– Vi har prefabrikert betongsøyler på byggeplasser før, men aldri i så stor skala som her, sier Roger Halle. Han er Kruse Smith sin prosjektleder for råbygget til det nye Stavanger Universitetssykehus (SUS2023) som er i ferd med å reise seg på Ullandhaug i Stavanger.
Betongsøyleproduksjonen startet 22. november i pop-up-fabrikken, som disponerer 3500 m2 i sørenden av det store sykehusområdet. Her skal ni mann i snitt produsere 14 betongsøyler per dag i hele år. Til sammen 2461 av de rundt 4500 betongsøylene til bygget skal produseres i pop-up-fabrikken. De resterende vil på grunn av søylenes geometri og plassering i bygget støpes direkte på stedet der de skal stå.
I tillegg til søylene, støpes også trappeløp og repos (trappeavsatser) i denne midlertidige utendørsfabrikken.
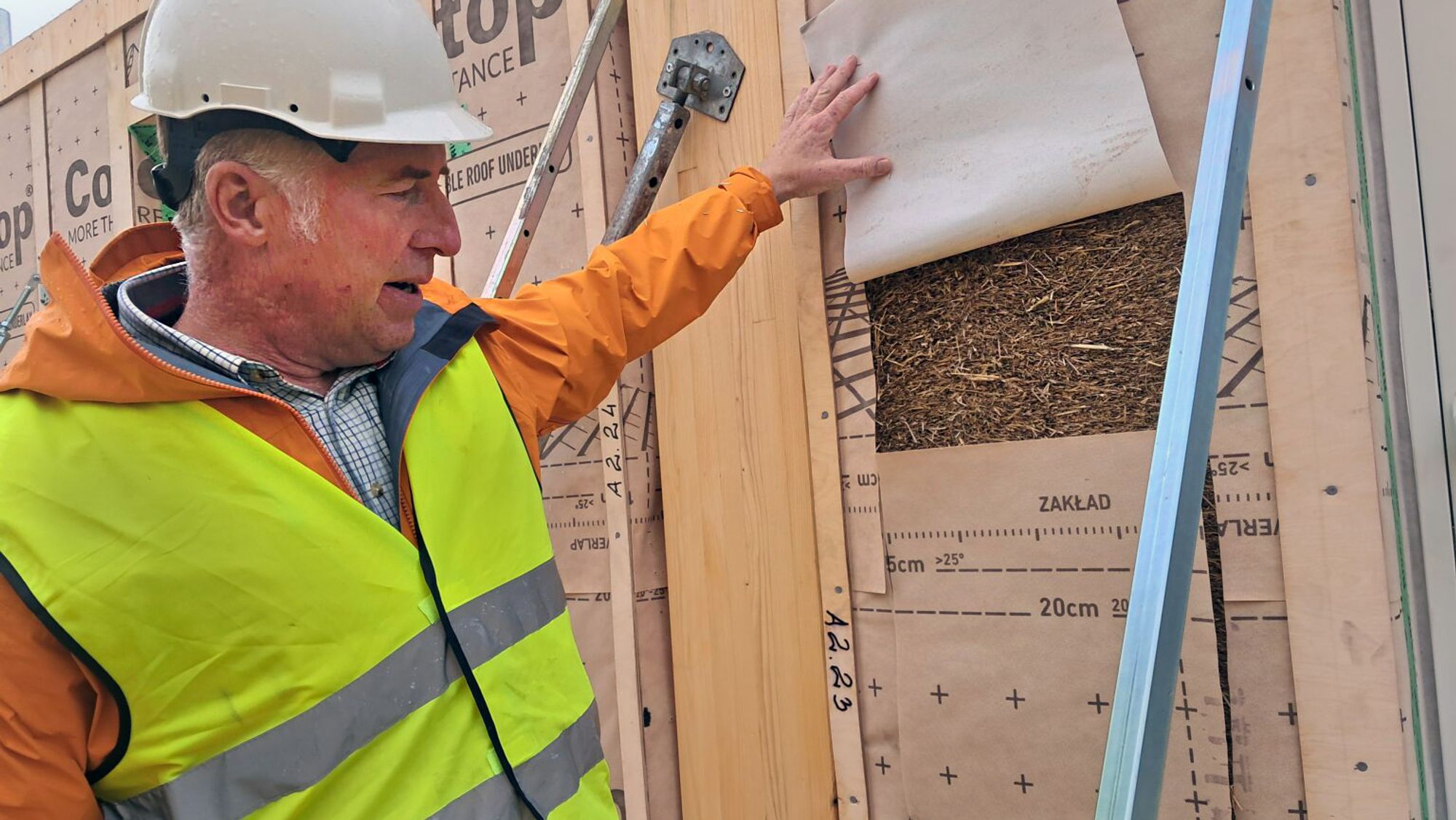
Verdens høyeste «halmhus»: – Brannsikker løsning
Redusert transportbehov
– Vi fyller formene, som allerede har armeringsstålet i seg, med betong som holder 25 grader. Formene dekkes med presenning og står til herding til dagen etter. Deretter heises de ferdige betongsøylene på plass på lageret vårt like ved, forklarer Stig Jonsson, arbeidsleder for prefabrikkeringen av betongsøylene på Ullandhaug, idet han viser oss rundt på den provisoriske fabrikken. Dampen stiger opp fra den lunkne betongen som fylles i form etter form ute i den milde rogalandsvinteren.
