Dårlig ingeniørarbeid og sviktende rutiner har kostet norsk industri og norske arbeidstakere dyrt. I de syv største industrikatastrofene i nyere norsk historie lå årsaken snarere i design- og systemfeil enn hos enkeltoperatører. Det viser en gjennomgang som Teknisk Ukeblad nylig fikk ta del i, hos Direktoratet for brann og eksplosjonsvern (DBE) i Tønsberg.
I svært mange av tilfellene skyldtes uhellet som vokste til katastrofe, en ganske liten svikt i en ventil eller en pumpe. Svikten førte raskt til en utvikling som ikke lot seg stanse. Årsaken var ofte at detaljen som sviktet, hadde en svært uheldig plassering eller utforming, og at rutinene for vedlikehold ikke var gode nok.
Kunne unngås

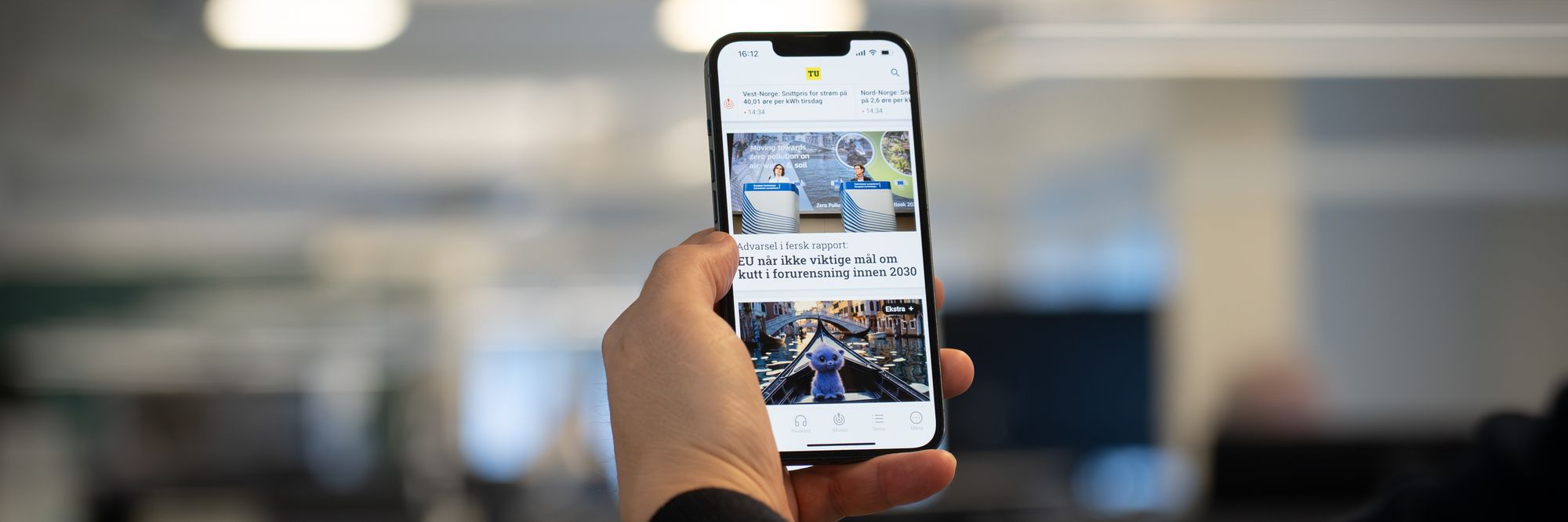
– Det er etter min personlige mening liten tvil om at mange av disse katastrofene helt kunne ha vært unngått, eller i hvert fall blitt dramatisk mindre i omfang, hadde bedre konsekvensanalyser vært gjennomført på planleggings- og prosjekteringsstadiet, sier seksjonssjef Per Låhne i DBE's seksjon for prosessindustri.
– På den annen side er det jo svært lett å være etterpåklok. De anleggene det gjelder, var stort sett planlagt, utført og drevet etter datidens beste praksis. Samtidig må det kunne sies at en bedre og grundigere forhåndsanalsye slik det er vanlig å foreta på nye anlegg i deg. Hazardous Operations Analysis (HAZOP) kunne ha endret ulykkesbildet, sier Låhne.
