Bruk og installasjon av bolte forbindelser
Bolter produseres i dag til 85 ulike industristandarder. Kravene til bolteforbindelser varierer for ulike bransjer utfra gitte krav til design, drift og vedlikehold. Dette innebærer spesifikasjoner av materialegenskaper, korrosjonsmotstand, utforming og varmebehandling. Ved installasjon er det i tillegg viktig å oppnå riktig forspenning av bolter, noe som krever bruk av egnet verktøy og prosedyrer. En stabil bolteforbindelse krever således vurdering av følgende forhold:
- Dimensjonering av belastning

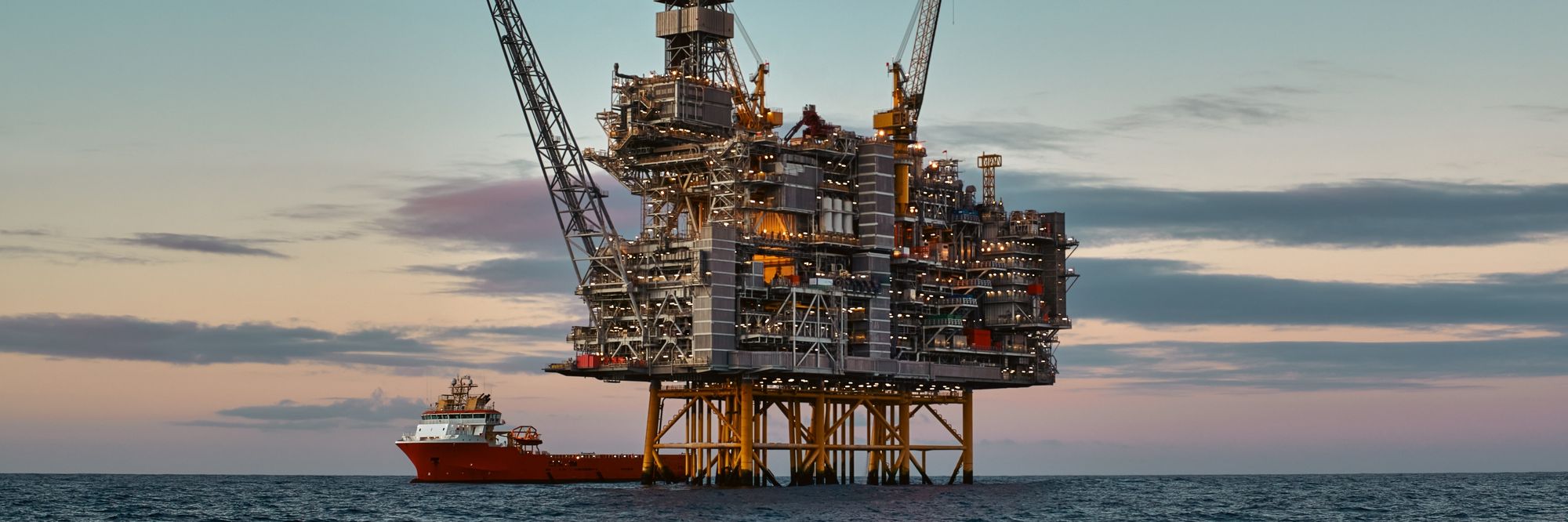
- Materialvalg med hensyn på mekaniske egenskaper og korrosjonsmotstand
- Eventuell bruk av smøremiddel
- Forspenning og bruk av verktøy for tiltrekning
Dette er forhold som er beskrevet gjennom en rekke standarder og etablerte prosedyrer. Likevel viser skadeanalyser utført av DNV at grunnleggende feil stadig gjentas. Det faktum at alle har et forhold til bolteforbindelser er kanskje en grunn til at det ikke alltid settes av nødvendig tid til gjennomgang av design og installasjon på formålstjenlig og forskriftsmessig måte?
Offshore : Skader og lekkasjer på utstyr med hydrokarboner
De områder der bruk av bolter offshore er særlig kritisk er i hovedsak: Flenseforbindelser : Rørledninger, stigerør og subsea utstyr
Løfteutstyr : Kraner og boretårn
Lekkasjer på utstyr som fører hydrokarboner kan få katastrofale konsekvenser på en offshore plattform. En undersøkelse av HSE (Health and Safety Executive) fra 1996, dokumenterte 888 hydrokarbon lekkasjer over en periode på 3,5 år (Storbritannia). Utslipp var fordelt på ulikt prosess utstyr som følger : 44 % på piping, 36 % på ventiler og 20 % på flenser.
Bruk på flenseforbindelser utgjør et betydelig del av bruksområdet for bolte forbindelser offshore. Således innebærer riktig bruk av flenseforbindelser, med de krav dette setter til de ulike deler av verdikjeden, et viktig risikoelement i vurdering av lekkasjer og potensielle ulykker.
Installasjon og tiltrekking av bolter
Feil ved tiltrekking representerer en av hovedårsakene til at de skader som skjer ved bolte forbindelser. Verktøy for tiltrekking baserer seg enten på bruk av hydraulisk strekkbelastning eller på metoder basert på momenttiltrekking. Dette er metoder som gir en indirekte avlesning av forspenningen i bolten.
