– Induksjonsovner er kjent teknologi, men har så vidt vi vet ikke vært brukt til grafittering til batterier. Vi har så mye kompetanse på høytemperaturprosesser at vi kommer rundt kjente vanskeligheter, blant annet at det er utfordrende å kontrollere prosessen ved så høye temperaturer, sier Inge Grubben-Strømnes, senior vice president i Elkem Carbon.
Det var på forsommeren Elkem slapp nyheten om at de har satt av 65 millioner kroner til å utvikle nye måter å produsere anodemateriale til batterier. Dagens produksjon ligger i området 150 – 200 000 tonn årlig.
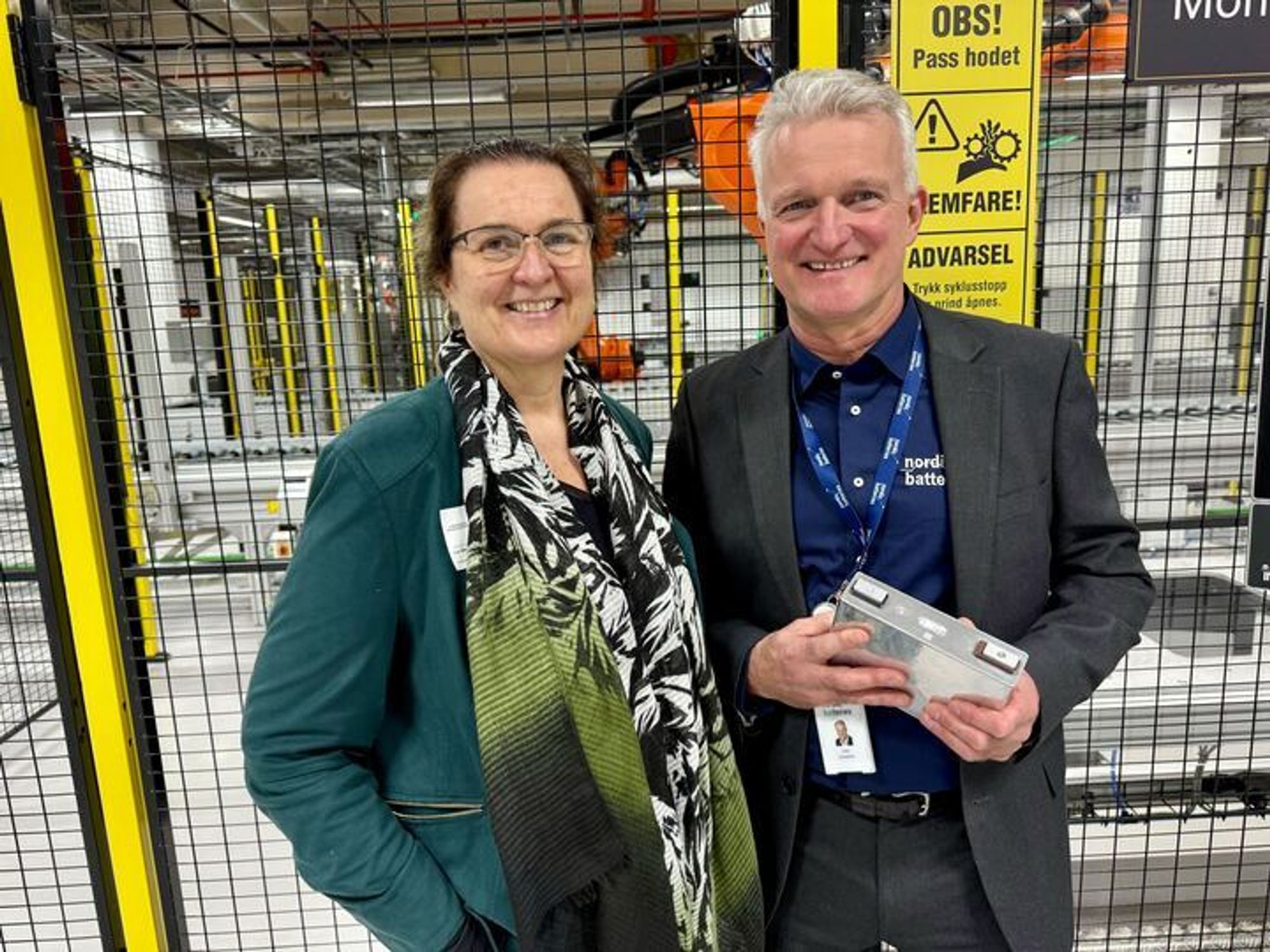
På'n igjen for batterier i Norge

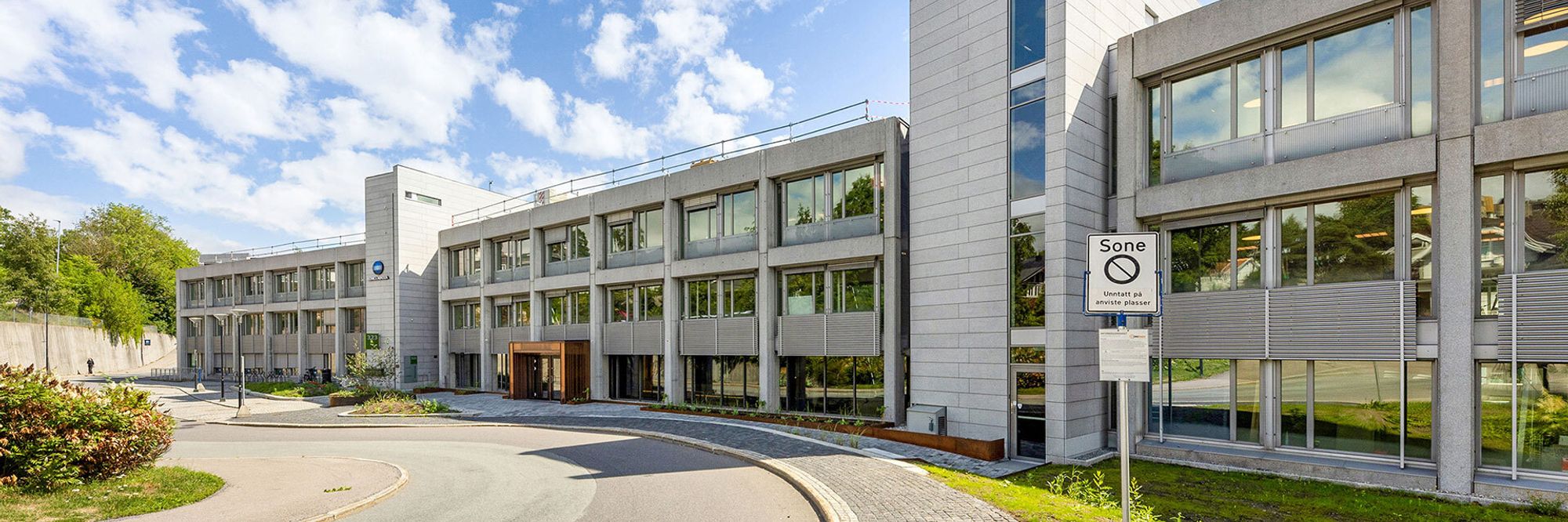
Tidobling
– Veksten blir kraftig, de mest forsiktige anslagene sier den skal opp til 750 000 tonn, mens de mest optimistiske sier mer enn 2 millioner tonn grafitt hvert år, sier Stian Madshus, vice president for batterimaterialer i Elkem.
Flere enn Elkem tror på satsingen. Selskapet har nettopp fått beskjed om at et konsortium de er med i har fått godkjent et prosjekt i regi av EUs forskningsprogram Horizon2020 om utvikling av neste generasjon battericeller til elektriske biler.
– Vår rolle i prosjektet blir å utvikle og levere silisium og grafitt som skal brukes i anodene, sier Madshus.
Programmet går over tre år, øvrige deltakere er ledende europeiske forskningsinstitusjoner og selskaper innen batteriteknologi og materialer. Blant deltakerne er også bilprodusenter.
Grafitt produseres i dag hovedsakelig i Kina og Japan, noe i Sør-Korea. Produsentene bruker en av to vanlige metoder. Med Acheson-metoden brukes en beholder av ildfast materiale med en grafittstreng i bunnen som leder strøm. Så plasseres digler i beholderen med koksen som skal grafitteres og det fylles på med koks. Denne metoden gir kun 30 prosent utnyttelse av tilført energi og store utslipp av støv og svovel. Både temperatur- og tidskontrollen er vanskelig og Acheson-metoden gir derfor varierende kvalitet på sluttproduktet.
Med LWG, lengthwise graffitation kjøres strømmen gjennom det som skal grafitteres – råvaren brukes til oppvarming. Ulempen er at det er vanskelig å få tilstrekkelig høy temperatur, det gir lavere grafitteringsgrad og andelen ferdig grafitt med topp kvalitet er lavere enn med Acheson-metoden.
