VANVIKAN/ÅRDAL: Utgangspunktet for bruk av sagen er dannelsen av gassbobler på anoden som er i kontakt med elektrolysebadet.
Gassboblene fører til økt elektrisk motstand og dermed mindre utnyttelse av strømmen gjennom badet. Sporene i anodene drenerer ut gassboblene til et avgassystem, og resultatet blir bedre strømutbytte.
På Årdalstangen har Hydro Carbon anlegg for produksjon av forbakte anoder. Her produseres ikke bare anoder til eget bruk i Øvre Årdal og Høyanger, men også til flere av Elkems aluminiumverk.
Dårlig løsning
Produksjonen av anoder er tidkrevende. En blanding av karbon, bek og koks «bakes» i store ovner i en temperatur på opptil 1300 grader. Hele prosessen tar tre uker før det kommer ut blokker på ett tonn med en lengde på 1,6 meter, høyde 65 cm og en bredde på 70 cm. Materialet er meget hardt og gir sagbladene en stor utfordring.
I forbindelse med modernisering av anlegget i Årdal ble det bygget et transportsystem for anodene der det inngikk utstyr for sporsaging av anoder levert av franske Brochot, som var underleverandør til TTS Handling System AS. Sagene har to parallelle sagblad som sager spor som er ca. 36 cm dype i starten og ca. 33 cm i slutten.
– I utgangspunktet skulle sagbladene med hardmetallskjær klare 3500 anoder før det ble nødvendig med bytte av blad eller skjær, men det viste seg at de bare klarte 120 anoder før vi måtte bytte, sier overingeniør Oddvin Nesse i Norsk Hydro.
Å skifte så ofte ville medført en ekstrautgift på 12 til 15 millioner kroner i året bare i verktøykostnader, i tillegg til ofte stopp i produksjonen. – Det var en meget dårlig løsning, sier Nesse.

.jpg)
Brochot avslo
I produksjonslinjen står også boremaskiner som freser ut koniske nippelhull i anodene. De brukes til å støpe inn fester for opphengsystemet. Her brukes datastyrte (NC) verktøymaskiner med bor som er produsert av Lyng Drilling. Borene er basert på teknikken de bruker i sine diamantborekroner for offshoreindustrien.
Metoden er patentert av Hydro og fører til mindre vrak enn forming av hullene i forkant av bakeprosessen. Dessuten står de friere med hensyn til hullene siden noen kunder bruker to eller tre fester, mens andre bruker fire.
– Da vi hadde gode erfaringer med diamantverktøy for boring av nippelhull, ba vi Brochot om å ta kontakt med Lyng Drilling for å bruke diamant i stedet for hardmetall i sagbladet, sier Nesse.
Dette avslo Brochot, men Hydro og Lyng Drilling satte i gang et samarbeid for å utvikle et diamantsagblad. Denne prosessen var i god gang da de første sagbladene med hardmetall ble uttestet. Da det ble konstatert at hardmetall var mislykket, var første prototyp diamantblad klar for uttesting.

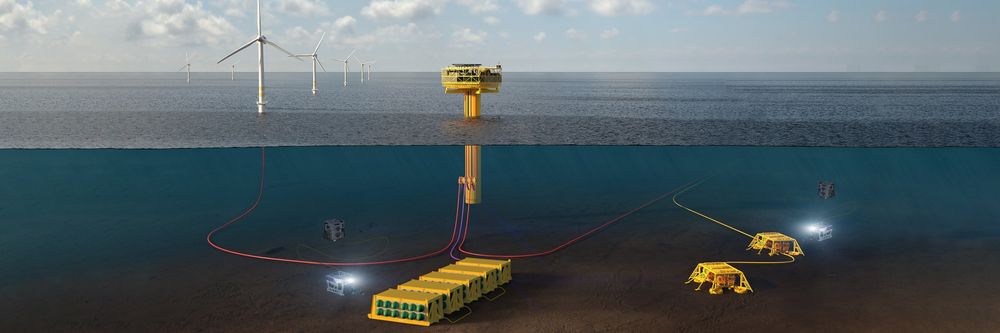
Tredje generasjon sagblad
Ved hjelp av DAK-systemet SolidWorks konstruerte Lyng Drilling et nytt blad hvor 48 skjær er festet til bladet med skruer. – Utfordringen videre er å lage et blad hvor vi kan redusere sporbredden ytterligere, sier teknisk sjef Hans Seehuus hos Lyng Drilling AS i Vanvikan. Første utgave hadde en sporbredde på 16 mm, nå er den nede i 13 mm. Selve diamantskjæret har en tykkelse på ca. 1 mm.
– Vi maskinerer alt her i våre lokaler i Vanvikan, sier produksjonssjef Jan Egil Pallin. De har lagt ned mye arbeid på å finne stålkvaliteter og en produksjonsmetode som gjør bladet mest mulig plant. De har også hatt kontakter mot sagbrukindustrien for å se hvordan de løser problemer med stabilitet på bladet.
– Da vi satte inn første generasjon sagblad, fikk vi problemer med vibrasjoner fordi selve maskinen var for dårlig konstruert. I samarbeid med den norske leverandøren av transportsystemet (TTS), ble sagene ombyd. Underveis har vi testet flere generasjoner av bladet, forklarer Nesse. Nå er tredje generasjon sagblad i drift.
Da sagbladene ble utviklet, var målet å klare 20.000 anoder før skjærene måtte byttes. – Aluminiummiljøet er relativt lite og nye ting ryktes fort, forteller Nesse. Da vi hadde kjørt 40.000 anoder, mente aluminiumprodusenten Alcan Grand Bye i Canada at dette var et mirakel. De er nå veldig interessert i å bruke dette på sine anlegg verden over, sier han.
Etterpå har de klart å kjøre 80.000 anoder på ett blad. – Det er vi meget godt fornøyd med, sier Nesse. Også på Sunndalsøra har Hydro egen produksjon av forbakte anoder. Der brukes også de nye diamantbladene fra Lyng Drilling.
Har søkt patent
Hydro og Lyng Drilling har søkt om patent i en rekke land på sagbladet, vinkling av skjærene og oppbygging av skjæret. Begge selskapene fremholder det gode samarbeidet . – Hydro er meget behjelpelig hvis vi ønsker å ta med kunder for å vise sagbladet i arbeid, sier adm. direktør Kjell Haugvaldstad i Lyng Drilling. Han mener det er riktig at Hydro ikke holder dette for seg selv.
– Vi tror dette kan bli et nytt viktig produkt for oss, sier han. – Vi kunne holdt kortene tett til brystet, men det ville bare ført til at det hadde blitt utviklet andre metoder. Nå får tross alt Hydro noe igjen for sine utviklingskostnader, sier Nesse.