Selskapet håndterer rundt en tredel av den norske potetproduksjonen, om lag 100 000 tonn årlig.
Les også: Freia melkesjokolade blir nå laget med flunkende ny styring
Hoff-leverandør til Arcus
I andre enden av selskapets fire fabrikker kommer det store mengder ren sprit, potetmos, potetgull, pommes frites og annen potetbasert snadder. Det er bare en liten del av produktene som bærer Hoff-navnet. Selskapet er hoffleverandør av råvarene til norskprodusert akevitt og Vikingfjord, og de lager blant annet Sørlands Chips og Mills potetmos.
Ole Solberg, vedlikeholdsleder for anleggene på Gjøvik og Brumunddal, forteller at automatisering er et sentralt element i de kontinuerlige forbedringsprosessene. Over halvparten av investeringene som selskapet gjør er relatert til automatisering, enten det dreier seg om instrumentering eller komplette maskiner.
Les også: Roboter revolusjonerer potetbingen, pakker 40 000 tonn i året
Spriter opp satsproduksjonen
Det siste tilskuddet er dette helautomatiske potetmeskeriet. Solberg forteller at det mates med poteter, inkludert overskuddsmaterialer fra andre produkter, som er kvernet ned til omtrent én kvadratmillimeter. Da er stivelsen borte, men fremdeles tilgjengelig for gjæring. Massen blandes med vann og gjær i satsdunkene. De er på 45 kubikkmeter hver. Tilsetning av nitrogen setter fart på prosessen. Uten nitrogen ville det tatt ca. en uke.
- Produksjon av sats tar 36 timer, sier han.
Investeringen ligger på nærmere 20 millioner over fem år, og meskeriet har fått et nytt utseende. Tanker, rør og annet prosessutstyr minner om et meieri, det skinner av det hygieniske utstyret. Automatiseringen i det nye anlegget er dessuten en revolusjon sammenlignet med meskeriet som blir erstattet.

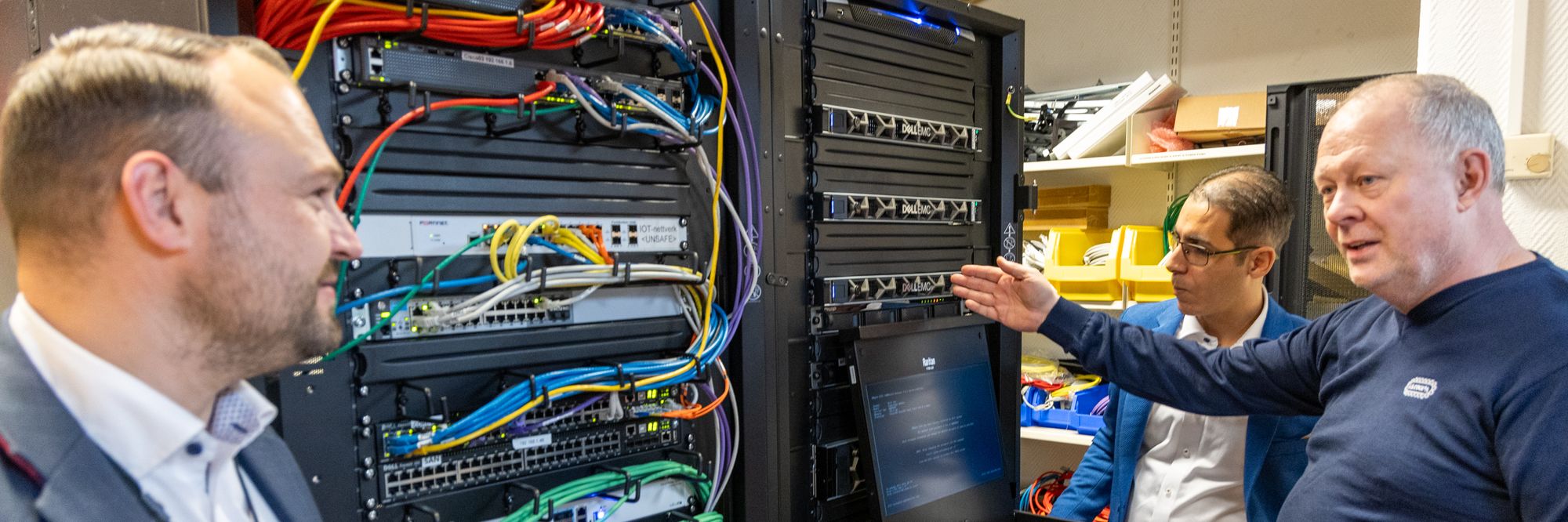
- Det hadde en håndfull ventiler. Det nye har om lag 180 av- og på-ventiler fra Alfa Laval og et dusin reguleringsventiler fra Samson, forteller Solberg.
