Hva er forskjeller og likheter? Og er det hipp som happ hvilket system som velges?
Forbedringsprosesser
TPM (Total Productive Management), Lean og TPS (Toyota Production System) er begreper vi hører stadig oftere i industrien i Norge.
Mange har blitt ”pirret” til å sette i gang slike forbedringsprosesser. Men det er ikke alltid like lett å holde tunga rett i munnen. Det hersker fortsatt tvil om hva en produksjonsbedrift trenger, og hva de ulike begrepene innebærer. En gjenganger er hvilken prosess eller metode som skal velges, Lean, TPM eller TPS. Kanskje ikke så merkelig, da både begrep og forklaringer utvilsomt varierer. Vi gjør derfor et forsøk på klarifisering, og starter med likhetene i TPM og Lean.
Slankekrigen
Enkelt fortalt betyr en ”Lean” prosess å skape en mest mulig ”trimmet” eller ”mager” verdiprosess gjennom hele bedriften. I praksis betyr det å sette all resursbruk, fra innkjøp hos underleverandør og ferdigprodukter, helt frem til kundene, under lupen.
En TPM prosess fokuserer på utfordringene i produksjonsområdet, dvs. selve produksjonen i større grad enn Lean. For å oppnå en god gjennomstrømning (”flow”), eller Lean Production/Manufacturing, er vi avhengig av å kunne stole på produksjonsutstyret, og at det leverer som forventet. For å kunne levere en ordre til avtalt tid, må produksjonsutstyret fungere, og levere som planlagt.
Hensikten med begge systemene er å fjerne mest mulig tap, enten det dreier seg om tidstap, stopp i produksjonen eller leveringskjeden, og at det samtidig skapes et ”sug” (pull) etter nye varer, slik at produkter ikke produseres for lager og/eller mellomlager. På denne måten blir det den eksterne, eller interne, kunden som bestemmer hva som skal produseres og når.
Forbedringsgrupper
I Lean, som i TPM, er involvering av operatørene en kritisk suksessfaktor. I begge systemer brukes Kaizen begrepet. Dette betyr å involvere alle medarbeidere i en kontinuerlig forbedringsprosess, gjennom at alle er deltakere i forbedringsgrupper.

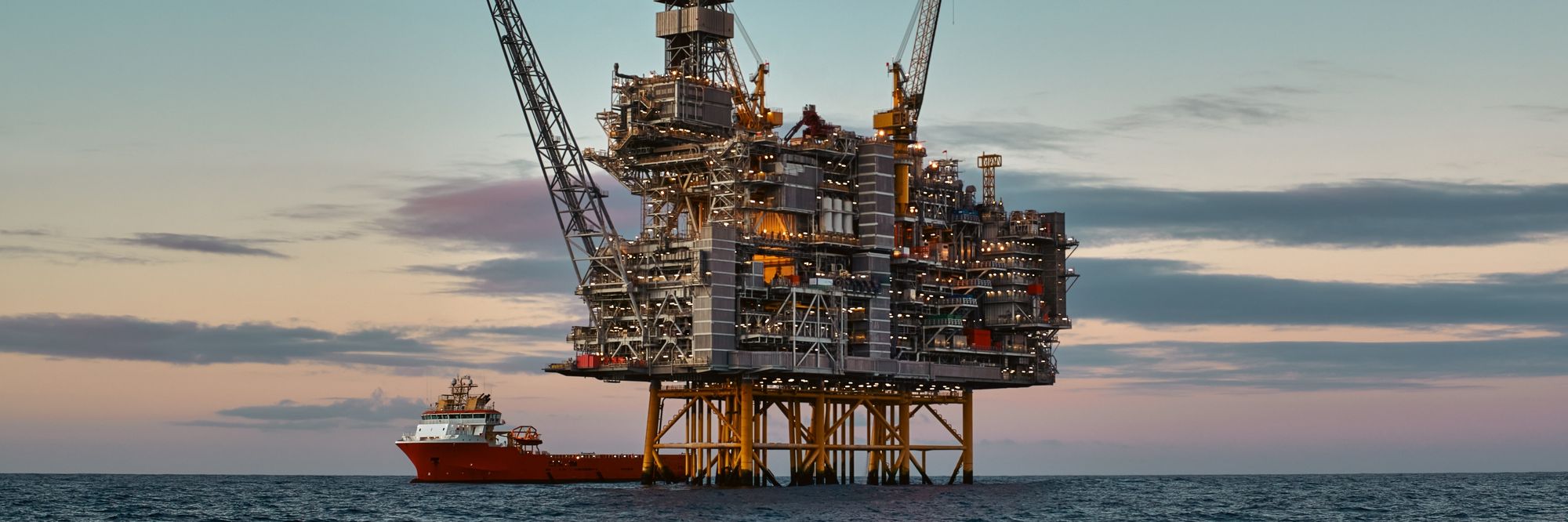
Dette er ofte den mest takknemlige og hyggelige del av jobben. Operatør / ansatte har alle en rekke gode forbedringsforslag som de kommer med i løpet av første treningsdag. Dette på tross av alle typer ”forslagskasser”, som i praksis er rimelig tomme.
