Som en naturlig del av petroleumsproduksjon, skitnes prosessutstyret til og det blir avsetninger på utstyret. I verste fall kan dette føre til produksjonsstans og reduksjon av sikkerhet.
Avsetningene består av helsefarlige komponenter. Når utstyret skal vaskes og renses, har det derfor vært en utfordring at personell gjør dette manuelt, og at de blir eksponert for ulike former for hydrokarboner, benzen, kvikksølv og lavradioaktive komponenter, for å nevne noe.
Les også: Dette er oljearbeidernes favorittplattformer
Vann og kjemikalier
Det norske selskapet Safeclean leverer tjenester til industrien, der vaskingen av prosessutstyret gjøres automatisk. I tillegg kildesorteres vaskevannet ved å sortere ut de farlige stoffene for å behandle dette korrekt.
– Dette gjør vi med sirkulasjonsvask hvor vann og dedikerte kjemikalier benyttes. Løsningene er vel utprøvde på ulike former for utstyr og systemer offshore i løpet av disse årene, sier Jon Refsnes til Teknisk Ukeblad.
Prinsippet Safeclean benytter seg av fungerer ved at det aktuelle systemet fylles med en vaskeblanding bestående av vann og kjemikalier. Deretter etableres en lukket krets, og løsningen varmes opp og sirkuleres over en tidsperiode.
– Kontinuerlige målinger foretas på væska med tanke på progresjon i renseprosessen. Etter endt sirkulasjon dreneres kretsen og systemet er friskmeldt. Avtappet væske avhendes eller kildesorteres, forklarer Refsnes.
Les også: Miljøvernerne jubler over denne ferga
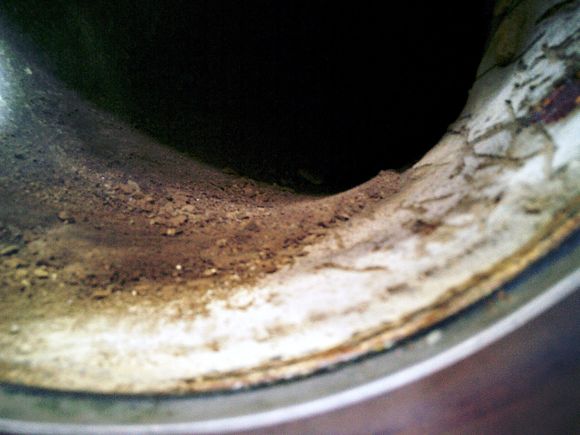
180.000 liter væske
Gjennom produksjon av olje og gass dannes det belegg på innvendige overflater i større deler av prosessanlegget.

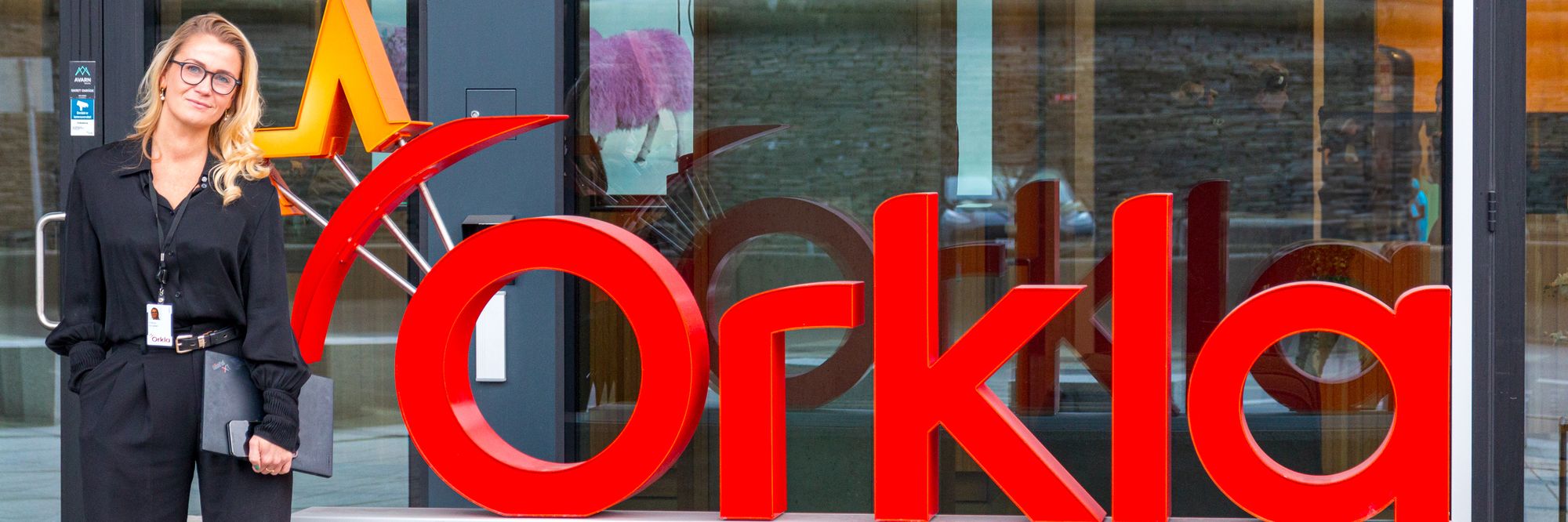
Belegget som dannes kommer naturlig fra bestanddelene i reservoaret. Disse beleggene kan skape store driftsforstyrrelser, og de kan i verste fall medføre reduksjon i produksjon eller utgjøre en reell sikkerhetsrisiko, ifølge Refsnes.