Det viktigste er å lære av katastrofene. Låhne beklager likevel at det generelt må katastrofer til før sikkerhetsoppmerksomheten styrkes og samfunnet vedtar et strengere lov- og regelverk.
Strengere nå
Det strenge, moderne lov- og regelverk for bygging, drift og vedlikehold av risikofylt prosessindustri som størstedelen av Europa har i dag, er basert på erfaringene fra store ulykker i moderne tid. Blant de ulykkene som har hatt mest å si for utformingen av det moderne lov- og regelverket her i landet, er raffineribrannen på Mongstad i 1975, brannen i Jotuns malingfabrikk i Sandefjord året etter, den eksplosjonsartede brannen på Herøya i 1985 og ulykkene på Rafnes i 1988 og i ilmenittsmelteverket i Tyssedal samme år.
En gjennomgang viser at langt de fleste av disse ulykkesforløpene preges av at viktige komponenter var slik plassert at store følgeskader lett kunne oppstå, så fort komponenten sviktet. Prosessen og utstyret var slik arrangert, at en liten hendelse vokste til en stor og ukontrollerbar. Videre tok vedlikeholdsrutinene ofte ikke tilstrekkelig hensyn til at en tilsynelatende uskyldig komponent kunne være avgjørende viktig for et ulykkesforløp. Dessuten viste det seg at opplæringen av operatørene i noen tilfeller var mangelfull.
Nytt lovverk i 1975
Allerede i 1975 ble lov- og regelverk skjerpet på dette område. Det ga regler også for innretningene i prosessindustri, ikke bare for lagring av brann- og eksplosjonsfarlige varer. Siden har dette regelverk vært oppgradert med visse mellomrom. I dag reageres det vesentlig strengere mot å slurve med sikkerheten enn før. Dessuten gjør Lov om internkontroll situasjonen enda strengere for ledere og operatører på alle nivåer.
Etter Låhnes mening er det liten tvil om at mye av det som skjedde flere tiår tilbake kunne ha vært unngått med dagens moderne regler. Sikkerhetsbevisstheten er i dag langt bedre enn før, og operatørene blir hørt på en helt annen måte. Ordningen med verneombud og påbudte brannøvelser sies å ha hatt en viktig effekt. Bedre merking av nødutganger og skjerpede regler angående ansvaret for å holde rømningsveier frie, har også hatt betydning.
De store ulykkene
Brannen på Mongstadraffineriet startet med varmgang i en oljepumpe slik at pakkboksen ble ødelagt. Oljen lekket ut og ble antent. Pumpen satt rett under en rørgate som ble skadet av primærbrannen. Lekkasjene fra rørgaten ga naturlig nok brannen et katastrofalt omfang. Over punktet med pumpen og rørgaten satt luftkjølere som dro luft fra omgivelsene og opp gjennom brannstedet slik at brannforløpet akselererte. Alt i alt en underlig konstruksjon og komponentplassering som førte til en stor brann som ødela enkelte deler av raffineriet.
Løsemiddelbrann
Jotunbrannen skyldtes at en tappekran for maling ikke lot seg stenge. Løsemiddelholdig maling rant ned i etasjen under tappestedet og inn i et rom som ikke var eksplosjonssikret. Der ble løsemiddeldampen like etter antent av elektrisk gnist og hele fabrikken forsvant i en kolossal hydrokarbonbrann. Menneskeliv gikk tapt og fabrikkskadene beløp seg til hundrevis av millioner kroner. I tillegg tapte Jotun markedsandeler, fordi kundene kjøpte andre malinger mens fabrikken ble bygget opp igjen.
Ammoniakkfabrikken på Herøya eksploderte i 1985 fordi hydrogengass fra prosessen lekket ut, og etter en stund ble antent av varmgang i en pumpe som jobbet mot en stengt ventil. Også dette skyldtes en blanding av dårlig design og utilstrekkelig opplæring og vedlikehold.
Gassbrannen ved vinylklorid-monomer-anlegget (VCM-fabrikken) på Rafnes skyldtes at et rørbend åpnet seg på grunn av erosjon. Etylendikorid-gass lekket ut og resulterte i en meget kraftig brann som ødela viktige deler av fabrikken.