Knowing how liquid fronts move around is crucial to the maximal exploitation of a reservoir. Four-dimensional (4D) seismics are a high-priority development area within exploration and production technology. With the aid of repeated seismic investigations, among other things ”by-passed” oil can be surveyed. The precision and resolution of 4D well studies is better than that of surface seismics. Traditional wireline operations measure seismics downhole, but in completed wells the formations are not as accessible. The Norwegian company Read Well Service has developed permanent downhole sensors to measure with the same equipment over time.
“We want fixed equipment that can measure without affecting production”, explains Helge Brandsæter, Vice President of Read Well Services Research and Development: “Without this, measurements are very expensive. By integrating the sensors into the well completion, we can measure the reservoir without it being at the expense of production.” One oil company has already bought a prototype system that will receive its final testing as soon as the well allocation is finished.
Noisy flows

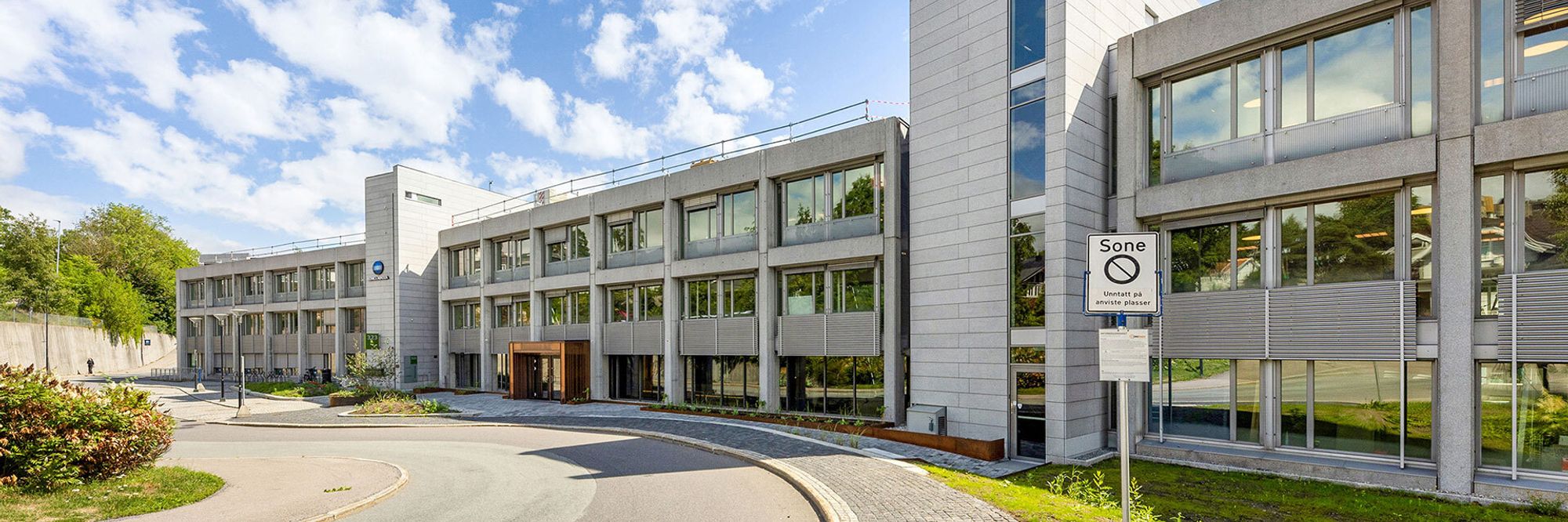
When the measurement equipment is inside both the casings and the production pipes, acoustic measurements are poor. It is then important to free the sensors from the production pipe and ensure that they are in contact with the formation. The sensors are placed where the casing is cemented on the back in full contact with the formation. In addition, sensors are placed on the production pipe so as to characterise the acoustic noise from the fluid flow there.
“We probably won’t succeed in detaching ourselves completely from the noise,” says Brandsæter, “We’re not that optimistic.”
Each receptor node in the well has three sensors distributed round a pipe. To reduce the size, accelerometers are used - integration of the measurement data will provide speed. In their packing, the sensors are about one cubic centimetre. The aim is 30 units with three sensors each per well, but this depends on the wells too.
Pressure and temperature are also major challenges when designing permanent equipment for wells – and temperature is the bigger of the two. “The electronics in the measurement equipment must tolerate up to 180°C, and we have put a lot of work into making them robust.”
Data are transmitted in real time to the surface for processing.
Microseismics
Permanent downhole sensors can also be used for microseismics, but Brandsæter makes clear that this is not Read Wells’ primary objective.
“This technology is still on the drawing-board, and the oil companies have not yet begun to use it”. Phillips Petroleum Norway has been the pioneer, and experimented on the Ekofisk field. They have calculated where a number of small earthquakes caused by field subsidence are coming from.
“They think that microseismics can be used to chart fault patterns that we wouldn’t otherwise see”, says Brandsæter. Microseismics are also relevant in relation to water injection, because they can survey how the water is moving.
Read Well is not the only one developing systems for permanent downhole sensors. No one else has yet made the kind of measurement Read Well is to make with its prototype system, but the competition to develop good solutions is fierce.
“We won’t be alone or have a monopoly”, says Brandsæter.