Pete Townsend fra rockebandet The Who var en av de første gitaristene som ble kjent for å smadre den elektriske gitaren sin under en konsert på midten av 1960-tallet.
Senere fikk Jimi Hendrix oppmerksomhet da han satte fyr på gitaren sin under tre konserter i 1967. Etter dette har tusenvis av kjente og ukjente rockemusikere avsluttet konserter med å kaste gitaren inn i forsterkeren eller ned på gulvet slik at halsen på gitaren knekker.
Men i fremtiden kan rockemusikere utføre slike handlinger uten å måtte investere i nye gitarer.

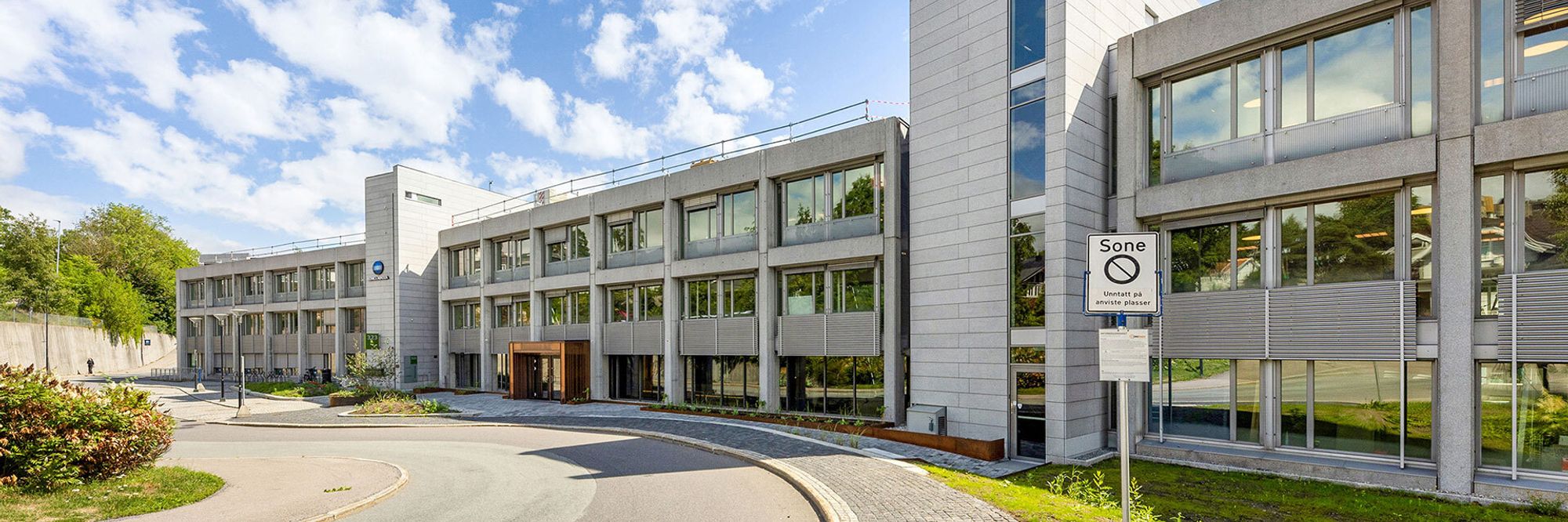
Praktisk talt umulig å ødelegge
For med 3D-utskrevet titan og en patentert sandwich-struktur har den svenske
verktøyprodusenten Sandvik Coromant utviklet og produsert en elektrisk gitar som det
praktisk talt er umulig å ødelegge.
– Vi har konstruert en gitar som det ikke er mulig å smadre på noen som helst tenkelige måter. Den ingeniørmessige utfordringen ligger i det kritiske leddet mellom halsen og kroppen, og som vanligvis kan knekke på en gitar, sier utvikleren Henrik Loikkanen hos Sandvik Coromant.
De svenske ingeniørene har klart å komme seg rundt denne utfordringen ved helt å fjerne leddet mellom halsen og kroppen til gitaren. I stedet har de frest halsen og gripebrettet i ett enkelt stykke av gjenbrukt rustfritt stål.
Ifølge Sandvik har denne konstruksjonen ikke tidligere blitt brukt på en gitar. Både halsen og gripebrettet er utvidet med et rektangulært «nav», som går langt inn i gitarkroppen. Gitaren er utviklet i samarbeid med den engelske gitarkonstruktøren Andy Holt fra Drewman Gitars, som er kjent for å bygge aluminiumgitarer.
3D-utskrevet i titan
Selve kroppen på gitaren er 3D-utskrevet i titan, og gitarknappene er også 3D-utskrevet.
– Additiv produksjon (3D-utskrift, red.) gjør oss i stand til å skape lettere, sterkere og mer fleksible komponenter med interne strukturer som er umulige å frese på tradisjonell måte. Og i tillegg er dette mer bærekraftig, fordi du bare bruker de materialene som du trenger til komponenten og dermed minimerer avfallet, sier Amelie Norrby, som er additiv produksjonsingeniør hos Sandvik.
Alle materialene i gitaren er produsert i metall, og derfor har det også vært en utfordring for verktøyprodusenten å unngå forvrengninger – også kjent som distorsjon – på de avlange, slanke flatene som halsen og gripebrettet.
– Presisjon var ekstremt viktig. Programvaren vår er basert på årevis av erfaring fra verktøymaskinene våre, og det gjør oss i stand til å frese gripebrettet ned til en tykkelse på millimeternivå, sier Henrik Loikkanen.
- Forskere hevder de har 3D-printet et hjerte: Nå må de lære det å pumpe
Sandwich-struktur utviklet til energilagring
For å oppnå en kombinasjon av en sterk, stiv og lett struktur på gitaren, har Sandvik brukt en ny lettvektsstruktur som de kaller Isotropic Lightweight Structure (ILS) av såkalt hyper-duplex-stål.

.jpg)
Strukturen minner om et sandwich-mønster, og er egentlig utviklet for å oppbevare for eksempel gass i kjøretøy eller til å lagre hydrogen som overskuddsenergi fra havvindmøller. Men denne strukturen har altså vist seg også å fungere godt til gitarer.
Her kan du se en 3D-animasjon av gitaren
At strukturen er isotopisk, innebærer at strukturen kan motstå press fra alle sider og kanter, inkludert innsiden.
Da gitaren var ferdig produsert, prøvde Sandvik-medarbeiderne å smadre gitaren på verkstedet, og de ga også et eksemplar til den svenske gitar-legenden Yngwie Malmsteen. Han tok gitaren med på en konsert i Florida, hvor han gjorde iherdige forsøk på å ødelegge gitaren.
Om den nye holdbare 3D-utskrevne gitaren overhodet blir satt i serieproduksjon, om lyden er god og hva prisen eventuelt vil være, er uvisst. Det sier i hvert fall ikke Sandvik Coromant noe om.
- Matprinting: Her utformer 3D-printere spektakulære matretter