Hærland, Østfold: For å sikre effektivitet, kvalitet og tilgjengelighet i butikkjedene Kiwi, Meny og Spar er store deler av den såkalte bakromsproduksjonen sentralisert.
Sentralisert produksjon
Det nye samarbeidet gjør at bakrommet primært lager håndverksprodukter og varianter med særlig kort holdbarhet. Dette skal komme oss forbrukere til gode ved økt mangfold av produkter.

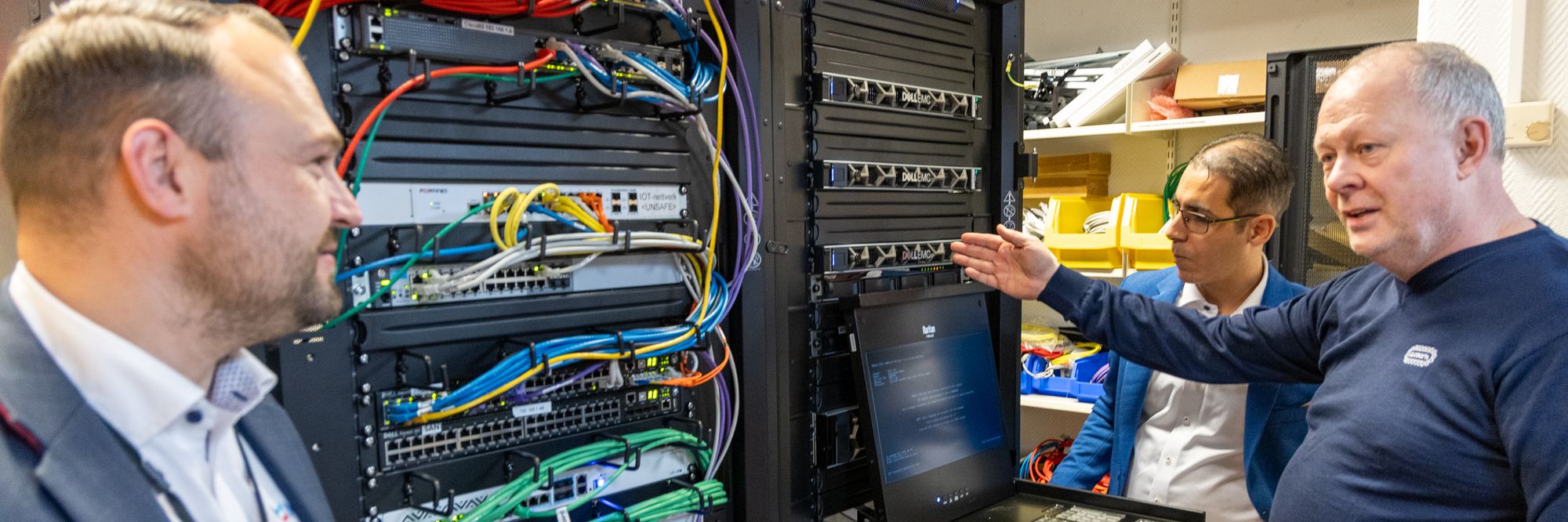
Anlegget er designet for å skjære og pakke 14 500 tonn i året. Johannessen forklarer at det er fem produksjonslinjer og et håndverksrom for spesialprodukter. Det er også satt av plass til en framtidig linje.
Manuell starthjelp
Det går unna på de lange pakkelinjene. Ifølge prosjektlederen går det for eksempel 95 pakker med 400 gram kjøttdeig i minuttet, per linje. Det blir fire og et halvt tonn i timen dersom begge kjøttdeiglinjene er i sving.
Alle råvarer skannes for videre sporing ved ankomst. Johannessen forklarer at det er uunngåelig med noe manuell håndtering ved starten på reisen gjennom anlegget. Etter partering, skjæring eller kværning er det imidlertid slutt på manuell assistanse.
Automatiseringsrekord
Nå reiser pakkene alene på sin ferd videre til dosering, emballering, veiing, etikettering, for kontroll i metalldetektor, pakking og stabling av kasser, og palletering.
- Vi har aldri laget et anlegg med så høy automatiseringsgrad, slår Johannessen fast. Han vet hva han snakker om. Prosjektlederen er del av en sentral trio i Nortura-konsernet som er involvert i alle store prosjekter.
