RØROS: Da Lockheed Martin bestilte 500 Håg-stoler til sine ingeniører på romfartssenteret i Denver, Colorado, fikk de muligens kvantumsrabatt.
Men for produsenten ville det ikke kostet mer å produsere én stol enn 500 like.

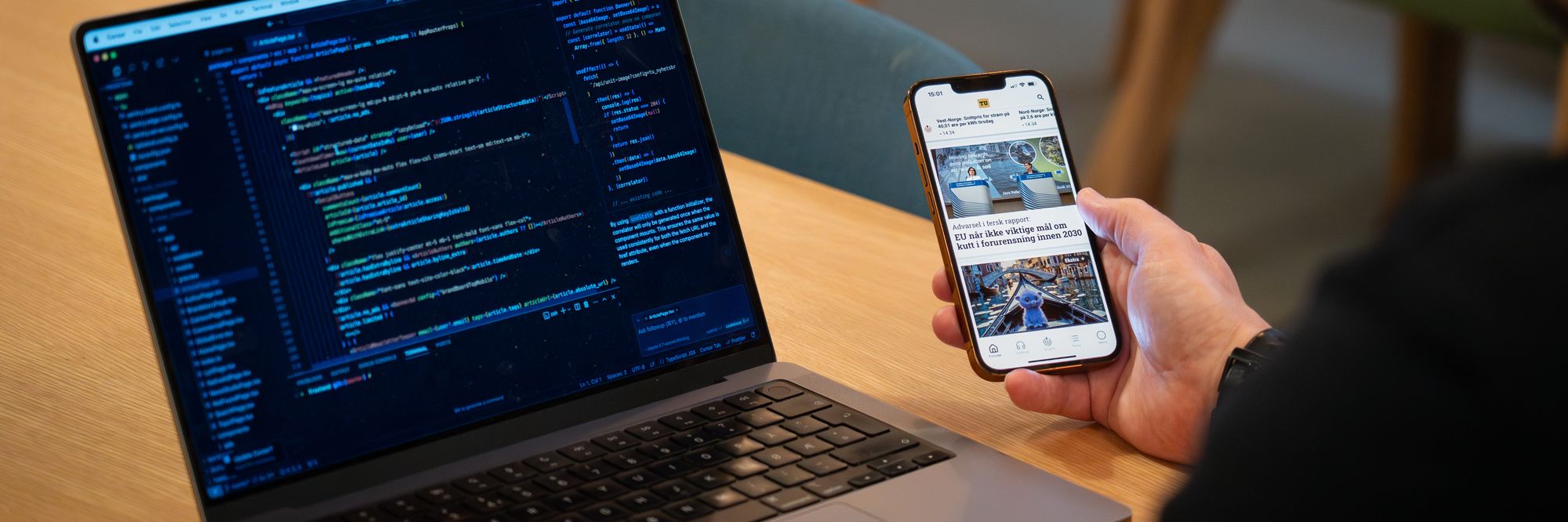
– Vi liker å kalle det masseprodusert skreddersøm, sier Torbjørn Iversen som er direktør for produksjon og logistikk i Håg-eieren Scandinavian Business Seating.
Langt mer effektivt
Du må være fleksibel og effektiv i alle ledd og ha et stort varespekter, men desto mindre leveringstid, for å være i stand til å fortsette å produsere konkurransedyktige kontorstoler på Røros.
Denne vissheten lå til grunn da Håg startet et automasjonsprosjekt for snart fire år siden. Det handlet om å effektivisere egen produksjon og outsource alle andre prosesser.
Det har gjort at fabrikken i fjor produserte 300.000 stoler med drøyt 200 ansatte, sammenlignet med 200.000 stoler i 2000 med over 300 ansatte.
Gjennomløpstiden per kontorstol ligger på 15-20 minutter, mens den tidligere var 2-3 dager.
– Utfordringen når man skal automatisere, er at det ofte bygger inn masse begrensninger. Det var essensielt for oss å være minst like fleksible som før, påpeker leder for produksjonsutvikling Stein Are Kvikne som kom inn i bedriften samtidig med automatiseringsprosjektet.
