Ringsaker: Han forteller til Automatisering at prosjektoppgavene den siste tiden har tatt helt av. Nå skal han bruke all sin arbeidstid som prosessleder på kontinuerlige forbedringer og forandringer ved meieriet fram til høsten.
Operatøren på gullstol
Knut-Arne forklarer at han alltid tenker på operatørens beste, uansett om han arbeider med drift, vedlikehold eller prosjekter. Han er selv meierist, og arbeidet i flere år med driften i meieriet før det ble automatiseringsoppgaver på heltid, og vel så det.

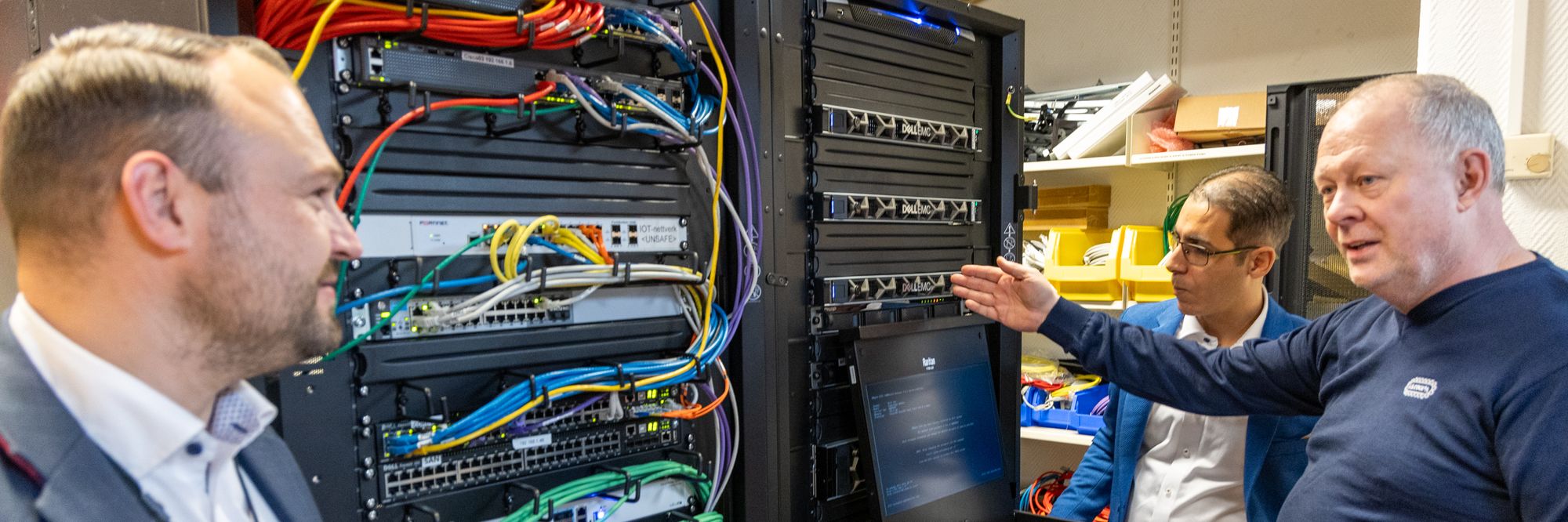
Vil samle operatørkompetansen
Meieristen innrømmer at flere kollegaer er skeptiske til hans framtidsdrøm om et felles kontrollrom for hele meieriet. Knut-Arne har allerede blinket ut stedet, som han viser oss på en rundtur i anlegget. I dag består meieriet av fire kontrollrom, og Knut-Arne forteller at det ikke er økonomiske motiv som driver ham.
– Et team med multidisiplin kompetanse er bedre enn å sitte på hver sin tue, mener han.
Argumenter som nærhet til utstyret med lokale kontrollrom preller av som vanndråper på blikktak hos Knut-Arne.
– Det gir falsk trygghet. Operatørene ser uansett bare et utsnitt av sin anleggsdel, forklarer han.
Les også: CGMs vision for bedre kontrollrom
Smartere ressursbruk
Prosesslederen ser for seg at de ulike miljøene deler på patruljeringen ute i meieriet. Han mener det er en smartere måte å bruke ressursene på, og trekker fram nok et argument når det kommer til å samle operatørene.
– Det er stor variasjon i erfaring blant DCS-brukerne. Noen bruker systemet bare en sjelden gang, andre jobber med det daglig. Å samle all kompetanse på ett sted er garantert fordelaktig, sier Knut-Arne.
Om han får gjennomslag for kongstanken gjenstår å se. I mellomtiden viser han oss rundt på det omfattende anlegget som bearbeider 100 millioner liter melk i året.
Lavkarbo driver prosjekter
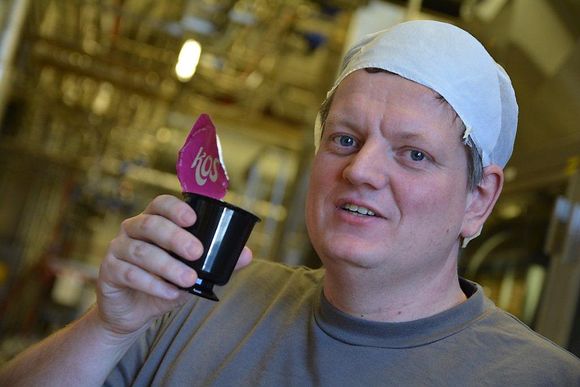
Den som måtte tro at et meieri er en statisk produksjonsbedrift tar grundig feil, i hvert fall ved den dynamiske fabrikken i Brumunddal. Flere steder er det rene anleggsvirksomheten, med nye produksjonsavsnitt eller større modifikasjoner.
