flytende havvind (TU Ekstra)
Holdt i sju minutter
Etter sju minutter - da strekkstyrken kom opp til 1909 tonn, røk polyestertauet med to harde smell.
Oppnådd bruddstyrke var dermed over det som tauet skulle tåle ifølge krav fra leverandør.
Myndighetene krever at operatørene kan dokumentere at tauet som skal brukes på norsk sokkel, er kvalifisert til den bruk de er planlagt for.
Aasta Hansteen installeres nå ferdig på ca. 1275 meters dyp. Den flytende Spar-plattformen er bundet og stabilisert med en total taulengde på nær 4,1 mil.
Ifølge kommunikasjonssjef for forskning og utvikling i Equinor, Eskil Eriksen, har Aasta Hansteen 17 forankringsliner der hver line er på ca. 2500 meter. Disse består av 2400 meter fibertau og drøyt 100 meter kjetting oppe og nede. Fibertauet har en diameter på 26 cm og en bruddstyrke på 1900 tonn.
- Equinor forskjellsbehandler direktører som slutter: Kjetel Digre må vente i ett år før han får gå til Aker BP
Like lang levetid
Og selv om fibertauet er dyrere å produsere enn kjetting av stål, er det mer fleksibelt og minst like holdbart på store dyp. Det vil si at de har en levetid på 20-25 år.
Selvet tauet er satt sammen med et vell av fibre som er flettet sammen på en
Vi har en spisskompetanse som gjør at vi kan lage standarder for bransjen
Gustav Heiberg, leder forretningsutvikling, materialer i DNV GL
spesiell måte som kan variere fra produsent til produsent. Tauet som ble testet i Bergen kom fra en av de største leverandørene, Lankhorst Euronete Portugal. Det er omsluttet av en tjukk plastkappe ytterst, bygget opp av et stort antall av flettede deltau som ligger parallelt – med en kappe som bundler dette sammen.
– Hensikten med kappen er at den skal holde deltauene sammen. Selve tauet legges ofte ned på havbunnen inntil det er klart for installasjon avhengig av værvinduet. Tauene synker fordi det er litt negativ vekt i forhold til vann, men det krever mye mindre ressurser å installere enn kjetting på grunn av vekten. Under kappen har vi et sandfilter som skal hindre gjennomtrenging av sand og partikler, samt et UV-filter for at polyesteren ikke skal bli nedbrutt av sol under installasjon. Hele tauet gjennomtrenges av vann og koples alltid til en bunn- og toppkjetting, sier overingeniør Knut Eide ved DNV GLs teknologisenter for Offshore Mooring & Liftning i Bergen.

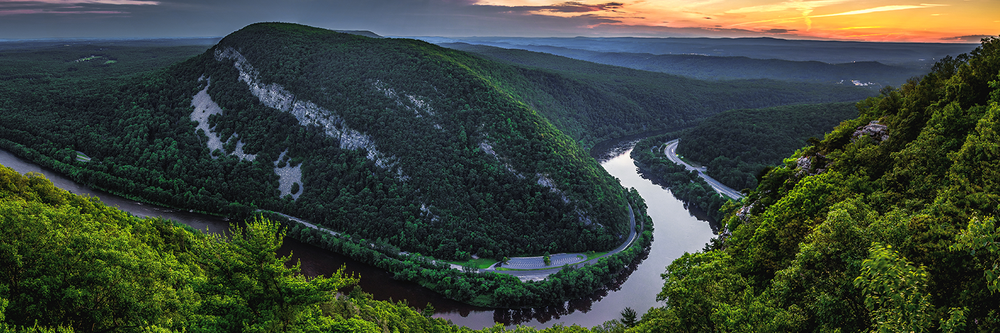
Disse tauene produseres i lengder på ca. 1000 meter og kobles sammen om de skal være lengre.
Ifølge Eidem er det mye penger å spare på bruk av fibertau sammenliknet med kjetting. Spesielt gjelder dette på store havdyp der også ordinær kranwire i stål kan erstattes helt eller delvis med fibertau.
Hemmelige tester
Kvalifikasjonstesting er vanligvis svært hemmelige seanser. Ingen selskaper vil gi innsyn i eventuelle materialsvakheter – verken før de tas i bruk eller i forbindelse med vedlikehold.
– Vi driver mest med oppdragstesting for selskaper. Vi merket godt at oppdragene ble færre etter oljeprisfallet, men nå er dette i ferd med å ta seg opp igjen. Og den andre trenden er at vi får mange flere kunder fra andre bransjer, sier Gustav Heiberg som er ansvarlig for forretningsutvikling på testing av materialer i DNV GL.
Ved siden av fibertau går det mest i testing av kjettinger og ståltau til rigger, plattformer og skip, men også til fiskeoppdrett og havbruk, landbasert og flytende vindkraft, bruer og jernbane.
Selskapet har testlaboratorier både ved hovedkontoret på Høvik og i Bergen, men det er bare maskinen i Bergen som kan ta styrker opp til 2900 tonn. Det finnes kun et laboratorium i USA som kan matche den styrken.
– Bruddtesting har en kort varighet på en time eller to, mens utmattingstesting av komponenter kan pågå over flere uker. Vår erfaring er at de operatørene som kvalifiserer materialer i tidlig fase, klarer å optimalisere seg på utstyr. Vi har for eksempel fått tilbakemelding om at Shell sparte 100 millioner kroner på å optimalisere forankringssystemet ved bruk av polyestertau, sier Eidem.
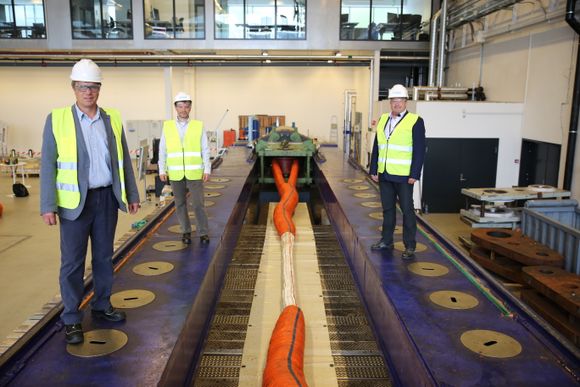
Unik kompetanse
Heiberg mener den ca. 40 år gamle strekkmaskinen i Bergen og de testansvarlige representerer en unik kompetanse. Nylig flyttet DNV GL til nye og større lokaler i Bergen.
– Innen fibertau jobber vi både med strekkbelastning, materialanalyse og verifikasjon av designanalyser. Vi har en spisskompetanse som gjør at vi kan lage standarder for bransjen, sier Heiberg.
DNV GL driver også med skadeanalyse ved sine 14 laboratorier i verden. Det vil si at de tester f.eks. hvordan et fibertau tåler påkjenningene fra et ståltau om en tråler skulle komme for nær en installasjon som er forankret med tau.
Av mer enn 1000 skadeundersøkelser som DNV GL har gjort på installasjoner fant man at 79 skyldtes forankringsfeil med tau eller kjetting.
Foreløpig er det lite utbredt, men Heiberg tror også fibertau kan utstyres med sensorer for å predikere vedlikeholdsbehov.
Apropos styrke: Nylig fikk DNV GL et oppdrag fra Equinor om å teste de enorme 152 mm tykke kjettingene som forankrer Troll B-plattformen etter 20 års bruk som var estimert levetid.
– De var fortsatt like sterke og kunne holdt i mange år til. Helt fantastisk, sier overingeniør Knut Eide entusiastisk.
.png)