Forspenning
ved strekkbelastning strekkes bolten til en ønsket last deretter trekkes mutteren til med håndkraft og strekkbelastningen avlastes. I utgangspunktet er dette en metode som skulle gi god mulighet til å oppnå ønsket forspenning. Forspenning med momentverktøy krever gode prosedyrer og at de følges.
Ulike typer overflatebehandling og smøremidler blir brukt for å oppnå ønskede friksjonsbetingelser. I praksis kan inhomogeniteter på boltens gjengeparti, eksempelvis av galvanisering gi store utslag i friksjonen ved tiltrekning. En konsekvens kan være at det er store individuelle forskjeller i friksjon fra bolt til bolt av samme bolteleveranse. I det tiltrekkingsverktøyet kun gir et indirekte mål for den reelle forspenningen er det viktig at det brukes gode prosedyrer for installasjon av bolte forbindelser.
Kontroll og oppfølging av forspenning er i dag blitt enklere ettersom det er tilgjengelig utstyr overvåking av forspenning på bolter(”Boltsafe”). Denne teknologien gir mulighet for direkte avlesning av forspenningen av bolten både under installasjon og etter en tids drift.
Boltematerialer : Kvalitetskontroll
.png)
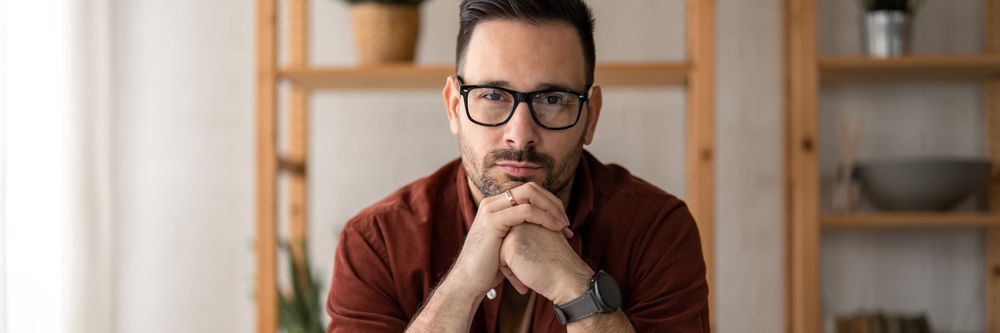
Riktig materialvalg er også en grunnleggende forutsetning for å oppnå en stabil bolteforbindelse. Dette kan bare oppnås ved at det etableres et system for kvalitetskontroll. Systemet må innebære sporbarhet av bolter med hensyn til nødvendige sertifikater, samt at alle bolter bør ha godkjent produsent- og gradmerke på bolte hodet. Det kan nevnes at det i USA for ca 15 år siden ble avdekket et stort marked med svindel av bolter. Ved en gjennomgang av forsyningsbasene til USAs forsvar ble det i denne perioden funnet 30 millioner substandard bolter. Det har imidlertid ikke vært store problemer med substandard bolter i Norge.
Typiske skader på bolter
Skader på bolter og bolte forbindelser kan ha ulike årsaker. Generelt er det antatt at ca. 85% av alle skader på bolte forbindelser skyldes utmatting. Utmatting kan være en følge av flere forhold:
- Dynamisk belastning ved utilstrekkelig forspenning eller uheldig utforming av forbindelsen
- Overbelastning av bolten som resulterer i redusert forspenning.
I tabell 1 (se link nederst) er det listet opp noen typiske skader, samt noen tiltak for å unngå slike skader. Det er viktig å være klar over at en skade i virkeligheten ofte er et resultat av flere faktorer som virker sammen. Dette omfatter både utforming av bolteforbindelsen, valg av boltemateriale, utforming av gjenger, utilstrekkelig smøring av gjenger samt feil under installasjon.
Undersøkelser utført av NASA, USA, har vist at 50 % av alle skader på bolte forbindelser skyldes utilstrekkelig kvalitet på arbeid i forbindelse med design/installasjon.
Bruk av bolter offshore
Bolter anvendes offshore både i atmosfærisk sone, skvalpesone og neddykket i sjøen. Her er bruken av bolteforbindelser særlig kritisk på flenser i produksjons- og prosessrør. I de fleste tilfeller er bruken av bolter i offshore industrien basert på ASTM A-193, og delvis også ASTM A-320, og muttere etter A-194. Bruk av bolter i de ulike miljøsoner har sine utfordringer:
Atmosfærisk sone:
Her er det ofte høy temperatur, mens miljøbelastning fra atmosfæren er begrenset. I tillegg er det mulig å utføre inspeksjon og å foreta vedlikehold.
Skvalpesone:
Miljøbelastningen er stor. Materialet må være korrosjonsresistent. Her vil det være områder der katodisk beskyttelse delvis kan ha effekt. Dette innebærer at materialet må være immunt mot hydrogensprøhet. I denne sonen er det begrenset mulighet for inspeksjon.
Neddykket: For permanent neddykket utstyr er det nødvendig at materialet er immunt mot hydrogensprøhet. For en rekke høyfaste boltematerialer er dette ikke avklart.