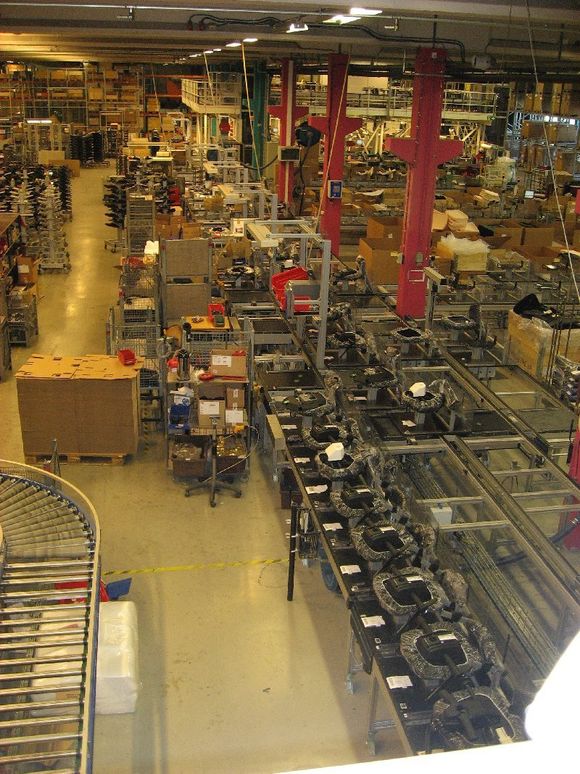
Logistikk – ikke robotisering
Automatiseringen på Håg har ikke dreid seg om å installere nye roboter for sveising og montasje. Det ville fordret større volum og serier, noe den ordrestyrte bedriften har lite av.
Gjennomsnittsordren er på 1-2 stoler. I stedet dreide prosjektet over til å bedre den logistiske flyten. Det har ført til at monteringstida nå er halvert sammenlignet med før ombyggingen. Det samme er kostnadene.
Det skjedde etter at Sintef var med og analyserte virksomheten på gulvet og påviste at én tredel var såkalt verdiskapingstid, mens to tredeler var indirekte tid som gikk med til leting og transport av deler på kryss og tvers.
Angrepsvinkelen ble altså å redusere interntransporten samt å legge til rette for å samle alle prosesser som kan automatiseres på ett punkt.
Kaosproduksjon
Håg har 70 ulike kontorstolmodeller. Når man ganger opp dette med tilsvarende antall valg stofftyper, rygghøyder, understell og så videre, blir det mange millioner ulike kombinasjoner.
Likevel skal Håg kunne levere det meste fra produktspekteret innen 1-5 dager.
.png)
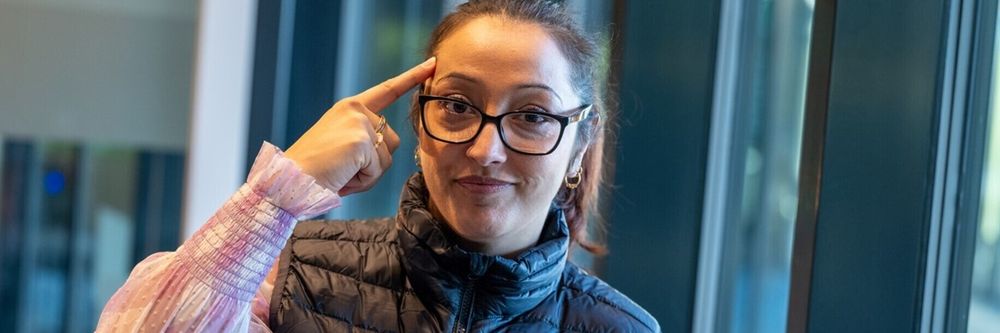
Der det tidligere ble produserte stoler på modellvise linjer, kommer nå alle stoler, unntatt konferansestolen H09, langs samme produksjonslinje i kaosproduksjon.
Nå har fabrikken en palettbaneløsning der det er hektet på et visst antall arbeidsstasjoner. Stolene monteres fortsatt for hånd.
– Det har tillatt mer sekvensering av produksjonen. Ingen dager er gjennomsnittlige på Håg. Det eneste vi vet sikkert om produksjonen er at den endrer seg hele tiden. Løsningen for oss har vært fleksible moduler der vi kan flytte på arbeidsstasjonene uten store kostnader, sier Kvikne.
Ny fabrikk i fabrikken
Produksjonen på Håg er ordrestyrt med en software som knytter sammen ordresystemet og produksjonssystemet.
Softwaren overvåker hva som skal gjøres ved hver enkelt arbeidsstasjon og hvilke deler som finnes der.
Ut fra denne informasjonen skapes en egen rute på produksjonslinjen over hvilke stasjoner akkurat denne kontorstolen skal besøke før den når målet – pakkestasjonen.
Slik kan også problemer på linja avdekkes umiddelbart. Til og med produksjonskostnadene per stol kan avleses i sanntid.
Samlet har Håg investert 15 millioner kroner i utstyr i det treårige automasjonsprosjektet. I tillegg har forskningsrådet har bidratt med nærmere tre millioner kroner til forskningstjenester.
Ombyggingen på fabrikken i utkanten av Bergstaden ble gjort i løpet av tre somre.
Riktignok mens det var produksjonsstans, men like fullt ble en ny fabrikk bygget om inne i en fra før smekkfull produksjonshall. Etter automatiseringen er det imidlertid blitt bedre plass.