Mer enn halvert energibruk
Med induksjonsovner mener Grubben-Strømnes at de kan redusere energibruken fra 10-15 kWh per kilo ferdig materiale til 5 kWh.
De to Elkem-direktørene er nå i samtaler med flere forskjellige leverandører av induksjonsovner. Målet er å holde kontakten med samtlige også når en er valgt til å levere pilotanlegget.
– De har kommet med litt forskjellige forslag. For oss er det viktig å se på om vi har tro på konseptet de foreslår, klima for felles utvikling og selvfølgelig kostnad og leveringstid, det er de viktigste kriteriene, sier Madshus.
Dette blir ikke modifisert hyllevare, men helt nyutviklete induksjonsovner for formålet. Det er fem trinn i produksjonen av anodemateriale – rekkefølgen vil kunne variere avhengig av hvilken løsning som blir valgt. Et utgangspunkt er å starte med kalsinering av enten petrolkoks eller bekkoks, dette er en initiell varmebehandling av råmaterialet. Så følger nedmaling til 15-20 mikron, som er 0,015 – 0,020 mm. Trinn tre er å forme kornene i en såkalt shaper – en roterende trommel. Som trinn fire kommer selve grafittiseringen som skjer ved temperaturer rundt 3000°C. Som siste trinn kommer en coating.
.jpg)
Mikrohus med talestyring og storskjerm: – Tenk deg disse som varmestuer i bakkene i Hemsedal
Vurderer produksjonslokaler
Selv om produksjonen fortsatt kun er i laboratorieskala, har ledelsen allerede begynt å se etter lokaler for fullskala produksjon.
– Vi ser for oss å starte med en produksjon på 10.000 tonn og så bygge videre trinnvis derfra. For oss er det flere fordeler ved å legge en slik produksjon her på Fiskå i Kristiansand, men vi vet ennå ikke om det er plass. Det er forhold vi skal vurdere i løpet av høsten, sier Grubben-Strømnes.
.png)
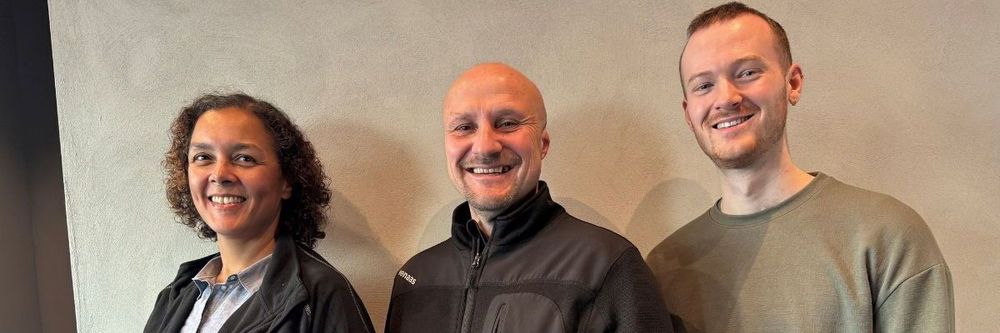
Det ferdige proudksjonsanlegget skal få høy grad av automatisering og gi 100 til 150 arbeidsplasser for en kapasitet på 10.000 tonn.
Forskere og batteriprodusenter jobber intenst med å utvikle faststoffbatterier. Slike bruker ikke grafitt i det hele tatt. Det skremmer ikke Elkem.
– Nei, vi tror at grafitt til anoder vil være vanlig i mange år fremover. Etter hvert får vi kompositter av silisium og grafitt, det blir en fordel for oss siden vi produserer begge materialene, sier Grubben-Strømnes.
Testes for kunder
Ledelsen i Elkem er ikke alene om å vente økt etterspørsel etter grafitt. Til tross for at pilotanlegget ennå ikke er på plass, kun minimalistisk laboratorieproduksjon, sender Elkem allerede anodemateriale til utvalgte kunder for test.
– Tilbakemeldingene er viktige, dette er skreddersøm og forskjellige batteriprodusenter vil ha forskjellige kvaliteter. Endelig kontrakt om leveranser blir ikke aktuelt før vi har et fullverdig produksjonsanlegg, men vi tar sikte på å inngå intensjonsavtaler, sier Madshus.
For europeiske produsenter vil det bety mye å bli mindre avhengig av Kina ettersom batteriproduksjonen øker.
