Fet kommune: De tre emballasjetypene kommer blandet til anlegget. Automatiseringsgraden er svært høy. Investeringen er på nærmere 100 millioner kroner.
Les: Roboter revolusjonerer i potetbingen
Fire millioner daglig
I tillegg til aluminiumsbokser, sorteres de supertynne flasketypene som Coca Cola i Norge var tidlig ute med. Grans Bryggeri i Sandefjord har nylig kjørt i gang en tappelinje for slik engangsemballasje, og Ringnes på Gjelleråsen og Farrisfabrikken i Larvik (eies av Ringnes) går over til samme type.
Maldum forteller til Automatisering at de komprimerte plastflaskene støpes om til preformer utenfor huset av andre aktører etter sortering, mens aluminiumen blir resirkulert ved Norsk Hydro i Holmestrand. Det går virkelig unna når fire millioner engangsemballasje for brus, øl og vann daglig suser gjennom automatiske sorteringsmaskiner på samlebåndene.
Les: Robotduo pakker hundepølser uten menneskelig assistanse
I løse luften
Flatklemte bokser og flasker flyr bokstavlig talt av gårde i luften i maskinene som skiller metall fra plast. Selv om vi bruker vår mest lyssterke linse (1:1,8 for den fotointeresserte), drar på med full blenderåpning og justerer opp ISO-verdien til noen tusen for å minimalisere lukkertiden, er det umulig å fange detaljene.
Først skal aluminium og PET skilles. Ifølge Maldum sørger sorteringsmaskinene fra nederlandske Bakker Magnetics for å slynge metallet litt lenger enn plasten, slik at materialene havner i ulike binger på de neste samlebåndene.
- Selv om aluminium er et ikke-magnetisk materiale, gjør en spesiell magnetvirvel trikset med å skille metall og plast, forklarer han.

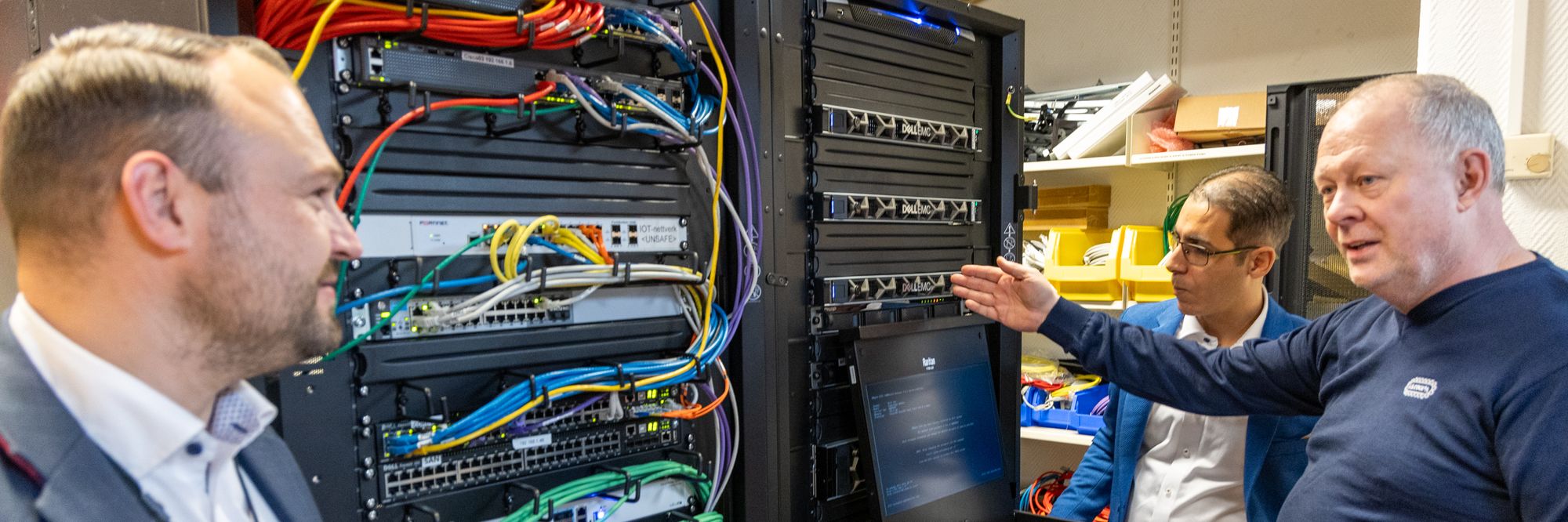
Les: Norfersks nye kjøttpakkesenter sprer ferskvare på en helt ny måte
Optisk plastsortering
Plastflaskene suser videre. Neste skritt er å segregere klar og farget plast. Driftslederen forteller at plasten blir sortert i optiske maskiner fra Titech. De stiller også med luftdyser som blåser flaskene i to retninger. Her skiller klar og farget plast lag. Maldum anslår at nøyaktigheten ligger på et par prosent. Det høres kanskje litt slapt ut, men det er krevende. Dessuten forventer han at ytelsen skal bli enda bedre.
- Vi jobber med finjustering av maskinene, forteller driftslederen.
Transportbånd kjører så ferdigsortert aluminium, klar og farget plast til hver sin presse på 120 tonn. De komprimerer materialene til klosser på en snau kubikkmeter (1 x 1 x 0,8 meter). Maldum forteller at de har bygget inn redundans i pressekapasiteten.
- Samlebåndene er fleksible slik at kan levere til hvilken som helst presse, sier han.
