Av Eiliv Elvebakk, Goodtech Products
Gode løsninger eksisterer og besparelsene kan ofte være store, så hvorfor ikke starte i dag?
Overall Equipment Efficiency (OEE) ble i sin tid definert av bilprodusenten Toyota for å kunne analysere og målsette hvor effektiv produksjonen er. I dag er OEE en anerkjent standard og mange bedrifter (også norske) må rapportere OEE-faktor til f. eks konsernets ledelse. Denne artikkelen har som mål å gi en liten innføring i OEE-begrepet, samt belyse praktisk bruk og implementasjon.
Litt teori
OEE-modellen beregner en ytelsesparameter for hvert aktivitetsområde (produksjonscelle, linje, maskin eller område) som overvåkes. På den måten kan man enkelt avgjøre om et aktivitetsområde har ønsket ytelse både i nåtid og historisk. Det er også mulig å sammenligne maskiner og områder med hverandre.

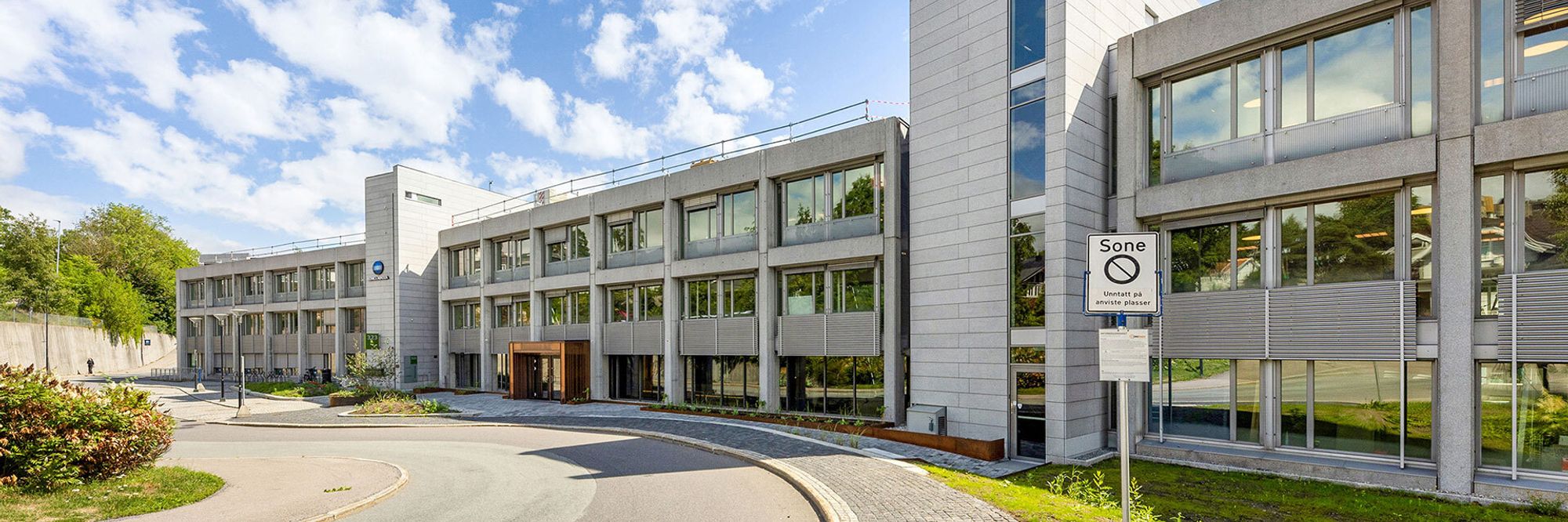
OEE-faktoren består av tre komponenter som måles i prosent: Tilgjengelighet, ytelse og kvalitet. OEE-faktoren er produktet av de tre faktorene, og måles dermed også i prosent. Se egen rute for kalkulasjoner. I tillegg til å beregne selve OEE-faktoren, får man gjerne også tak i andre vesentlige parametre som nedetid, stoppårsaker og hendelser.
Ikke uventet er det nettopp Toyota som ligger på verdenstoppen når det gjelder OEE, med en OEE-faktor på 90%. Gjennomsnittet i Europa var tidlig på 2000-tallet 42%, noe som i seg selv gir grunn til ettertanke.
Alle bransjer
Det er viktig å poengtere at OEE-modellen kan benyttes innenfor alle typer industri, ikke bare stykkproduksjon, som kanskje er det mest nærliggende. OEE-beregning kan med fordel benyttes innenfor både batch- og prosessindustri. Modellen bryr seg ikke om hva aktivitetsområdet produserer, det spiller ingen rolle om det er samlebåndsproduksjon av bildeler eller om det er et prosessanlegg som leverer olje.
.png)
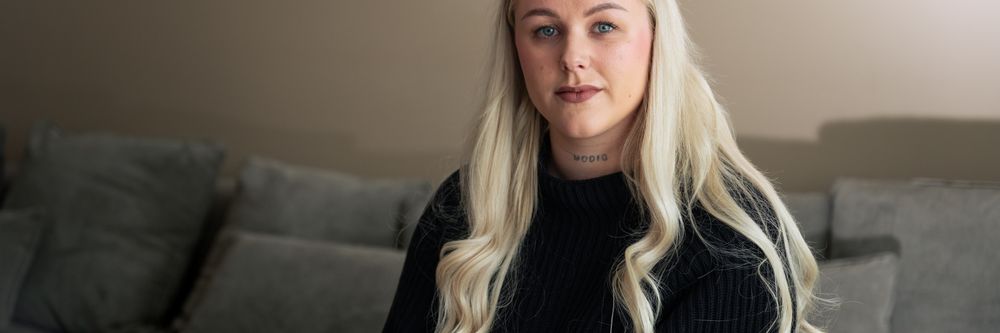
La oss ta et lite eksempel for å illustrere hvordan OEE-faktoren og tilhørende data som nedetid, hendelser og stansårsaker kan benyttes.