Knut-Arne forklarer at det store aktivitetsnivået hovedsakelig skyldes konsernets omstrukturering og lavkarbofarsotten, som blant annet har ført til at markedet nesten skriker etter smør.

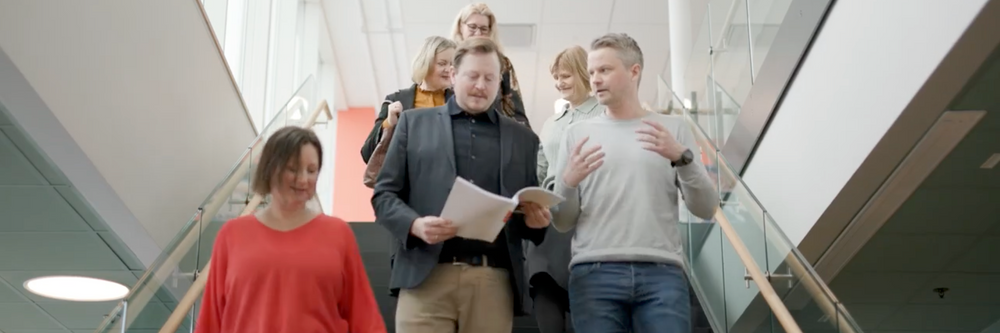
– TINE øker kapasiteten gjennom å samle virksomheten på færre anlegg. Det innebærer at noen legges ned mens andre bygges opp. Meieriene i TINE blir færre og større!, sier han.
– Dessuten har økt etterspørsel etter smør ført til økt produksjon. Det svarer TINE på ved at bøndene blant annet leverer melk med høyere fettinnhold. Konsekvensen av dette blir også økt mengde melkepulver, som vi bearbeider til forskjellige produkter.
Herlig høytemp
Selv om melkepulver av ymse slag utgjør rundt to tredeler av produksjonsvolumet, trekker Knut-Arne fram rosinen i pølsa, nemlig alt som meieriet produserer med ultrahøy temperatur. Det omtales som UHT, et temperatursjokk på 140 grader som varer i kun fire sekunder. Den harde temperaturbehandlingen tar knekken på alle mikroorganismer, noe som gir lengre holdbarhet på produktene.
Utstyret har rundt ti ganger livsykluskostnaden sammenlignet med det som benyttes for konvensjonelle meieriprodukter, og er dessuten ti ganger så avansert. Prosesslederen er ikke imponert over kunnskapene til leverandørene om kravene til utstyr for bearbeiding av langtidsholdbar melk.
– Vi må ofte være eksperter selv, kommenterer han.
Stor kompetanse, korte frister
Knut-Arne forklarer at det også generelt er stort behov for intern kompetanse på produksjonsutstyr. Det er ofte nødvendig å ligge i forkant av hva forbrukerne og den sentrale ledelsen ønsker seg. Han nevner et aktuelt eksempel der anlegget fikk en forespørsel om å prise en ny produksjonslinje til flerfoldige millioner til dagen etter.
– Det krever litt erfaring og kompetanse, sier prosesslederen med en ironisk tone.
Som de fleste næringsmiddelprodusenter har meieriet både prosessområder og maskiner for tapping og pakking. Knut-Arne antyder at styringssystemene totalt sett har minst 30 000 signaler. Prosesskontrollsystemet (DCS) er rene TINE-standarden, det vil si at det er basert på ABB Sattline med et bibliotek fra Landteknikk (nå Skala Prosessteknikk).
Betaler ekstra for oppetid
Han forteller at maskinene styres av mange forskjellige typer PLS-er, blant annet Omron, Mitsubishi, Sattline og Siemens.
– Det er litt dumt, men det har vist seg vanskelig å standardisere når vi kjøper ferdige maskiner, kommenterer prosesslederen.
Derimot bruker han mye tid på å finne de beste maskinene. Høy oppetid er vitalt. Knut-Arne slår fast at den nyeste pakkemaskinen er rene Rolls Roycen. Den er fra tyske Schubert og har en unik oppetid, tett på 100 prosent. Han mener det er verdt å betale litt mer for økt produksjonstid.
– Majoriteten av maskinene våre krangler for mye, kommer det kjapt.
Forenkling fenger
Han har stor sans for maskinbyggere som forenkler løsningene. Prosesslederen har opplevd at for mye overvåking og annen ”leamikk” kompliserer og kan gi negativ innvirkning på tilgjengelig produksjonstid. Det er stikk i strid med intensjonen.
– Jeg liker filosofien til Tetra Pak. De gjør det enkelt, blant annet ved å fjerne tilbakemeldinger på ventilene. Om det skjer noe vil trykket svikte og vi vil oppdage det i selve prosessen, konkluderer han.