Standardisering
Involvering av de ansatte er en betingelse for at forbedringsprosessene ikke skal stoppe opp. Slike prosesser skal styres av ledelsen, men skal drives av de ansatte gjennom sitt forbedringsarbeid i gruppene.
Andre elementer, som er like i TPM og Lean, er den sterke tanken om standardisering. Dette er grunntanken i TPM, og den er like viktig i Lean. Tydelig styring fra en tilstedeværende ledelse er også nødvendig i begge systemer, på samme måte som visualisering av oppgaver, mål og resultater.
Tydelig ansvar
Både innen TPM og Lean er tydeliggjøring av ansvar et vesentlig element. Gi ansvar til enkeltpersoner – ikke bare til grupper, lag og avdelinger. Det vil gjøre det mye lettere å følge opp om oppgavene gjennomføres.
Gi ansvar, til alt fra renhold til planlegging og oppfølging av daglig drift. Men, tilpass alltid oppgavene til kompetansenivået. La de ansatte være i ”flytsonen” ! Det er like naturlig i administrasjonen, i en Lean prosess, som i TPM på en produksjonslinje.
Fjern tapene!
Sørg deretter for å følge opp oppgavene gjennom ”24 timers møter”. Dette forutsetter mange ganger at det har vært en målstyringsprosess i forkant, for å rydde i de mange, og ofte for store, for lange og noen ganger unyttige, møtene.

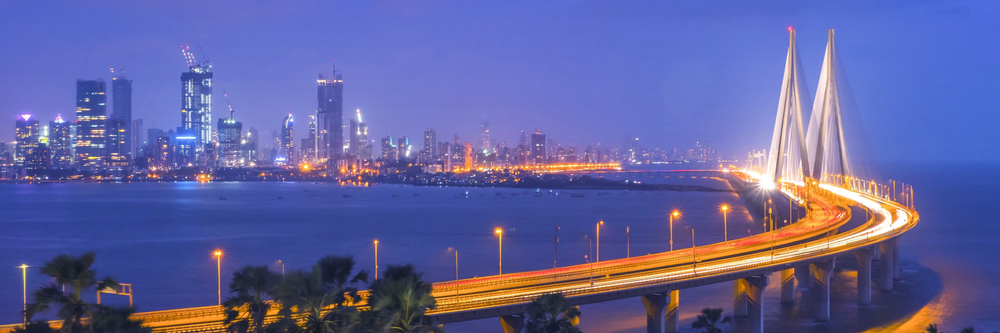
I et 24 timers møte står oppfølging av siste døgns aktiviteter på agendaen. Hensikten er å få iverksatt tiltak umiddelbart på forhold som ikke fungerer. Eller kort sagt: Fjern tapene snarest! Og dette er igjen vesentlige elementer i både TPM og Lean.
Og sist, men ikke minst: Både TPM og Lean er opptatt av hva som er verdiskapende for kundene. Og det er kun verdiskapende elementer i produksjonen, eller Lean prosessen, vi skal være opptatt av. Elementer som ikke oppfattes som verdiskapende (av kunden), skal vi i utgangspunktet ikke beskjeftige oss med.
