Helly Hansen ønsker å bli i Norge med produksjon.
– Paradokset i prosjektet har vært at vi skulle begynne å automatisere med det mest komplekse sikkerhetsutstyret du kan tenke deg, sier produksjonssjef Ivar Grøneng i Helly Hansen Spesialprodukter.
I dag er nemlig produksjonsprosessen stort sett manuell, og produksjonslokalet i Moss er fullt av damer bak symaskiner.
– Vår strategi er å opprettholde produksjonen i Norge. Vi klarer det hvis vi går inn for det, men det er ikke enkelt, og vi må bruke ressurser på det. Derfor passet Tempo-prosjektet som hånd i hanske for oss, sier Grøneng.
Mann til månen
Tempo-prosjektet ble sparket i gang for to år siden.
Fire bedrifter er med: Helly Hansen Spesialprodukter, Ekornes, Arcus og Kongsberg Automotive. Prosjektet er støttet av Norges forskningsråd, og RTIM (Raufoss Technology and Industrial Management) har stått for prosjektledelsen.
Denne typen prosjekter kalles «Mann til månen» fordi de skal finne nye løsninger på eksisterende utfordringer.
– Fellesnevner for de fire bedriftene er at de har kompliserte produksjonsprosesser. Målet har vært å finne metoder for automatisering av hele eller deler av produktet, sier prosjektleder Tor Giæver ved RTIM. Han har ledet Helly Hansens del av prosjektet, og er stolt over at de har kommet så langt på så kort tid.

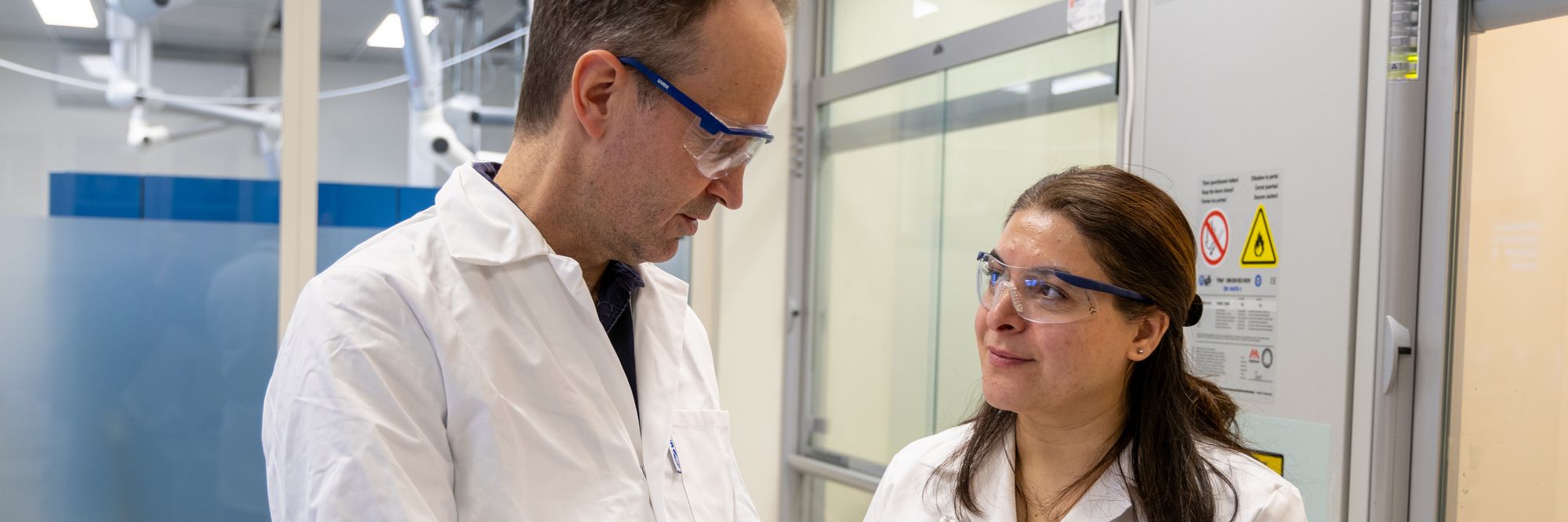
Ny drakt
– I løpet av prosjektperioden satte Statoil nye krav til sine redningsdrakter. Helly Hansen Spesialprodukter tok utfordringen og brukte caset i prosjektet. Resultatet ble en ny drakt forberedt for automatisert produksjon, forteller Giæver.