Les også: Lilleborg har vasket bort den gamle styringen
Satset på standardisering
Økt seksjonering skal bidra til høyere produksjon, bedre fleksibilitet og vaskeprosesser (CIP, Cleaning In Place). Instrumenteringssiden har også fått et løft. Meskeriet har et dusin trykk- og temperaturmålere fra Baumer, og et dusin mengdemålere fra Endress+Hauser, både elektromagnetiske og Coriolis. Hoff har standardisert på Profibus PA for instrumentering, og meskeriet er intet unntak.
- Reguleringsventilene og samtlige instrumenter kjører på Profibus PA, sier vedlikeholdslederen.
Kommunikasjonen med av- og på-ventilene utføres også kollektivt, på AS-Interface (ASI). Meskeriet er altså fritt for konvensjonelle signalkabler. Styringen føyer seg pent inn i rekken av et femtitalls Siemens PLS-er ved Gjøvik-anlegget. Solberg forteller at de fra slutten av 90-tallet har standardisert på slike maskiner og produsentens pc-baserte Scada-system, Wincc. Han forteller at standardiseringen også gjelder prosessinstrumenter fra Endress+Hauser og Profibus PA.
Les også: Magnesiumen på Herøya spiller igjen, med langt høyere automatiseringsgrad

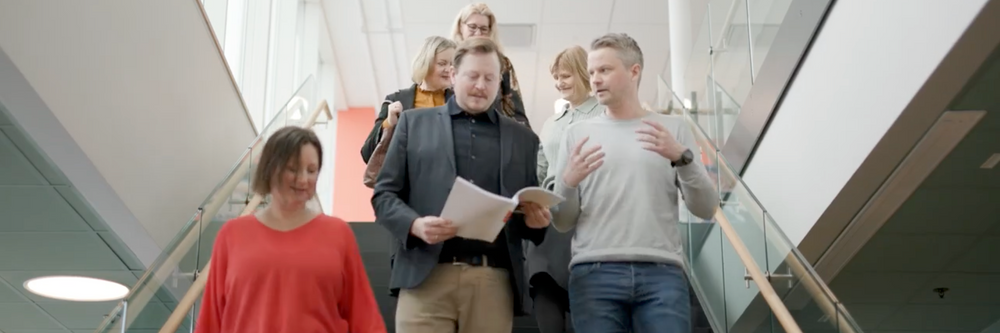
Beste brenneri
I dag har Opplandsfabrikken 250 instrumenter på feltbussen. Vi utfordrer vedlikeholdslederen når det kommer til både valget og nytten av PA. Han medgir at det handlet litt om tilfeldigheter, og at de nok kunne gjort mer med informasjonen i feltutstyret. Samtidig slår han fast at teknologien fungerer svært bra. Beviset er kanskje den gjennomførte satsingen på bussløsninger i det nye meskeriet.
