Vi starter med en kort sammenligning av fabrikk- og kjedesporing. Sistnevnte er sporing mellom ulike forretningsenheter. Et eksempel på dette kan være sporing fra fiskefangst til fiskemelprodusent, videre til fiskefôrprodusent, deretter til fiskeoppdretter, så til distributør, butikk og endelig sluttkunde. Kjedesporing har stor dybde og vanligvis liten bredde, sjekk Sporingsskolen del 1.
Kjedesporingen begrenser seg stort sett til å registrere og lagre data for materialflyt. Sporing på fabrikknivå er (vanligvis) på mange måter forskjellig fra det å spore på kjedenivå. De viktigste forskjellene er:

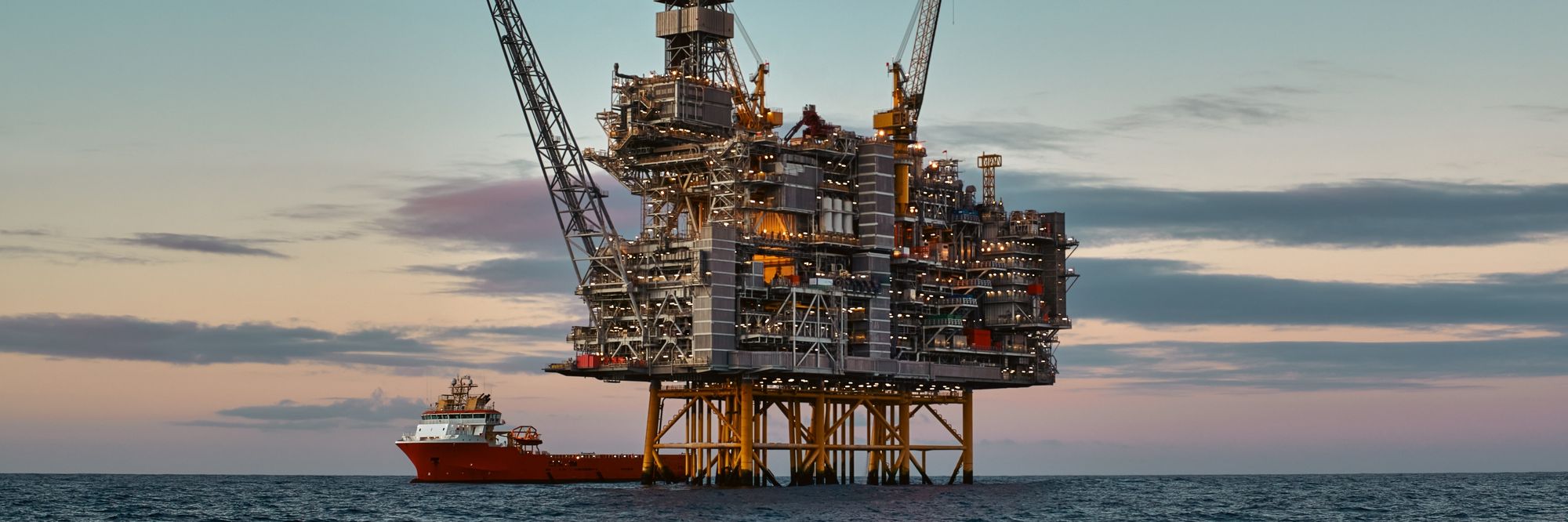
- Fabrikksporing har som oftest, i motsetning til kjedesporing, stor bredde: prosesseringsparametere, knyttet til ressursbruk, effektivitet, produsert kvalitet og prosessparametere, lagres og assosieres til identifiserte råvarer, mellomprodukter og ferdigvarer.
- Fabrikksporing er ikke avhengig av å benytte omforente standarder for datautveksling og kommunikasjon, selv om dette selvsagt er en fordel. Alt er internt i bedriften. Ved kjedesporing er en nødt til å bli enige om hvordan data utveksles mellom forretningsenheter.
- Alle data kan fritt samles og benyttes. Ved kjedesporing vil en som regel være mer restriktiv med å utveksle produksjonsrelaterte data mellom selvstendige forretningsenheter.