Mens søylene kun trenger å hvile i en dag, må repos og trappeløp ligge til herding i to døgn før de plasseres på lageret. Hver søyle merkes med et unikt nummer som viser hvor den skal stå i det ferdige bygget.
– Det er billigere å støpe betongsøylene på plassen, men vi sparer også mye kjøring, sier Roger Halle.
Råvarene til betongstøpingen hentes på Orstad like sør for Sandnes. Alternativet hadde vært å hente ferdige betongsøyler fra fabrikk på for eksempel Vigrestad helt sør på Jæren. Kruse Smith anslår at de sparer rundt 30.000 km i kjøring, som utgjør cirka 60.000 kg CO2.
For å redusere mengden betong, brukes bubbledeck i reposene, som dekke i ringen, samt som dekke over 1.-3. etasje i den ene blokka. Det skal brukes mellom 2500-3000 m2 med bubbledeck.
– Det er vanlig å bruke dette i etasjeskillere, men vi bruker det også i reposene. Dette er noe vi kom på av oss selv, sier produksjonsplanlegger Anders Idland.

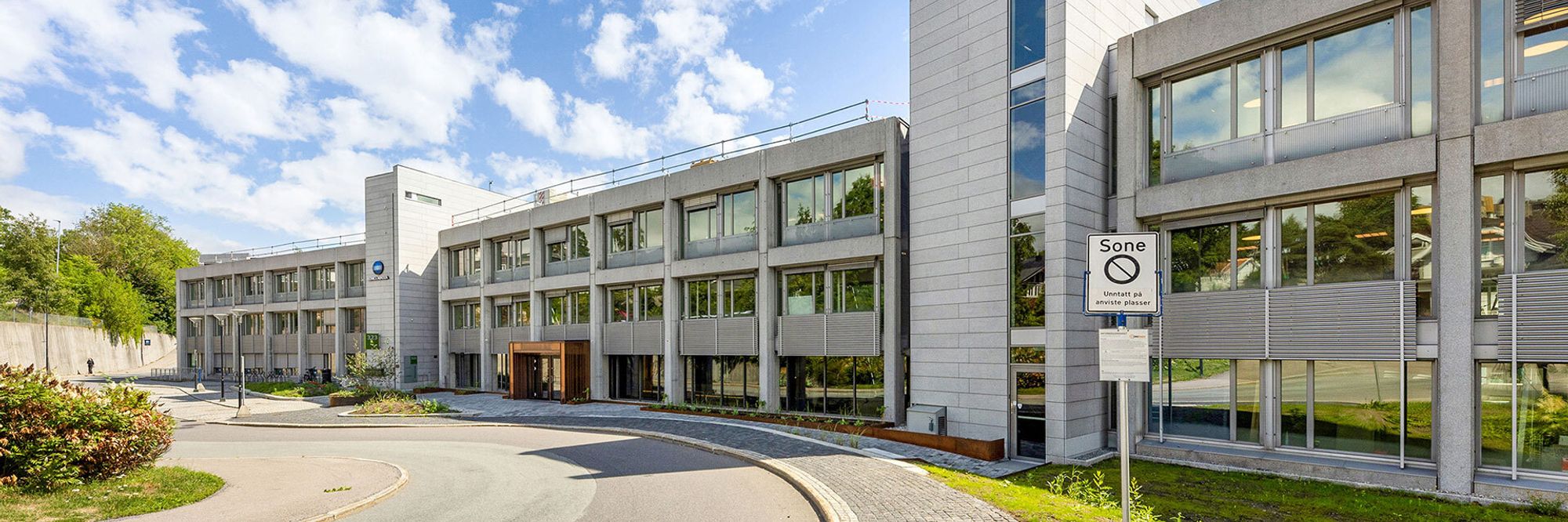
Redusert karbonavtrykk
– Bruk av bubbledeck er en teknisk god metode for å redusere betongforbruket. De har riktignok noen utfordringer i forhold til at plastkulene må monteres solid på plass, men det er ikke noe hokus pokus, sier Øyvind Sæter, fagsjef for betongprodusenten Unicon AS.
