Kortversjonen av svaret er kompetanse, automatisering og digitalisering. Allooc har nå flyttet produksjonen av aluminiumprofiler som brukes i deres laminatgulv fra Kina til Magnor. Derfra får de den rette kvaliteten til konkurransedyktig pris. Sapa kontaktet Tronrud Engineering, som utviklet en helt ny produksjonscelle for profilene.
Den nye produksjonscellen ble installert i april, innkjøringsfasen er snart ferdig og sammen inviterte de tre bedriftene presse og politikere til en omvisning.
Flere i samme presse
I Lyngdal har kunden Alloc også avanserte løsninger som gir den konkurransekraft.

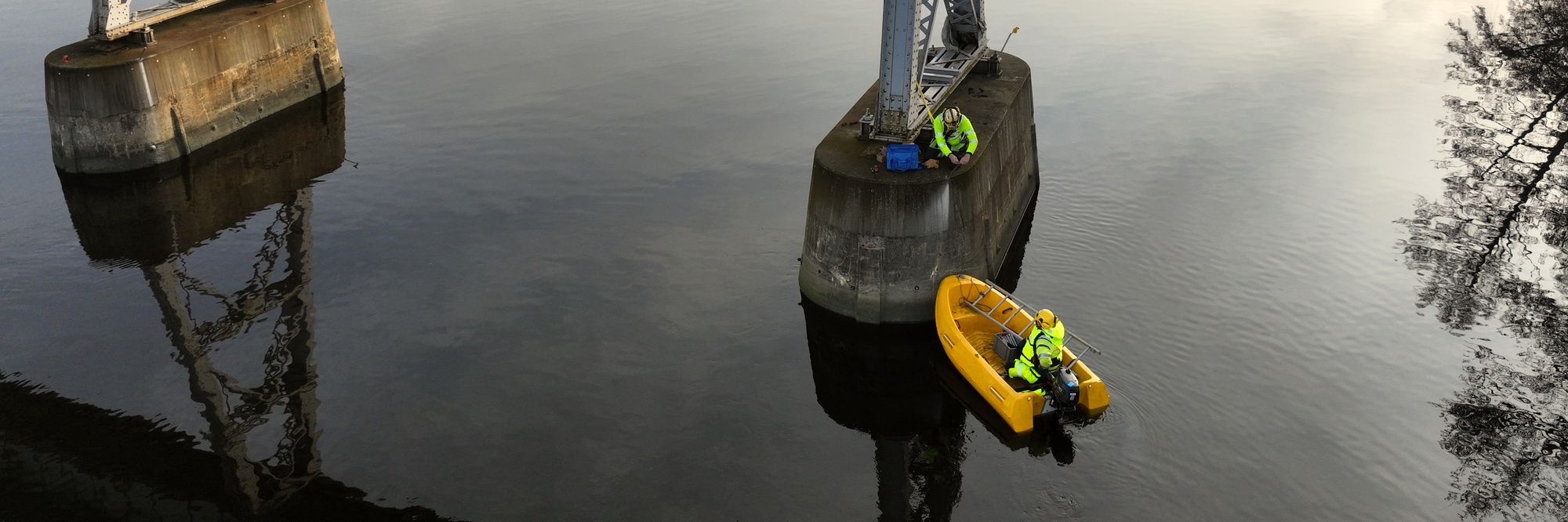
– Vi har en produksjonsprosess for høytrykkslaminat som tar to timer. Konkurrentene våre bruker 16 sekunder. Derfor har vi utviklet et system der vi har økt antallet i pressen, og dermed klarer vi å matche den tiden. Vi skal ytterligere ned. Vi har fire ansatte som jobber fulltid på forskning og utvikling, sa John Vonli, general manager hos Alloc.
Han forteller at det ikke var noen selvfølge at de valgte Sapa. Alloc hadde forespørsler ute hos en rekke leverandører.
– Sapa var den leverandøren som ga oss den mest kosteffektive løsningen. For oss er råvarekostnadene nå 92 prosent av de totale produksjonskostnadene, sier Vonli.
Vil opp til 20 hull
For Sapa er håndteringen av profilene den virkelig store utfordringen. De er tynne, smale og veldig lette. For å få ned produksjonstiden utviklet de verktøy med 16 hull (som gir 16 profiler fra bolten som presses inn i ekstruderen).
– Vi har forsøkt med 20 hull men det gikk vi bort fra i første omgang. Nå skal vi optimalisere produksjonen med 16 hull før vi tar opp igjen arbeidet med 20 hull, forteller Roy Nygård, avdelingsleder for verktøy på Sapa.