Potetbearbeiderne liker å strekke seg. Solberg forteller at det er nødvendig for å henge med i kampen om å beholde produksjonen i Norge. Et annet eksempel på innsatsen er at de bygget Europas mest automatiserte brenneri i 2008. Det renser satsen fra meskeriet. Etter fem runder er sluttproduktet på 96 prosent alkohol klar som råvare for norsk akevitt og vodka hos Arcus. Hele brenneriet er en egensikker sone (Ex). Derfor vil Hoff ha bygningen mest mulig folketom.
- All kontroll og overvåking gjøres fra et kontrollrom som håndterer både meskeriet og destilleriet, og det ligger i en annen bygning, forklarer vedlikeholdslederen.
Les også: Kjøttpakkesenter sprer ferskvare på en helt ny måte
Oversikt fra kontrollrommene
Gjøvik-anlegget har to kontrollrom. Det andre dekker produksjon av fast føde som potetmos og pommes frites.Siemens Wincc regjerer som nevnt på begge steder. Solberg forteller at anlegget har totalt 22 000 tags (punkter) i systemet. Feltsignaler er det færre av, da deler av utstyret har flere parametere.
Majoriteten av signalene fra prosessdelen er på plass, og det er også det området Hoff arbeider mest med å komplettere. Han anslår at rundt 60 prosent av signalene fra matproduksjonen er samlet i kontrollrommet. Det er stort sett pakkemaskiner som lever sitt eget liv, med lokalpaneler. Det er vedlikeholdslederen foreløpig fornøyd med.
- Vi må uansett ha operatører på de aktuelle områdene hele tiden, sier Ole Solberg.
Les også: Scandinavian Business Seating på Røros er verdensledende på masseprodusert skreddersøm
Fanger forbedringer
Hoff forventer at et automatisk datafangstsystem skal føre til en reduksjon på ti prosent i energiforbruket. Da Automatisering var på besøk ved anlegget i Gjøvik hadde vedlikeholdsleder Ole Solberg nettopp bestilt fire nye Vortex-mengdemålere for damp. I tråd med selskapets standardisering skal målerne snakke Profibus PA.
Les også: Robotduo pakker hundepølser uten menneskelig assistanse hos Vom og Hundemat
Nøkkeltallene skal frem
De får godt selskap av andre energimålere i det store anlegget. Fabrikken konsumerer store mengder energi for produksjons- og vaskeprosessene for å bearbeide 100 000 tonn poteter årlig. Solberg forteller at de er i startfasen med datafangstsystemet, som har automatisk overføring av informasjon fra styringssystemet til et datavarehus. Enova bidrar økonomisk. Energimålingene er første etappe.
- Vi tar blant annet ut nøkkeltall som energimengde per produsert liter sprit, forteller vedlikeholdslederen til Automatisering.
Hoff har allerede erfaring med datafangst, for logging av effektivitet, eller OEE (Overall Equipment Effectiveness). Solberg forklarer at de har kjørt en blanding av automatisk og manuell innsamling. Nå skal informasjonen inn i datavarehuset sammen med energimålinger og andre relevante parametere.
- Det blir et viktig verktøy for kontinuerlige forbedringer, sier han.
Les også: Fiskefôrprodusenten Skretting reduserer kostnadene for energi med flere millioner kroner per år
Maskinbytte etter OEE-analyse
Solberg forteller at OEE (produktet av kvalitet, tilgjengelighet og ytelse) typisk svinger mellom 60 og 90 prosent. Selskapet bruker nøkkeltallsindikatoren til mer enn fintrimming av produksjonen. Dårlig ytelse fra en maskin har også ført til at den ble erstattet. Vedlikeholdslederen trekker frem fordelen ved å kunne dokumentere rikets tilstand.
- Vi skiftet en maskin for et par år siden. Den stod for halvparten av stopptiden på linjen, og for 17 prosent av total nedetid på våre fire fabrikker, forklarer Solberg.
- Det var lett å overbevise ledelsen om at maskinen måtte byttes.
Les også: Automatiserings innsiktsartikkel om OEE