Ved fabrikksporing må graden av presisjon bestemmes. Det vil si hvor finmasket sporingen skal være, både med hensyn til råvarer, mellomprodukter og ferdige produkter, og med hensyn til hvilke detaljer i prosesseringen som skal spores. Presisjonen, i sporingen, bestemmes av hva som er teknisk mulig, men også selvsagt av hva som er praktisk og hensiktsmessig.
Kontinuerlige prosesser
Sporing i kontinuerlige prosesser foregår ved at masseflyt modelleres vha. massebalansemodeller. Sett fra et sporingsperspektiv, vil det oppnås best resultat (størst presisjon i sporingen) hvis masseflyten gjennom produksjonen er lineær. Det vil si ideell plugflow, og at det ikke er store blandetanker eller betydelige tilbakestrømmer i prosessen.
Massestrømmen kan da ”choppes” opp i masseplugger. Det vil si definerte mengder av materiale som flyter etter hverandre gjennom prosessen, og hvor masseplugger kan slås sammen (hvis to strømmer slås sammen), eller splittes (hvis en strøm deles i flere strømmer). Størrelsen, på massepluggene, bestemmes av hva som er hensiktsmessig og av hva som er mulig. Hver ny masseplugg får en entydig identifikator som relateres til ”foreldre-” og ”barnemasseplugger”.
Trackeren, i en kontinuerlig prosess, drives basert på flytmålinger, nivåmålinger og andre mengdemålinger online, og i sann tid. Det er viktig å ha tilstrekkelig antall målinger til å estimere massepluggenes transport og omvandling gjennom prosessen.
Det er også viktig at data og analyser/spesifikasjoner kan koples, for innkommende råvarer til massepluggene, når disse starter sin vei gjennom prosessen. Det samme gjelder kobling av labanalyser av råvarer, mellomprodukter og produkter, som tas ut underveis, til rett masseplugg.
Store blandetanker eller reaktorer er ofte involvert i prosessen. Da er det uhensiktsmessig å ”choppe” opp innstrømmen til blandetrinnet i masseplugger med mindre masse, enn det som selve blandetrinnet rommer. Selv da vil historien fra flere masseplugger, inn i blandetrinnet, smitte over på historien til massepluggene ut, i lang tid.
For helt å bryte smitteeffekten, av en masseplugg inn i en blandetank, på masseplugger ut, må blandetanken tømmes, og eventuelt vaskes, hvis vi snakker om sporing av bakterieinfiserte mellomprodukter. Det betyr at dersom sporingen utelukkende er for å kunne lokalisere bakterieinfiserte varer, i matvareindustrien, kan en operere med masseplugger eller batcher som omfatter mengder som avgrenses av tømming/vasking. Hvis vi imidlertid er ute etter sporing for å korrelere resulterende kvalitet med prosessbetingelser og råvareegenskaper, spiller det mindre rolle om vi har små korrelasjoner mellom en masseplugg og den neste.
Tilbakestrømmer i en prosess gir samme begrensninger som et blandetrinn, idet en viss prosentdel av massen, som passerer et tilbakestrømningspunkt, alltid vil komme tilbake igjen via den tilbakeførte massen.
I kontinuerlige prosesser må massebalansene alltid avstemmes. Hvis en måler inn- og utstrømning i eksempelvis en silo, vil en regnemodell, som sier at massen i siloen er lik integralet av masse inn, minus masse ut, tilslutt gi store feil nivå pga. små feil i målingene. Derfor må stadige korrigeringer fra nivåmålinger, peilinger eller høy/lav-brytere benyttes. Dette kan enkelt realiseres for eksempel vha. Kalmanfilter-teknologi.
Diskrete prosesser
Sporing i diskrete prosesser foregår også ved at en modellerer masseflyt, dvs. hvordan materialene kan flyttes gjennom prosessen. Modellene er imidlertid enklere, og av logisk karakter. I diskrete prosesser kan materiale- og materialflytting identifiseres på mange måter.