Konsernsjef Egil Hogna er optimistisk på vegne av norsk industri. Han peker på at vi har et cluster rundt aluminium som dekker hele spekteret fra produksjon til høyt foredlete produkter.
– Dette er det verdt å satse videre på. Til nå har vi tatt de enkle grepene, det som gjenstår i norsk industri er å løfte det teknologiske nivået. Vi trenger mer autonome og selvlærende løsninger. Utfordringen på sikt blir å ha operatører og driftspersonell med tilstrekkelig utdannelse.
Les: Intens jakt på god automatisering
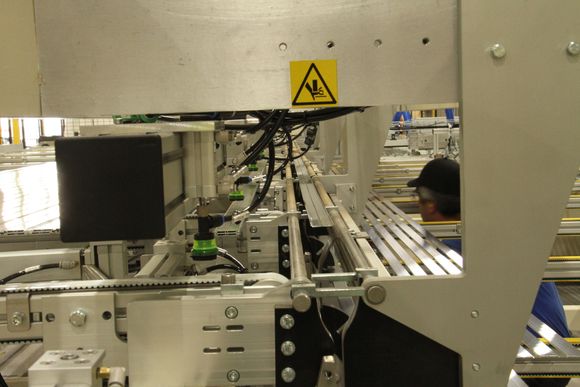
Hyllevare funket ikke
Sapa valgte å gå til Tronrud Engineering for å laget en ny produksjonscelle til å bearbeide og ferdigstille profilene. Lukasz Sidor var prosjektansvarlig for den jobben. Han forteller om en utfordrende og vanskelig jobb der hyllevare ikke lot seg bruke.

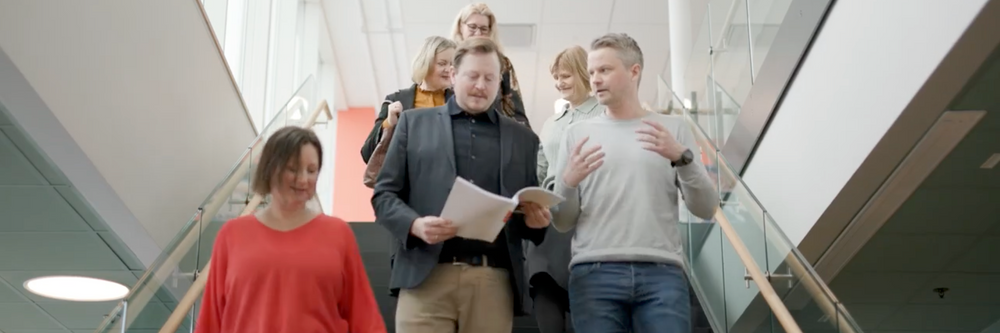
– Profilene har en z-form, det gir mye lekkasjer og det var vanskelig å få til en løsning med vakuum for å flytte dem. Vi måtte lage et helt nytt system som tilpasser seg z-formen og reduserer lekkasjene. Fordi ikke alle profilene ligger samme vei ble det ekstra komplisert, sier Sidor.
Siden de ligger to veier må systemet detektere hvilken vei profilene ligger, og hvilke som skal snus. Da tas bilder fra undersiden i løpet av millisekunder og systemet beregner hvilken av to flaps som skal åpnes for å snu den rette profilen før de føres videre.
Les: Tok opp kampen mot østeuropeiske billigprodukter
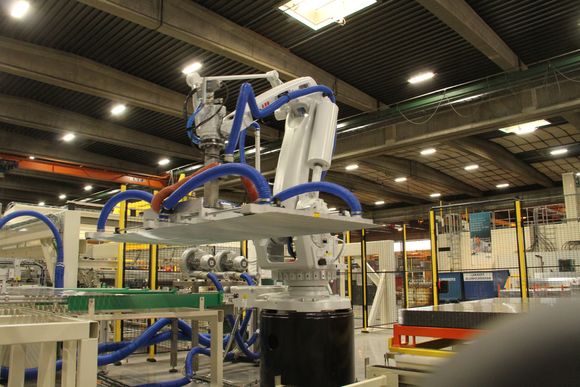
Problemfri innkjøring
I produksjonscellen til Sapa har Sidor benyttet de nyeste pls-ene fra Simens, pneumatikkomponenter fra Festo og en robot fra ABB.
– Vi har en partneravtale med Kuka, men her ønsker kunden ABB.
Prosjektet startet i september i fjor. Først ble den montert og testet hos Tronrud, før den ble fraktet til Magnor 9. april. Innkjøringen har så langt gått uten problemer. Sidor forteller at Tronrud utviklet den 215 kvadratmeter store cellen på egen hånd, men at Sapa godkjente løsningen før den ble satt i produksjon.