I dag er kontrakten med Statoil signert, og serieproduksjon av redningsdrakten starter i løpet av januar.
– Drakten er en kompromissløsning. Vi måtte ta hensyn til krav fra kunden og nye myndighetskrav, sier prosjektlederen.
Helt automatisert har dermed ikke produksjonen blitt. Men automatiseringstanken har vært med i hele utviklingsprosessen. Søm heter ikke lenger søm, men sammenføyning. Den kan foregå på gamlemåten, eller for eksempel med laser- eller ultralydsveis. Drakten er delt opp i moduler, der noen deler er like uansett hvilken størrelse det er på drakten. Nye materialer er brukt, og logistikken rundt produksjonen vil bli ny.
– Den nye drakten bygger på gammel kunnskap og gamle løsninger, men ingenting av det gamle er med – alt er nytt: Materiale, teknologi osv. For oss er dette et nytt produkt selv om drakten ser ganske lik ut som de gamle redningsdraktene, forteller Ivar Grøneng.

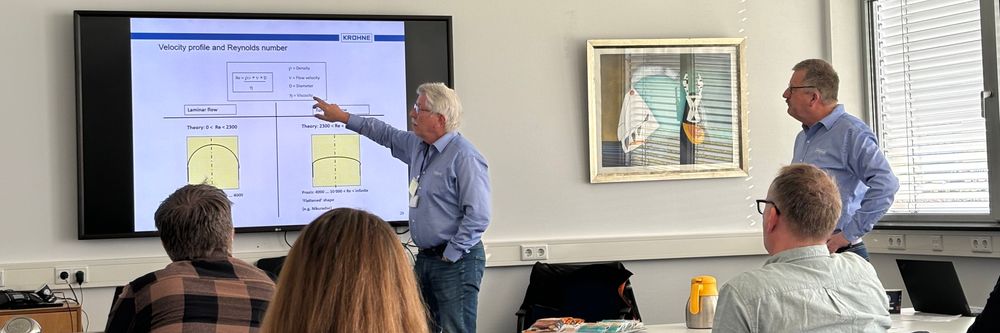
Bryter nytt land
Produksjonslinjen vil bli satt sammen på en ny måte for å øke produktiviteten og gi en tydeligere vareflyt. – Vi har stykket opp drakten og samlet like prosesser. Disse vil bli organisert i celler for å få en naturlig flyt i produksjonen. Dermed kan vi se på automatiseringsmuligheter innen hver celle, sier Giæver.
Teko-industrien har svært mye å gå på når det gjelder automatisering. – Produsentene har flyttet produksjonen lenger og lenger øst for å få ned kostnadene. Dermed har det ikke vært incentiver for å jobbe med automatisering i Europa. På mange måter bryter vi nytt land, og vi må være ydmyke i forhold til at det tar tid, sier prosjektlederen fra RTIM.
Utålmodige
Teknologien har ikke kommet så langt at det er mulig med full automatisering av søm ennå. Giæver kjenner til ett forsøk i Japan på slutten av 80-tallet, som det ikke kom noe ut av. Dermed er neste skritt å få maskiner som er gode nok til at målet kan nås. – Vi er utålmodige på teknologiutviklingen, og synes det går litt seint, innrømmer Grøneng.
I løpet av året er planen å sette opp en pilotcelle for å kunne teste ut nye teknologier for automatisering. En robotlab skal bygges på Raufoss, og den skal gjøre innledende forsøk med robot og søm. – Ekornes har blant annet investert i denne. De har kommet relativt langt, og har også investert i en sømautomat med flere integrerte prosesser, forteller Giæver.
Ingen mirakler
For de to siste deltagerbedriftene, Kongsberg Automotive og Arcus, har målet vært å få frem et godt 2D eller 3D vision system, som kan detektere porer i maskinert støpegods eller skille mellom ulike vin- og brennevinstyper – alt etter hva produsenten har bruk for. Underveis i Tempo-prosjektet har internasjonale industri- og forskningsmiljøer bidratt, i tillegg til at Sintef har deltatt i samarbeidet.
– Prosjektet har åpnet dører og gitt kontakt med nye miljøer. For Helly Hansen Spesialprodukter har det i tillegg bidratt til å utvikle et nytt produkt på kort tid, sier Giæver.
– Jeg tror ikke vi hadde fått det til uten nytt tankegods i starten, og vi hadde nok lukket mange dører underveis. Jeg er fornøyd med prosessen, selv om mirakelmaskinene jeg hadde håpet på ikke er på plass, sier Grøneng.