Årsaken til problemet var at kvalitetsutviklingen på termomekanisk masse for papirproduksjon har vært stor de siste årene. Kvalitetsforbedringen gjør at masse har mer energi og økt styrke, men fører også til at det er tyngre og tar lenger tid å presse ut vannet. Blekeriet ble til slutt et stort problem for Saugbrugs, som valgte å utføre omfattende ombygginger og utvidelser av anlegget.
Oppstarten skjedde i fjor høst. -Det gamle anlegget var konstruert for å produsere 530 tonn masse i døgnet. For å opprettholde kapasiteten, måtte vi bruke kjemikalier til å hjelpe avvanningsprosessen. med det nye blekeriet har kapasiteten økt til 640 tonn i døgnet, sier driftsingeniør Geir A. Hansen på tremassefabrikk 2 (TMP 2).
Anlegget er forberedt for en ytterligere kapasitetsøkning til 700 døgntonn.
Blekeriinvesteringen på 65 millioner kroner er et ledd i en langsiktig plan for å øke produksjonskapasiteten på fabrikken i Halden. Norske Skog Saugbrugs er en av verdens ledende produsenter av SC-magasinpapir. Papirtypen brukes i magasiner, trykksaker og kataloger. Produksjonskapasiteten er 550.000 tonn papir i året og omsetningen er på om lag 2,5 milliarder kroner i året.
Tremassefabrikkene TMP 1 og TMP 2 produserer termomekanisk masse av flis for de tre papirmaskinene på Saugbrugs. Sliperiet er et anlegg som lager slipemasse for de samme maskinene. Siste produksjonstrinn for massefabrikkene og sliperiet er blekeriet. Derfra går tremassen til papirmaskinene.
Stramme tidsrammer
Det ble satt tøffe krav for gjennomføringen av blekeriprosjektet; testingen av utstyret skulle foregå mens det var full produksjon i fabrikken. Anlegget ble stoppet i bare fire døgn da det nye blekeriet skulle kjøres i gang. Alt måtte klaffe perfekt. Og det gikk som smurt.
– Tidsplanleggingen var en av de største utfordringene. Den lyktes vi bra med. Anlegget ble satt i produksjon bare 30 minutter etter det planlagte tidspunktet, forteller prosjektleder Tina Forsman ved Saugbrugs. Forsmann nevner nøye forstudier, en god hovedstudie, engasjerte medarbeidere og konsulenter med stort pågangsmot og steinhard oppfølging av leverandørene som viktige årsaker til at både kostnadsrammene og tidsplanen ble overholdt.
Forprosjektet og hovedstudien ble gjennomført allerede i 1998. Den østerrikske hovedleverandøren Andritz ble kontaktet svært tidlig, og allerede i desember 1998 var kravspesifikasjonene på utstyret klart. Da styret i Norske Skog- konsernet i januar 1999 ga klarsignal til at prosjektet kunne gjennomføres, rullet det i gang umiddelbart.
Kvalitetssikring
Ved utbygging og endring på eksisterende utstyr i industrien er plassbegrensninger et stadig tilbakevendende problem. For Saugbrugs innebar det denne gangen at de nye pressene i blekeriet måtte ta liten plass. De er derfor langt smalere enn de gamle pressene. – Underveis oppdaget vi et annet problem; det ikke var plass i bygningen til å dra ut transportskruene fra de eksisterende skivefiltrene. Løsningen var å bygge en ekstra plattform på utsiden av bygningen og lage luker i veggen som skruene kan føres gjennom, forteller Forsmann.

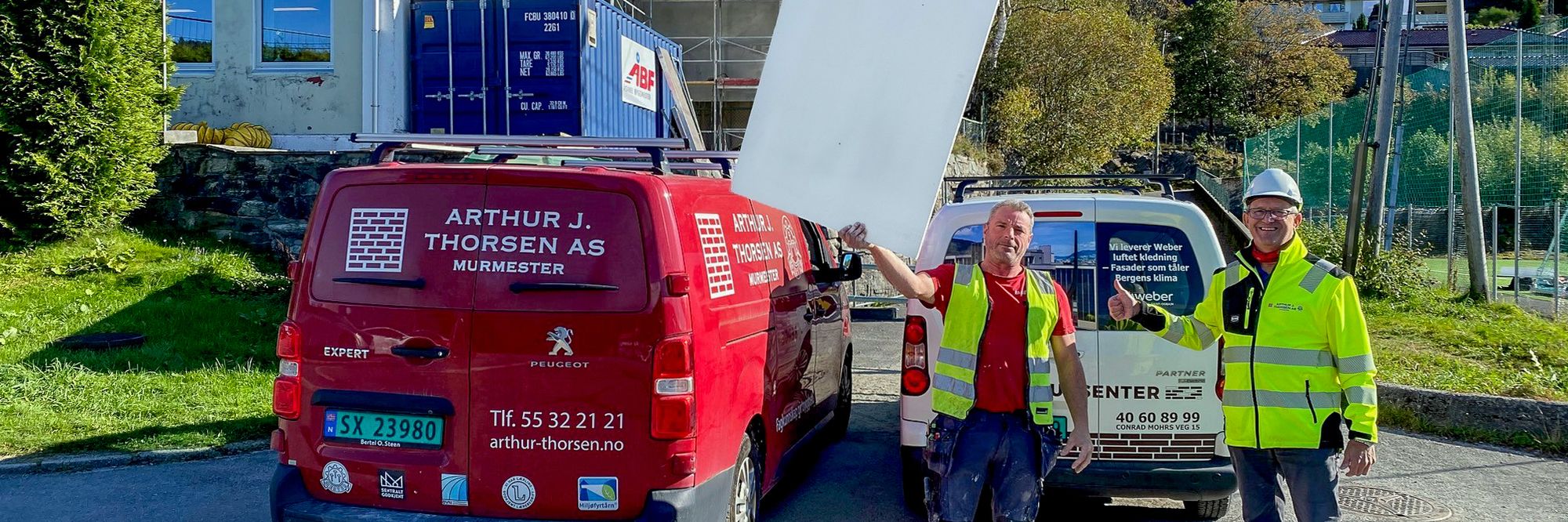
Driftsingeniør Hansen var med i prosjektgruppa for blekeriet. Saugbrugs har gode erfaringer med å involvere vedlikeholdsingeniører, driftsfolk og operatører for å kvalitetssikre prosjektene. – Dette er særlig viktig nå som anleggene blir stadig mer komplisert rent styringsmessig. Totalresultatet blir bedre og vi oppnår en høyere grad av aksept for nye anlegg, hevder prosjektleder Forsmann.
Også operatør Svein Erik Arntzen er fornøyd med gjennomføringen av prosjektet. – Det gikk veldig bra. Vi hadde ingen problemer med å overvåke anlegget i oppstartsperioden. Prosjekter gjennomføres stadig vekk, og vi har mange flinke instrumentfolk som sørger for at arbeidet er behagelig for oss operatører under testing og igangkjøring.