I formel 1 sirkuset står store verdier på spill. Effektive pitstop er vitalt. På samme måte er optimale produktomstillinger i industrien essensielt.
Kutt opp- og nedkjøringstid
Millisekund- og millimeterpresisjon. På samme måte som pitstoppene i F1, bør alt være ”timet og tilrettelagt” for omstilling samt opp- og nedkjøring av produksjonen. Årsaken er svært enkel: mange bedrifter har de største tapene sine i forbindelse med disse oppgavene.
Mange industribedrifter, med en eller toskiftproduksjon, har en dårlig start på dagen, sett fra et økonomisk perspektiv. Et tap, eller forsinkelse, på 10 – 30 minutter er ikke uvanlig ved oppstart. Det går raskere etter pausene. Men, også her går det vanligvis for lang tid fra siste godkjente produkt før pause, til første godkjente etter pause.
Opptil en tredel i omstillingstid
I tillegg er det gjerne et nedkjøringstap før pauser, og mot slutten av skiftet. 10 – 30 minutter er heller ikke her helt uvanlig. I tillegg har mange bedrifter lange omstillingstider for produkt-, film- eller etikettbytte. Dette er ofte til sammen over 60 minutter pr skift.
Med enkel algebra ser vi at tapt produksjonstid, med fulle kostnader, er mellom 1,5 og 3 timer per skift. Dette er slett ikke uvanlig! I mange bedrifter forsvinner opptil en tredel av arbeidstiden i en eller annen form for omstilling.
Halveringer…
Løsningen er den engelske firebokstavsforkortelsen SMED (Single Minute Exchange of Die), eller på godt norsk: omstillingstrening for de ansatte. Men, det hjelper ikke med et SMED kurs alene. Operatørene må ha fått fordelt ansvar gjennom såkalte ”Forbedringsgrupper”. Gruppene må få laget nye standarder for omstillingene.
Deretter er det viktig at ledelsen følger opp at den nye standarden brukes av alle. Alle endringer, og innføring av nye standarder, krever stor oppmerksomhet fra ledelsen. Dette inkluderer tid til inntrening og perfeksjonering av de nye standardene.

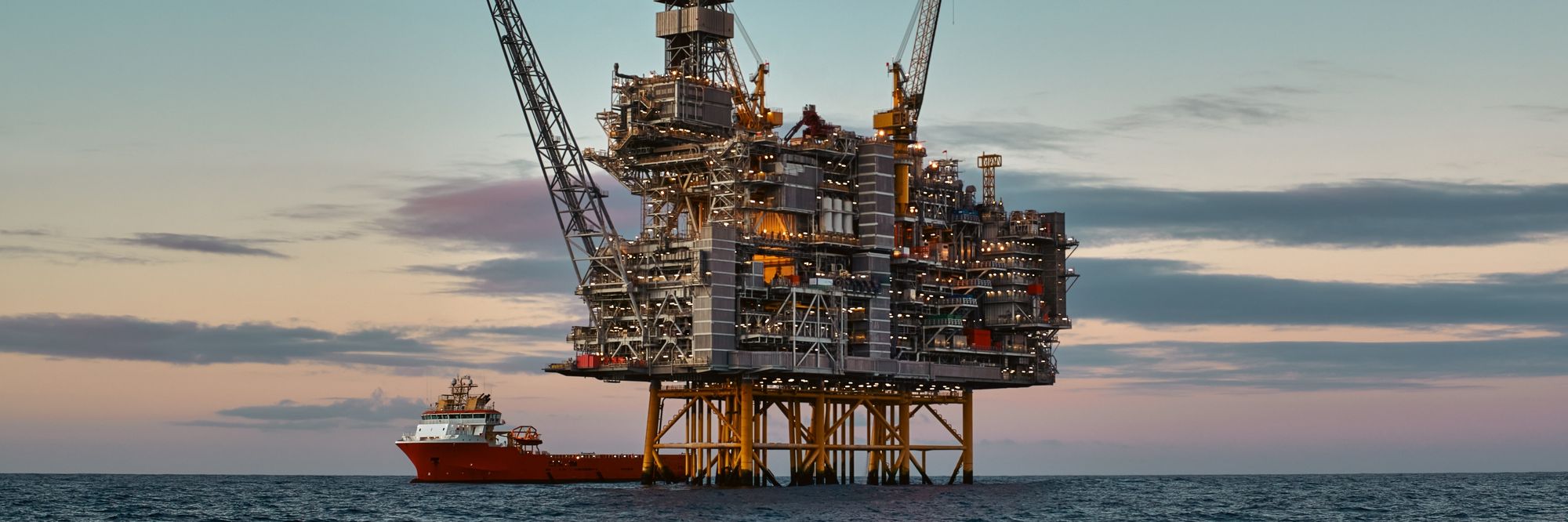
Langt unna verdensklasse
Systematisk arbeid er krevende, men gevinsten er formidabel! Veldig få norske bedrifter, som ikke har gjort spesielle aktiviteter for å forbedre produktiviteten, vil ha en OEE (Overall Equipment Efficiency) på godt under 50 prosent. Og selv mange større produksjonsbedrifter har OEE ned mot 20-tallet. Da er det vanskelig å være konkurransedyktig, og langt til verdensklasse på rundt 85 prosent.
Det er viktig at operatørene har eierskap til de nye prosedyrene som innføres i forbindelse med SMED. Det er derfor naturlig å engasjere, foreta opplæring i å avdekke tap, samt å tilrettelegge og trene på nye rutiner. Gjennom trening på omstillinger, vil drastiske reduksjoner i tidsbruken oppnås. Dette vises umiddelbart på produktivitetstallene (OEE). Gjort på riktig måte, vil typisk omstillingstid halveres de første gangene!
Vitale bidrag fra operatørene
Hvordan få operatørene til å gjøre denne jobben i tillegg til de vanlige oppgavene? Gjennom å starte en ”Forbedringsprosess” (i TPM, Total Productive Management) får operatørene en innsikt og forståelse av hva som kreves for å overleve i fremtiden. Samtidig må de forstå at kravet er å jobbe smartere, ikke å jobbe fortere. Ved å involvere operatørene til å være med å måle bedriftens-, linjens-, og/eller maskinens OEE, er det lett å se at deres bidrag øker verdiskapningen i bedriften.
Les også de andre artiklene i "Perfekt produksjon!":
Del 2: Forbedringsgrupper dobler produktiviteten

.jpg)
Del 6: Tapsanalyse setter en pris på tapene
Del 7: Operatørvedlikehold: Selvgjort er velgjort