Går du inn på en statoilstasjon for å fylle propan, får du nå tilbud om å bytte ut den gamle blytunge stålbeholderen med en ny lett utgave, i glassfiberarmert plast. Ikke bare er den lettere, den er gjennomsiktig også, slik du kan se hvor mye propankondensat som er igjen. Dermed slipper du at sommerbiffen forblir halvstekt på grunn av gassmangel.
De nye gassflaskene, som raskt sprer seg til hytter og terrasser rundt om i landet, produseres av Ragasco. Ikke noe annet tettsted i Norge er mer forbundet med materialteknologi enn Raufoss. De fleste tenker vel på kuler i messing og støtfangere i aluminium, men industristedet syd for Gjøvik er mye mer allsidig enn som så.
Fra parabol til rakettrør
- Vi begynte å tenke på kompositter på Raufoss for over tjue år siden, sier administrerende direktør Per Sture Jenssen i Raufossbedriften Ragasco (Raufoss Gas Containers).
- Først forsøkte vi å lage parabolantenner i materialet, men det ble aldri noe av. I stedet fikk vi suksess sammen med forsvarsdelen av Raufosskonsernet. Ved å erstatte stål kunne vi redusere vekten på enkelte komponenter til en tredjedel, og øke flyenes lasteevne. Rakettrør er et eksempel på det, forteller Jenssen.
Satsingen på kompositter til forsvarsindustrien har resultert i en jevn produksjon helt frem til i dag, men har aldri nådd opp til forventningene. Det ble først fart i sakene da Volvo ønsket fiberarmerte tanker for å kjøre busser med komprimert naturgass (CNG). Mens propan kondenserer ved rundt 10 bar, krever naturgass, som hovedsakelig består av metan, et helt annet trykk. Daværende Raufoss Composites utviklet en prosess som spant karbonfiber fuktet i et epoxybad, rundt en beholder i tynn aluminium. Resultatet ble en 200 liters trykktank med en egenvekt på bare 86 kilo. Tanken har et arbeidstrykk på 170 bar og et sprengtrykk på minimum 700 bar.
- Vi er underleverandør og selger disse tankene til Raufosskonsernet, som igjen selger ferdige systemer til Volvo, sier Jenssen. Omsetningen av slike høytrykksflasker ligger på 30 millioner kroner i året.
Helautomatisert
Fabrikken for gassflaskene er en åpenbaring for produksjonsingeniører. Den kjøres døgnet rundt, og leverer en gassflaske hvert minutt. Produksjonen er helautomatisert. De fem operatørene som bemanner hvert skift, driver stort sett med vedlikehold og overvåker prosessen.
Første skritt mot en gassflaske er å blåse opp en innerforing i to millimeter polyetylen. I den sveises inn et ventilfeste, og så går den videre for å få på seg "rustningen". I en spesialutviklet, og svært hemmelig spinnemaskin, forsynes fem foringer samtidig med flere lag med polyesterfuktede helkontinuerlige glassfibertråder. Når spinneprosessen er ferdig, bærer det videre til herding. Så blir polyetylenytterkappen montert, og til slutt monteres ventilen. I løpet av prosessen blir hver flaske lekkasjetestet ved at den settes under trykk med helium, og så sniffer en sensor etter lekkasjegass.
Eksploderer ikke

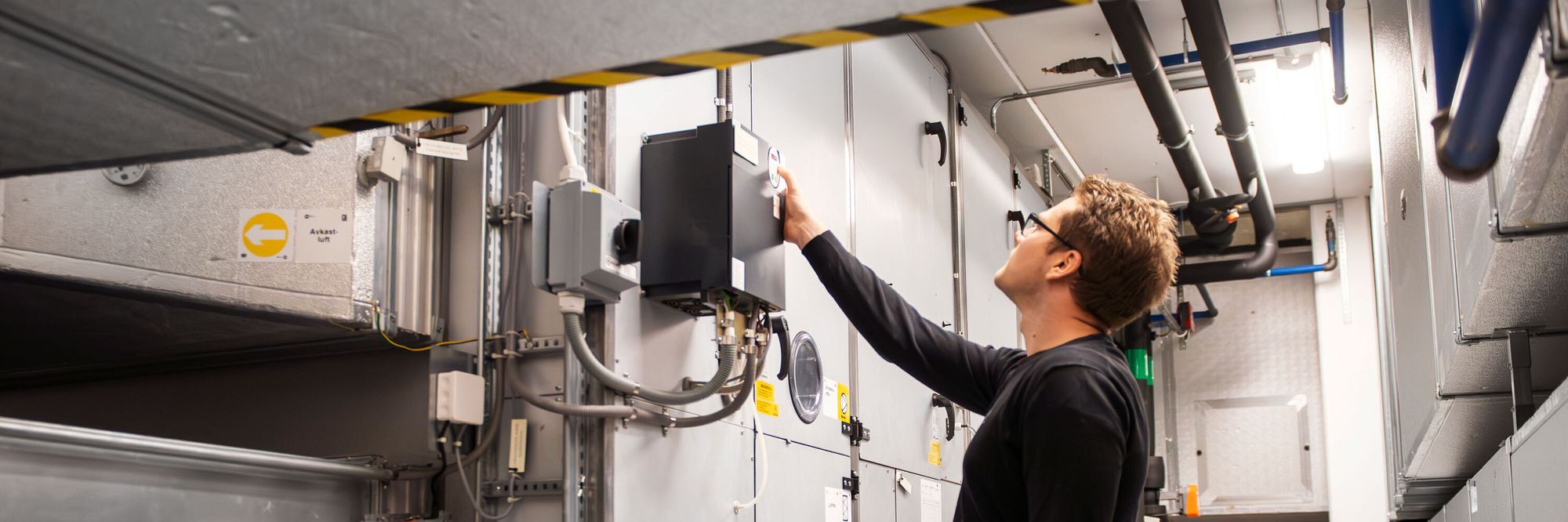
- Fordelen med glassfiberarmerte gassflasker er mer enn lav vekt, sier Jenssen. Sikkerheten er mye høyere. I stedet for å eksplodere ved en brann, forbrennes plasten og gjør at gassen lekker ut gjennom glassfibrene og brenner opp i løpet av 17 til 25 minutter.
- De fleste ulykker med slike flasker skyldes korrosjon, og det skjer ikke med de nye flaskene. I mange land, med høye temperaturer og høy luftfuktighet, slik som i Mexico, er korrosjonsproblemet svært alvorlig og forårsaker mange ulykker.
Ragasco-sjefen tror derfor at det er kan bli et stort internasjonalt marked for slike flasker. Bedriften vurderer muligheten for å sette opp en fabrikk i USA, med minst dobbelt så stor produksjon som den på Raufoss.
Ragasco var tidligere eid av Statoil og Raufoss ASA i fellesskap. I 2001 ble bedriften overtatt av Hexagon Composites AS, som har hovedkontor i Ålesund. I 2002 venter bedriften en omsetning på 100 millioner kroner.