– I dag fjerner bransjen disse beleggene i stor grad med manuelle metoder hvor personell er sterkt involvert. Belegg er ofte befengt med helsefarlige komponenter. En automatisk rengjøring i lukket system sikrer at personell ikke blir eksponert, sier han.
Safeclean mener for øvrig at deres arbeid passer best til felt som er i haleproduksjonen.
– Jo eldre et felt er, desto mer vann produseres. Noen produserer over 90 prosent vann og 10 prosent olje. Da er det enorme mengder vann som skal behandles. Utstyret om bord som renser det produserte vannet får disse beleggene. Konseptet vårt er nok derfor mest essensielt der felt er i haleproduksjonen, sier han.
Refsnes viser til en større jobb som er gjort i år der det ble sirkulert 180.000 liter væske for å få behandlet anlegget under revisjonsstansen.
Dette tok rundt 36 timer.
– Det ble fjernet nærmere 60–80 tonn belegg. Etter jobben ble et eget fartøy koblet opp, og væsken ble fraktet til land for videre behandling. Nå kvantifiseres resultatene, både med tanke på de økonomiske og miljømessige gevinstene, sier han.

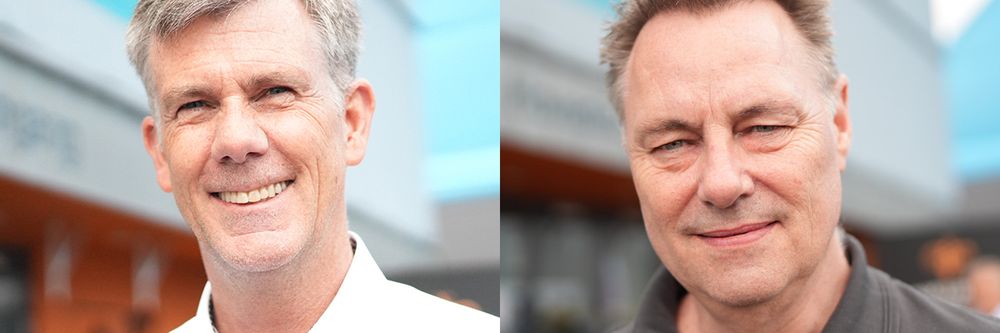
Les også: Lundin-sjefen: - Dersom vi bare spiller golf, vil vi fortsatt doble produksjonen
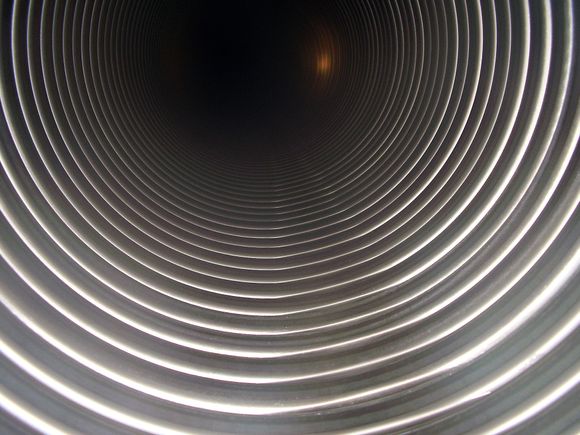
Vil være best i klassen
Selskapet har 40 ansatte, i Kristiansand og Høyanger. De mener selv at de har et konkurransefortrinn i markedet, da de utvikler kjemikaliene selv.
– I tillegg er vi også en nisjebedrift, som utelukkende holder på med dette. Det som er vår mulighet, er å være best i klassen, sier Refsnes.
Selskapet har fått drahjelp av både Innovasjon Norge og av industrien, som har støttet opp rundt diskusjoner og spesifikke ønsker fra industriens side. Foreløpig retter selskapet seg kun mot norsk sokkel.
Les også:
Disse 7 tingene må du aldri gjøre på jobbintervjuet