Eksempler er:

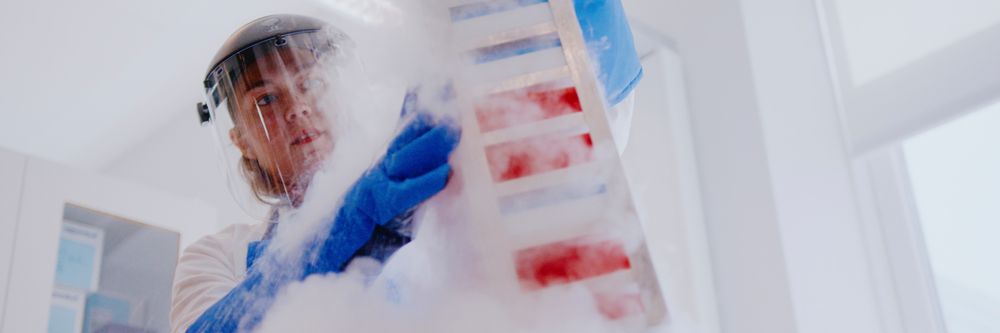
- Manuelt ved at en operatør benytter et operatørskjermbilde for å fortelle systemet at en batch eller en materialenhet er flyttet.
- Signaler fra prosessen som masseforflytninger kan avledes fra. Et eksempel er når en robot flytter et mellomprodukt fra en bearbeidingsstasjon til den neste. Her går det an å benytte prosesskunnskap. Hvis for eksempel enheter transporteres via et ”first in – first out” mellomlager, kan datasystemet holde orden på dette.
- Dersom signaler fra roboter og håndteringssystemer ikke kan benyttes, for eksempel hvis mellomprodukter mellomlagres i et mellomlager uten en fast systematikk for uthenting, må mellomprodukter som tas ut identifiseres og transporteres/prosesseres videre vha. identifikasjonsteknologi.
Neste utgave dekker ulike merketeknologier, aktiv og passiv sporing, samt prosjektering og installasjon av et sporingssystem.
Sanntids sporingsmaskin
Alle sporingssystemer må ha en sanntids sporingsmaskin. Sporingsmaskinen logger signaler og målinger relatert til driften og materialflyten i prosessen. Eksempler på dette er:
- Målinger, som syklisk leses inn fra prosessen via PLS’er, styresystemer eller annet. Sporingsmaskinen henter data via OPC eller andre kommunikasjonsprotokoller. I praksis kan det dreie seg om flere tusen signaler hvert sekund.
- Brukerinput via operatørskjermer, for eksempel å kvittere inn råvarer, å registrere manuelle målinger eller for å signalisere at et mellomprodukt er flyttet fra en prosesseringsenhet til en annen.
- Data fra manuelle eller automatiske identifikasjonsmekanismer, for eksempel strekkodelesere eller RFID-brikker (Radio Frequency Identification).
Sanntidsmaskinen vil, basert på disse dataene, beregne hvor de enkelte sporingsenhetene befinner seg til enhver tid. Sporingsmaskinen vil også forhåndsprosessere data og eventuelt gjøre modellberegninger eller andre kalkulasjoner som skal aggregeres til sporingsdata.
Når sporingsmaskinen registrerer at en sporingsenhet flyttes i prosessen, foretar den de nødvendige transaksjonene mot sporingsdatabasen for å lagre sporingsdata, samt tider for ankomst og avreise til/fra prosesserings-, transport- eller lagerenheten. Sporingsmaskinen vil også slå sammen eller generere nye sporingsenheter der dette er nødvendig. Hvis for eksempel en tømmerstokk sages opp i flere planker, skapes flere nye sporingselementer med utgangspunkt i tømmerstokken, mens tømmerstokken i seg selv forsvinner som aktivt element i sporingsmaskinens nåtidsbilde.
I Prediktors sporingssystem, APIS Click&Trace, konfigureres for eksempel sporingsmaskinen grafisk. Ulike prosesselementer dras inn på en tegnflate og koples sammen for å definere mulige materialflytveier. Sporingsmaskinen har også grafiske moduler, hvor modellberegninger, logiske operasjoner og andre beregninger kan foretas.