TPM før Lean?
Når brukes så de forskjellige elementene? Hvordan velger jeg det ene eller det andre? Vi må en snartur innom TPS (Toyota Production System), det grunnleggende tankegodset som bilprodusenten har bygget sine produktivitetsfremmende prosesser på. På lik linje brukes TPM for å få kontroll på produksjonsprosessene. Å fjerne tapene er et naturlig startsted for alle produksjonsbedrifter.
Selv om beregningsmetodene varierer, finnes det få norske stykkproduksjonsbedrifter, inklusiv næringsmiddelbedrifter, med OEE (Overall Equipment Effectiveness) over 50 prosent før starten på TPM eller Lean. I praksis betyr det at flere titalls prosent av blant annet arbeidstiden, energiforbruket og maskintiden ikke benyttes til verdiskapende tid.
Når vi har kontroll på produksjonen (standardisert produksjon – ”0 feil”), er det naturlig å se forbedringer i en mer alt omgripende sammenheng, en Lean prosess.
Kun verdiskapning for kunden
Lean består i grunnen av tre elementer:
- Lean filosofien
- Lean prinsippene
- Lean Verktøykasse.
I Lean filosofien tenker vi på hva kunden vil betale for. De ansatte skal alltid forsøke å være i forkant, dvs. tenke endring/forbedring. ”Det vi gjør i dag, er det beste vi kan, men i morgen kan det gjøres enda litt bedre”.
I Lean prinsippene er tanken om verdiskapning for kunden grunnleggende. Det skal være fokus på tap og fjerning av disse, slik at den ønskede ”flyt” oppnås. Tanken om ”pull”, altså et sug etter varer som skal styre produksjonen, er også et grunnleggende prinsipp. Kontinuerlige forbedringer, med alles involvering, blir da et ”must” for å kunne nå ”den perfekte” produksjon uten tap.
Verdistrømsanalyse
Lean verktøykassen er stort sett lik i begge prosesser (Lean og TPM), med 5S (blant annet renhet, orden, standardisering og systematisering) som grunnleggende.
Verdistrømsanalysen i Lean skiller seg en del fra en TPMs ståstedsanalyse, da denne vil involvere flere avdelinger og elementer. Verdistrømsanalysen (i Lean) følger produktflyten for et spesielt produkt eller produktfamilie, mens ståstedsanalysen (i TPM) hovedsakelig kartlegger situasjonen i en avdeling.
Full fokus
Noen vil kanskje lure på hvorfor begge deler (verdistrømsanalyse og ståstedsanalyse) ikke kan gjøres samtidig, for det er tap mange steder. Svaret vårt, basert på omfattende erfaringer, er tydelig og klart: Ledelsen bør kun ha et fokusområde innen produksjonsforbedring gående!
Denne type prosesser er avhengige av ledelsen, og er en stor utfordring for disse. De skal både styre, involvere, etterspørre og tilbakemelde.
Konklusjonen på sammenligningen er at det er store likheter mellom TPM og Lean, men området som Lean brukes i, er annerledes enn for TPM. Sistnevnte er kun aktuell i produksjonsavdelingene, hvor den bidrar til å fjerne tapene og sikre rett produkt, til rett tid, i rett kvalitet, og vi anbefaler å starte med dette.
Lean dekker hele bedriften, men har ikke samme fokus på stabil produksjon, som hovedsakelig er en forutsetning for Lean. Start derfor med å få kontroll på produksjonsutstyret, det vil si TPM! Men, verktøy og metodikk er stort sett likt.
Velg metode
Uansett, for produksjonsbedrifter som ikke er i gang med et omfattende produksjonssystem:
- Begynn med å bestemme dere for et system (krevende, men nyttig).
- Sørg for involvering og små forbedringer (kaizen).
- Husk på viktigheten for lederne av tilstedeværelse, tilbakemelding og litt ”feiring”.
- Vær tydelige og klare på målene (ingen må være i tvil om hvor vi skal), og husk til slutt:
- Det finnes ingen ”quick fix” – ting tar tid, vær tålmodig (og det kan ofte være en stor utfordring for ledere).