Skumme kremen av fløten
På grunn av stor etterspørsel må bedriften NorMelk AS øke produksjonskapasiteten med 10% for et av sine produkter (fløte). For noen år siden ville sannsynligvis tilbakemeldingen fra operatører og produksjonssjef vært at fløtemaskinen allerede produserer maks, og at den eneste løsningen er å sette inn en ny maskin eller et ekstra skift.
Nå er imidlertid situasjonen en annen, NorMelk AS har OEE-beregning på hele maskinparken. OEE-faktoren for fløtemaskinen er på 55% og ledelsen vil først og fremst undersøke mulighetene for å forbedre maskinens OEE. Operatørene og produksjonssjefen setter igang med å analysere nedetid og stoppårsaker og det viser seg at mye av nedetiden, dvs. tap av produksjonstid, skjer med innmatingen til maskinen.
Oppdaget skadet sensor
For å rette på dette blir man enige om å endre operatørens arbeidsmetode (som for øvrig har vært uforandret i 20 år,) samt at automatikken på inntaket modifiseres. De nye tiltakene iverksettes og resultatet lar ikke vente på seg: OEE faktoren stiger til 62%. Ved gjennomgangen av stoppårsaker og hendelser, fant man også at en sensor ofte slår ut, noe som reduserer maskinens hastighet.
Vedlikeholdsavdelingen tilkalles og fastslår raskt at sensoren er defekt. Etter at ny sensor er montert, kan man se at OEE-faktoren forbedres ytterligere. Resultatet er at den eksisterende maskinen kan ta unna den økte produksjonen uten at det brukes millioner av kroner til ny maskin eller økte lønnskostnader.
Små grep, store løft
Eksempelet kan kanskje virke enkelt og banalt, men slik er jo også virkeligheten i mange tilfeller. Ofte er det bare små endringer som skal til for at man utnytter maskinparken på en bedre måte. Endringene trenger ikke bare å være av teknisk art, det kan like gjerne være endringer i arbeidsrutiner eller operasjoner.
Hensikten med eksempelet er å synliggjøre hvilke muligheter OEE og data for nedetid og stoppårsaker gir. Informasjonen blir rene beslutningsdata, som kan brukes på alle nivåer i bedriften. For enhver beslutningstaker må det jo være betryggende at beslutninger baseres på fakta, og at man i etterkant kan evaluere og dokumentere virkningen av de tiltakene som iverksettes.
Sanntidsdata for OEE
Teori er en sak, men hvordan finne OEE, nedetid og stoppårsaker i praksis?
Noen bedrifter beregner OEE-faktor basert på data i bedriftens overordnede forretningssystem (ERP-system). Dette vil i de fleste tilfeller ikke være særlig nøyaktig, dataene blir statiske og man går glipp av stoppårsaker og hendelser.
Den eneste farbare veien er å ta tak i sanntidsdata fra aktivitetsområdet (automatiseringssystemet) og bygge opp statistikk på bakgrunn av disse. I dag er det ingen grunn til å skreddersy eller egenutvikle slike systemer, det finnes standard løsninger på markedet som konfigureres til å passe det enkelte aktivitetsområde.
Standardløsningene finnes i ulike utførelser, alt fra en hardware modul som kobles direkte til maskinen, til rene software løsninger som henter data fra aktivitetsområdet via OPC (Ole for Process Control). Hardware løsningene er typisk mer lukket, mens software løsningene typisk lagrer data i en åpen database, og er mer fleksible når det gjelder rapportering (f.eks via HTML-rapporter over bedriftens Intranett). GE, Rockwell og Wonderware (Invensys) har for eksempel slike løsninger.
OPC ”universalnøkkel” til PLSer
Man må også løse en rekke praktiske utfordringer før OEE-faktor kan beregnes. Automatiseringssystemene kan være gamle og ofte bestå av ulike fabrikater. Det må gjerne gjøres programendringer i PLS-en, og det er ikke sikkert at alle nødvendige signaler er tilgjengelig. I mange tilfeller er det ikke alt som kan automatiseres, og man er avhengig av manuelle operasjoner, f.eks for å registrere vrak eller for å identifisere stoppårsaker. Hvis dette høres kjent ut, så fortvil ikke.
OPC-standarden løser elegant problemet med forskjellige PLS- fabrikater. Hvis det ikke er mulig/ønskelig å gjøre endringer i eksisterende system for å få tak i nødvendige data, kan en løsning være å installere en liten PLS, som kobles til eksisterende (og eventuelt nye) sensorer. En del av standardløsningene støtter også innlegging av manuelle data, dvs. at OEE kan beregnes selv om f.eks vrak må registreres manuelt.
Menneskelig motivasjon
Kanskje viktigere enn de tekniske utfordringene, er de organisatoriske utfordringene, som kommer i kjølvannet av optimaliserings- og effektiviseringsprosesser. Det er svært viktig å inkludere alle som berøres når OEE og logging av nedetid og stoppårsaker skal implementeres. Å få alle til å forstå hensikten med systemet samtidig som dataene brukes som motivasjonsfaktorer, kan være helt avgjørende for om OEE-investeringen blir en suksess.