Les: Ekornes er norgesmester på robotisering, det neste skrittet er å få sømrobotene i full rulle
Komprimeringsgrad på 22

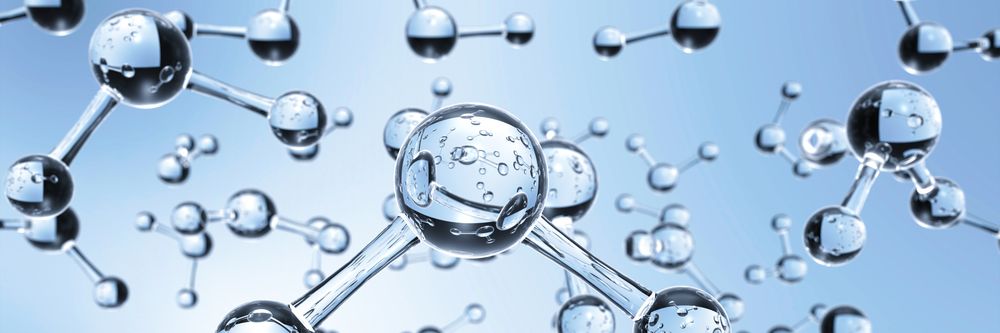
Maldum forteller at hver kloss inneholder 11 000 flasker eller inntil 22 000 bokser (0,33 liter). Det er nå vi kjøper selskapets påstand om at 22 trailere med tomgods blir komprimert til én med preform-metoden. Det kommet alltid nye flasker, og det blir mindre bruk av vaskemidler.
Driftssjefen tar oss med til mottaket av emballasje, på motsatt side av den 4000 kvadratmeter store bygningen. Her er det fire store åpninger, hver med sitt transportbånd. Maldum forklarer at to blir benyttet til flatklemt emballasje fra panteautomater. Et såkalt gående gulv (walking floor) sørger for å løse opp pappkartonger og frigjøre flate flasker og bokser.
Les: Magnesiumen på Herøya spiller igjen, med langt høyere automatiseringsgrad
RFID i hele kjeden
De to andre samlebåndene blir benyttet til mottak av hel emballasje fra kiosker, bensinstasjoner, kafeer og restauranter, eller kort sagt alt som ikke har gått gjennom pante- og komprimeringsautomater. I motsetning til betaling for komprimert retur, står Norsk Resirk for oppgjøret for panteordningen til brukerstedene.
Derfor er de gjennomsiktige plastsekkene merket med RFID-brikker. Maldum forklarer at teknologien benyttes gjennom hele kjeden, slik at Norsk Resirk kan følge flyten hele veien, fra henting til betaling til brukerne. ACT Systems har levert løsningen. Den som måtte prøve seg på juks blir raskt avslørt.
- Vi har tre industrielle panteautomater som kontrollerer hver eneste flaske og boks, sier driftssjefen.
Les: Slik fungerer RFID-teknologien
Blitsregn i panteautomat
Det ligger i kortene at industriversjonen av panteautomatene har en langt høyere kapasitet enn de vi fôrer med returemballasje i butikkene. Emballasjen suser gjennom industriversjonene én etter én, og åtte kameraer (vision-systemer) utsetter dem for et blitsregn i reneste paparazzi-stil.
- Det er kun godkjente flasker og bokser som gir klingende mynt i kassen til kundene, sier Maldum.
Hver eneste returemballasje blir registrert i en database og koplet til aktuell identitet fra RFID-brikken. Dette gir også grunnlag for betaling til brukerstedet.
Les: Automatiserings innsiktsartikkel om vision-systemer
Kontrollrom i resepsjonen
Maskinene styres av lokale PLS-er, hovedsakelig fra Siemens. Lokalpaneler er plassert på strategiske steder. Styringen er sydd sammen med industrielt Ethernet, Profinet.
Det er ikke et konvensjonelt kontrollrom. Et Scada-system med detaljert innblikk i helsetilstanden til alt teknisk utstyr er plassert i resepsjonen.
- Resepsjonisten har oversikt over funksjoner som alarmer og utløst nødstopp, og kan informere operatørene via internkommunikasjon ved behov, forklarer driftssjefen.
Han forteller at Scada-systemet også logger informasjon som strømforbruk, og kan benyttes til feilsøking og vedlikeholdsarbeid.
Les: SB Seating (tidligere Håg) har økt effektiviteten med 70 prosent siden 2005
Kjedevirksomhet
Norsk Resirks sorteringsanlegg for plast og aluminium er en vital del av resirkuleringskjeden for engangsemballasje. Driftssjef Ståle Maldum forteller at anlegget sorterer rundt 80 tonn i døgnet. Volumet vil øke med rundt 50 prosent i løpet et drøyt år, når Ringnes’ anlegg og Farris-anlegget blir ferdig modernisert. Ifølge Maldum må anlegget gå kontinuerlig, ellers vil det samle seg uholdbare mengder med emballasje utenfor.
I dag er det god plass utenfor sorteringsanlegget. Driftssjefen håper det blir to nye anlegg på nabotomtene, et for omsmelting av plasten, og et som lager preformene til nye flasker. I dag sendes plasten til Sverige for å lage preformer.
- Om vi kan lage alt lokalt sparer vi både logistikkostnader og miljøet, sier Maldum.
Et slikt grep er allerede tatt når det gjelder aluminiumen. Nylig startet Hydro i Holmestrand resirkulering av aluminium fra Norsk Resirks sorteringsanlegg på Fet. Etter lossing vil lastebilene kjøre til Larvik (Ringnes/Farris) for å hente usortert returemballasje. Det blir derfor minimalt med lastebilkjøring uten last.
Les: Duun Industrier satser friskt med automatlager og robotsveising