Johannessen nevner tilsvarende anlegg andre steder i Europa, hvor det typisk er langt flere personer per pakkelinje med tilsvarende kapasitet.
- Hos Norfersk er det til sammenligning bare et par operatører som passer på, sier prosjektlederen og smiler fornøyd.
Over 300 varenumre
Tilbake til våre kjøttstykker, som altså reiser med minimal menneskelig innblanding. Pakkene får en liten dose oksygen og karbondioksid for å bevare kvalitet og farge. Sammen med en dobbel film, som sørger for å unngå misfarging, under produktene, er holdbarheten elleve dager.
- Begge deler er nytt i Norge, sier han.
Anlegget håndterer drøyt 100 produktvarianter. Ettersom hver butikkjede har sin egen dagligvareprofil, blir det altså tre ganger så mange varenumre. Et område i pakkelinjene minner nesten om et printerrom.
- Det er fire merkemaskiner per linje, kommenterer Johannessen.
- Vi kan etikettere både over og under pakningene, for å spare tid og redusere omstillingstider.

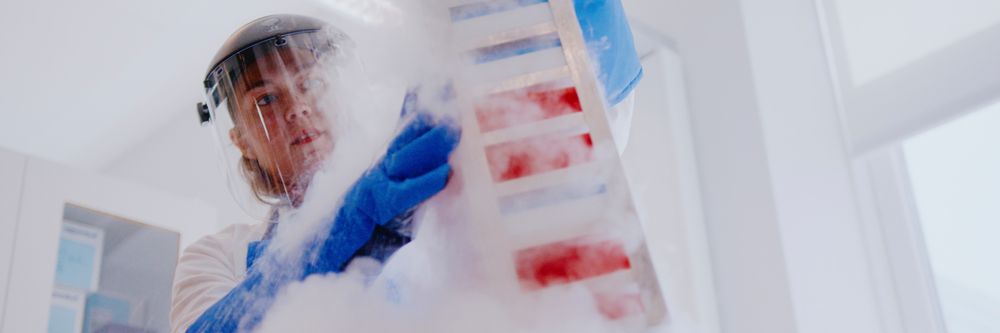
Sammensydd med OPC
Totalt har hver linje rundt ti maskiner, inklusiv merkemaskiner, vekter, gjennomlysings- og pakkemaskiner. I tillegg kommer transportbaner og tre roboter for palletering på slutten av pakkelinjene. Johannessen forteller at det finnes 3000 fotoceller for å holde kontroll på trafikken.
Les også: Automatiserings innsiktsartikkel om robotisering
Et system fra danske BV Electronics styrer hele anlegget. Norturas egne Matiq har stått for prosjekteringen av det omfattende systemet.
- Systemet har kontakt med alle maskinene på hele pakkeanlegget via OPC (en pc-basert kommunikasjonsplattform, journ. anm.), forklarer prosjektlederen.
ERP-integrasjon
Det skinner gjennom at det har vært et lite lerret å bleke, men de lange linjene spiller nå sammen på en harmonisk måte. Styringssystemet er integrert med Norfersks forretningssystem, Microsoft Axapta, og håndterer sporing og full kontroll på hvor alt befinner seg i linjene til enhver tid.
- Det vet blant annet hvor mye og hva som ligger i hver kasse, med riktig vekt på kassene, slår han fast.
I tillegg benytter Norfersk-styringssystemet både til produksjonsplanlegging og overvåking av effektiviteten. Johannessen sikter på en OEE (Overall Equipment Efficiency) på 50-60 prosent. Han mener kravene til rengjøring og omstilling gjør det vanskelig å komme høyere totalt sett. Likevel tror han at OEE kan havne på rundt 75 prosent ved kjøring av kjøttdeig når alt får satt seg.
Les også: Automatiserings innsiktsartikkel om OEE
Fra anlegg til bord
Et helautomatisk kassesystem sørger for internlogistikken. Transportsystemet er designet for å håndtere to kassehøyder, 106 og 185 millimeter. Etter automatisk stabling av kassene på paller av tre ABB industriroboter, overtar to store Swisslog-kranbaner, som håndterer transport til lasting på bil.
Derfra går det til Askos sentrallager i Vestby, og videre til butikker over hele landet. Mange av oss vil nok spise noen av produktene fra superpakkeriet på Hærland i tiden framover.