Ifølge Sæter kommer rundt 90 prosent av betongens karbonavtrykk fra bindemiddelet.
– For å få lavt karbonavtrykk må vi bruke råvarer som gir lavt karbonavtrykk, for eksempel sementer med lavt karbonavtrykk, eller ved at det tilsettes flyveaske eller slagg, sier han.
Lavkarbonbetong bruker lengre tid på å få full styrke, men det gir ikke noen ulempe så lenge utbygger og entreprenør tar dette med i planleggingen.
Fagsjefen oppfordrer også flere til å gjenbruke mer av betongavfallet.
– Vi i Unicon har redusert eget betongavfall med opptil 70 prosent ved å tenke aktivt på hvordan vi skal se på avfallet som en ressurs og ikke et problem, sier han.
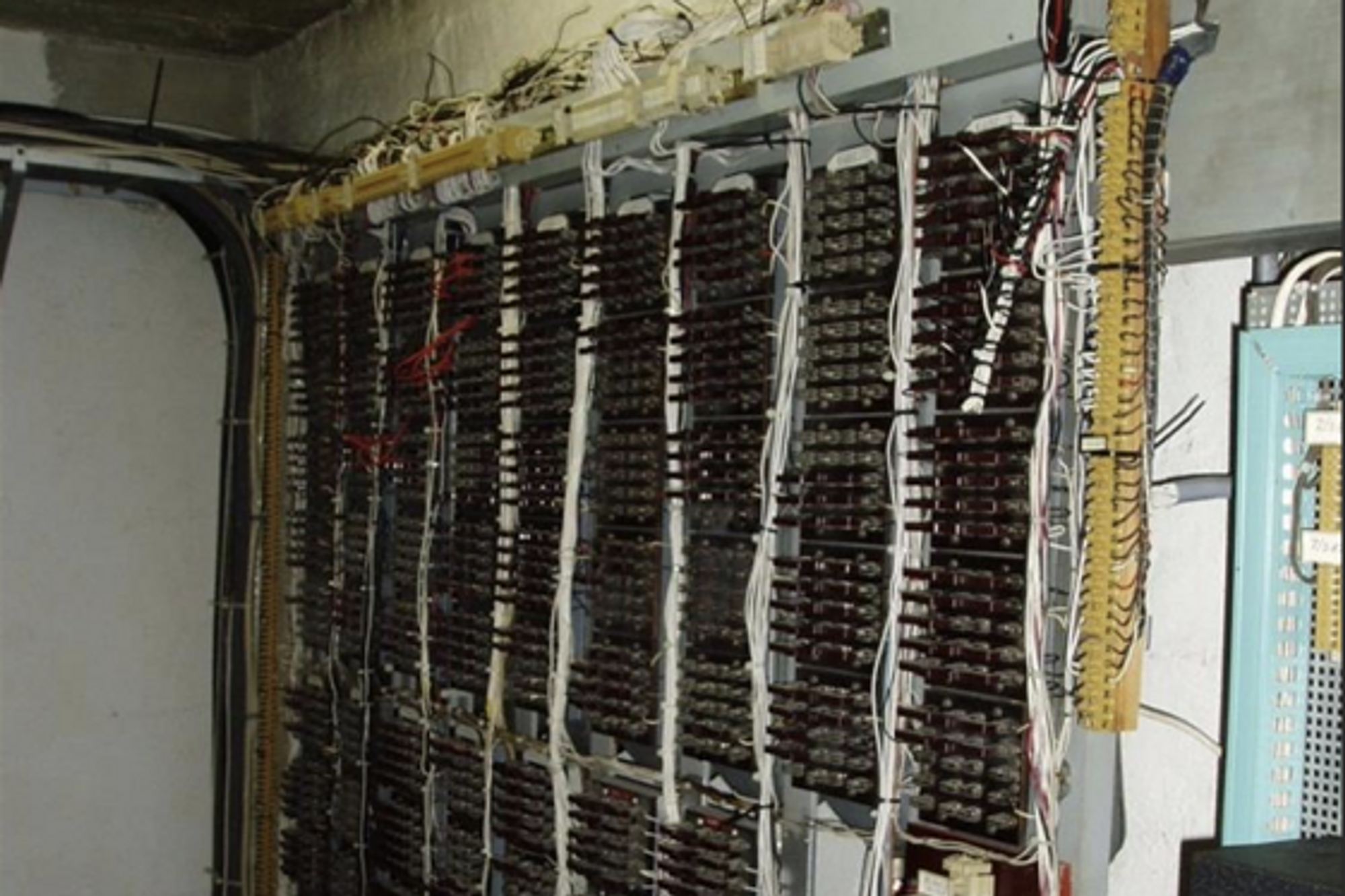
Viste frem dette bildet – fikk 20 milliarder kroner

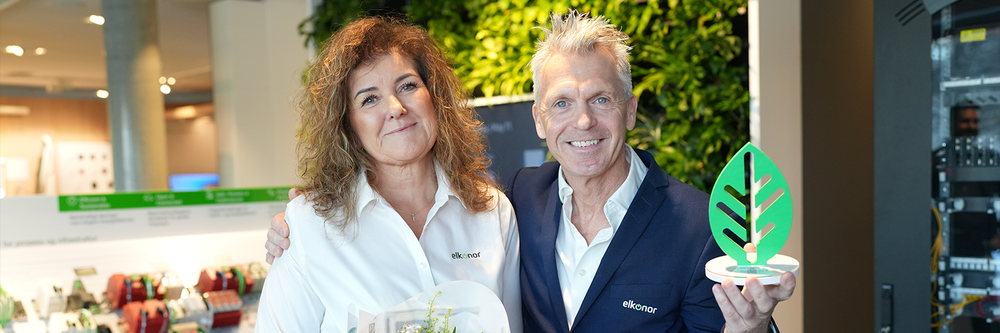
Uvant med papirløs byggeplass
Tilbake på Ullandhaug tar Idland oss med til en BIM-container midt på byggeplassen. Den skal tåle mange minusgrader, og er hjernen i prosjektet. For SUS2023 satser på bruk av BIM (Bygnings Informasjons Modulering) i byggeprosessen. Det gir detaljerte virtuelle byggetegninger. De ansatte oppdaterer produksjon og byggeprosess kontinuerlig ved hjelp av iPad eller iPhone. At dette dermed er blitt en papirløs byggeplass, er litt uvant for noen av de eldre karene.
– Det frister jo av og til å trykke på «print» sier Stig Jonsson med et stort smil, men legger kjapt til at dette er noe som går seg til. – De unge tar dette med en gang, sier han.
– BIM betyr at det er blitt bedre å planlegge produksjonen nå enn før. Lagerbeholdningen oppbevares i skyen, så BIM gir god lagerkontroll. Vi bruker det også til oppfølging og framdrift under produksjonen, samt HMS-oversikt, sier Idland.