Det er nå et drøyt år siden selskapet etablerte en egen organisasjon, Battery Materials. Den har nå seks ansatte, fire av dem med doktorgrad.
– Vi rekrutterer folk nå, vi trenger flere hoder til dette prosjektet. Det er flere grunner til at vi ser på dette. Vi har tro på at vi kan levere høy kvalitet, så klarer vi å holde produksjonskostnadene tilstrekkelig lave til at vi også tjener penger når prisene faller. For kundene vil en europeisk produsent bety økt forsyningssikkerhet, sier Grubben-Strømnes.
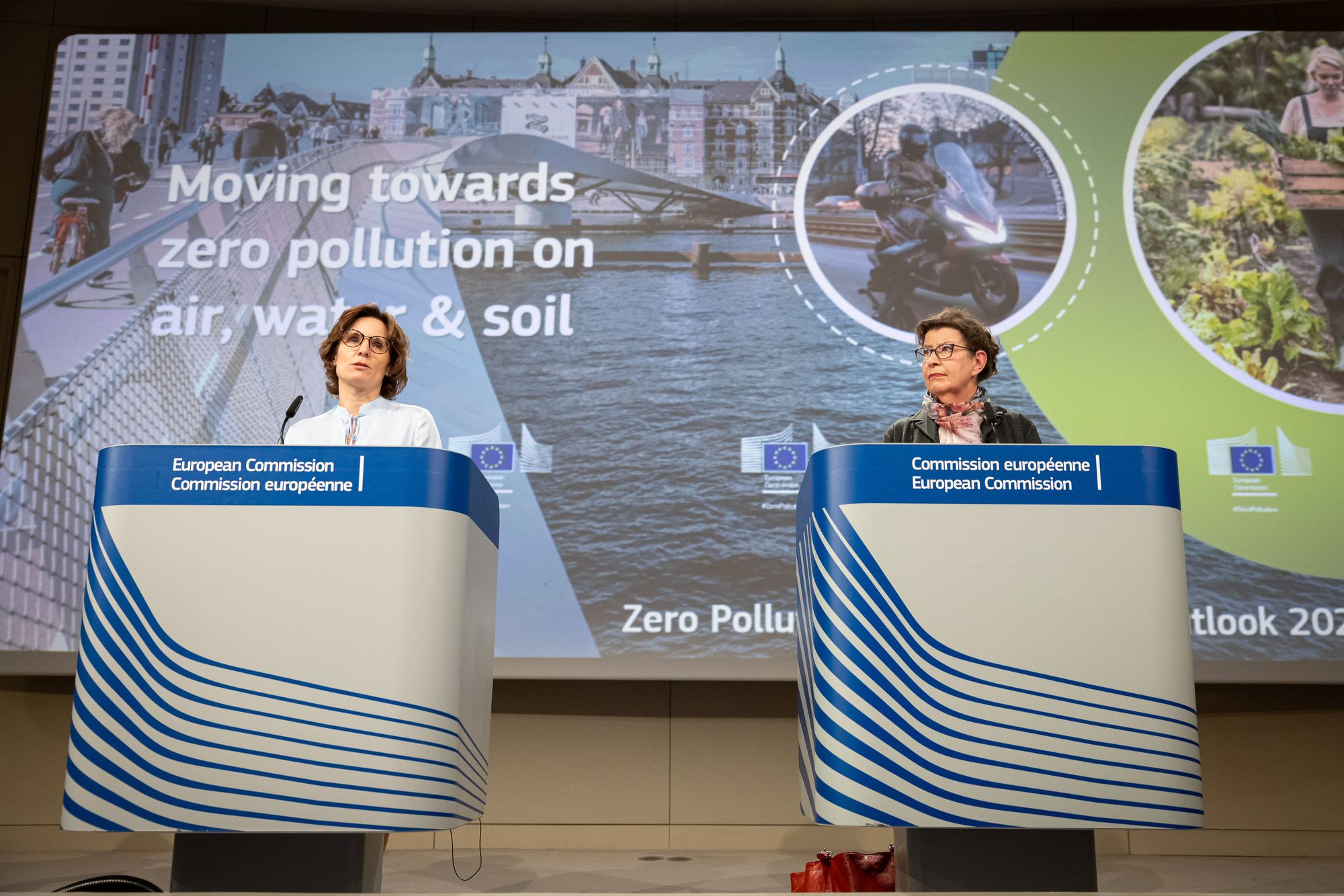
Advarsel i fersk rapport: EU når ikke viktige mål om kutt i forurensning innen 2030