Det har vært utført en rekke arbeider knyttet til bruk av høyfaste materialer i bolteforbindelser og betydningen av hydrogen utviklet ved katodisk beskyttelse. Her er det fremdeles en rekke uavklarte problemstillinger for en rekke materialer. Dette skyldes delvis uoverensstemmelse mellom erfaringer og laboratorietester. Det er også mulig at metodikken som benyttes i laboratoriet ikke er representativ for belastninger på bolter i praksis.
Galvanisk korrosjon og spaltkorrosjon:
Dette er tradisjonelle problemstillinger innen korrosjon som bør være velkjente. Dessverre brukes fremdeles materialkombinasjoner som er uegnet, f.eks. edle materialer som titanlegeringer som oftest medfører galvanisk korrosjon på lavlegerte stål og rustfrie stål. Spaltkorrosjon kan foregå på nikkelbaserte typer (som alloy 718) og rustfrie stål (som 17-4PH) under forhold med lav vannbevegelse.
Hydrogensprøhet:
Høyfaste materialer kan bli utsatt for hydrogensprøhet. Dette innebærer at atomært hydrogen diffunderer inn i materialet, slik at hydrogenet bindes i strukturen i volum med høy spenning. Dette øker muligheten for sprøbrudd ved gitte belastninger. Atomært hydrogen kan introduseres i forbindelse med syrebeising, elektoplettering eller annen behandling eller eksponering i sure miljøer. I tillegg kan hydrogensprøhet oppstå i katodisk beskyttede bolter neddykket i sjøvann. Generelt er høyfaste stål med Rockwell C hardhet høyere enn ca. 36 antatt å være utsatt for hydrogensprøhet.
Avhengig av forholdene vil dupleks rustfritt og Ni-Cr og Ni-Fe-Cr legeringer være utsatt for hydrogensprøhet under betingelser med katodisk beskyttelse i sjøvann. Utviklingen av hydrogensprøhet vil her være avhengig både av materialegenskaper, spennings- og deformasjons tilstand samt graden av katodisk polarisering. Dette innebærer at tiden til en kritisk hydrogensprøhet oppnås vil variere deretter.
Korrosjonsbeskyttelse av bolter:
Bolter av stål og lavlegert stål må beskyttes. Det finnes en rekke uorganiske og organiske belegg som kan være egnet til dette formål. Allerede i 1930 –årene gjennomførte ASTM utprøving av beskyttelse av bolter.
Valg av beskyttelsessystem må gjøres utfra behov for levetid, driftsbetingelser og miljøbelastning. Ved valg av belegg vil ofte også behov for redusert friksjon og minimale rivningsproblemer vurderes. Dette kan medføre at valg av beleggsystem vil være en optimalisering av krav til levetid og korrosjonsbeskyttelse, og ønsket om lav friksjon. Her er det behov for å kvalifisere aktuelle beleggssystemer m.h.t. effektivitet og levetid. Dette kan også danne grunnlag for et videre behov for aktuelle vedlikeholdssystemer .
Behov for F & U: Langtidstesting:
Tradisjonelt har materialvalg i bolter stort sett vært konsentrert om karbonstål og lavlegerte stål. I dag finnes en rekke alternativer for korrosjonsbeskyttelse, fra metalliske belegg og maling, til penetrereende oljer og voksprodukter. Her eksister et behov for å teste effekten av de ulike beskyttelsessystemer.
Bruken av nye og ofte høyfaste materialer til bruk i bolter er økende (f.eks. titan, austenittiske og dupleks- rustfrie stål og Fe-Cr-Ni-legeringer). En sentral problemstilling knyttet til flere av disse materialene er som tidligere nevnt, knyttet til faren for hydrogensprøhet p.g.a. katodisk beskyttelse. Det har vært utført en rekke prosjekter innen dette området både i Norge og internasjonalt, men dette har dessverre ikke gitt en avklaring på om hydrogensprøhet vil være et problem ved anvendelse av bolter i praksis. Dette skyldes at resultater fra ulike tester, samt de erfaringer som totalt foreligger, ikke alltid har gjort det mulig å trekke klare konklusjoner.
For å komme fram til mer pålitelige konklusjoner, ønsker DNV å igangsette et 10 års testprogram. Her vil utprøvingen være basert på en realistisk eksponering i felt med forspente bolter, både med hensyn til bruk beskyttelsessystemer (atmosfærisk sone on skvalpesonen), samt neddykket i sjøvann med bruk av katodisk beskyttelse. Det vil bli utført testing ved DNV’s laboratorium i Bergen og ved eksponering ved La Que Center, NC, USA. Alle tester skal forgå med forspente bolter, hvor Forspenningen blir overvåket ved det norske systemet ”Boltsafe”. Prosjektet vil således gi realistiske data om materialegenskaper, korrosjonsbeskyttelse og belastninger av bolter.
Tekst: K. P. Fischer, Sidsel Skauby, Espen B. Heier, Arne Småbrekke, Svein J. Haukenes
Kontakt i DNV, Bergen: K. P. Fischer/ Sidsel Skauby