Så lenge ingen fristes til å bruke skriveren, betyr BIM innsparing av store mengder papir. Akkurat hvor mye det blir for dette prosjektet er det ikke gjort noen anslag på, men at det ville blitt en stor papirstabel etter at alle revisjonene var gjort, er det ingen tvil om. Til sammenligning: Da Kruse Smith jobbet med drikkevannsanlegget for Nord-Jæren ved Langevatn, gikk det med cirka 2000 individuelle tegninger, som gjerne ble revidert både 1 og 5 ganger.
– Så papirfabrikkene sliter litt nå, humrer Roger Halle.
Byggingen går etter planen
Lars Egil Borsheim, som er prosjektleder for bygg av SUS2023, er svært fornøyd med at man bruker BIM.
– Dette kan sammenlignes med da man i sin tid gikk over fra steintavler til papir, sier han.
Hvert kontrollområde oppdateres i BIM en gang i uka. Åtte uker før produksjonsstart for kontrollområdet, låses modellen, slik at leverandørene kan starte med bestilling og produksjon.
Nå i starten jobber cirka 250 personer med grunnarbeidene for det nye universitetssykehuset i Stavanger. Når selve byggingen starter i 2020, øker dette til rundt 700.
– På det meste vil det jobbe opp mot 800-900 her, sier Borsheim.
Det er 1. byggetrinn av det nye Stavanger universitetssykehus som skal stå klar i 2023 med alle somatiske senger, akuttfunksjoner og nødvendige støttefunksjoner. Utbyggingen skal tilfredsstille kravene til BREEAM Very Good. Sykehuset skal ha passivhusstandard, energikarakter A og oppvarmingskarakter Grønn.
.jpg)
Mikrohus med talestyring og storskjerm: – Tenk deg disse som varmestuer i bakkene i Hemsedal