Hydro har satt spaden i jorda og begynt å bygge verdens mest energieffektive og miljøvennlige aluminiumsfabrikk på Karmøy.
Anlegget er en av de største investeringene i norsk fastlandsindustri, sett bort fra olje- og gass, på over ti år.
Hydro har siden 2005 forsket på hvordan et patent fra 1886 kan bli 15 prosent mer effektiv. Ikke sammenlignet med 1886, men i forhold til dagens gjennomsnittlige energibehov for å produsere en kilo aluminium.

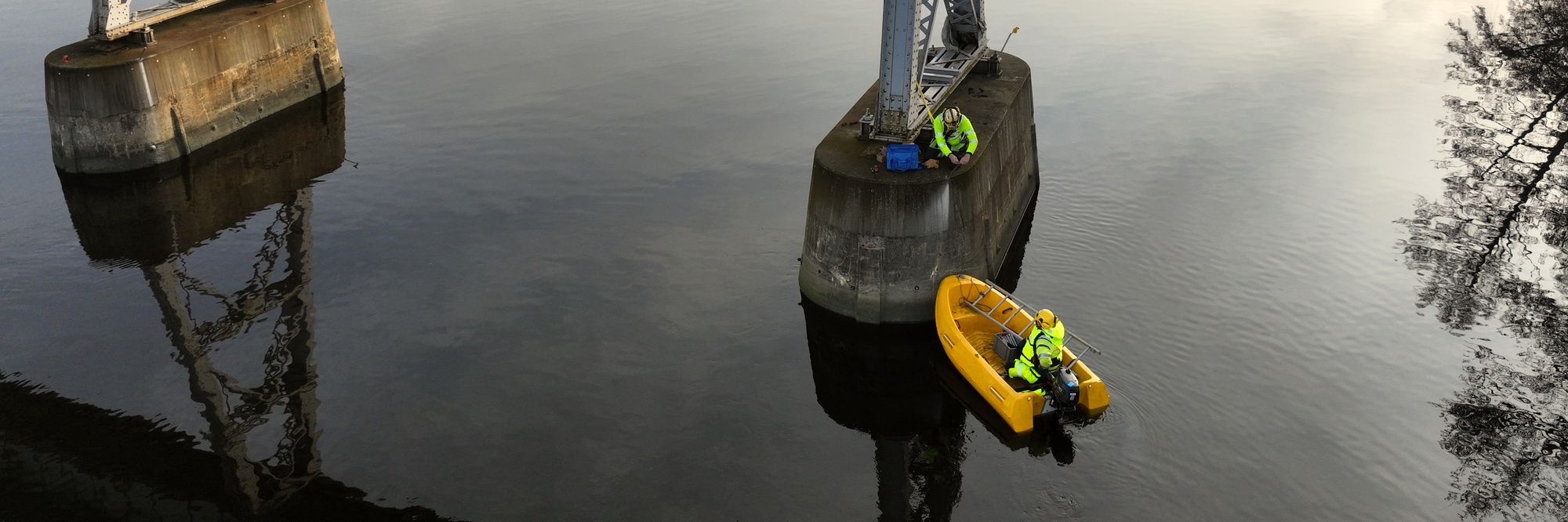
– Dagens gjennomsnitt er 14 kWh per produsert kilo aluminium. I testproduksjonen ved seks celler i Årdal er vi på vei ned til 12,3 kWh. Det er også målet med full produksjon fra 60 celler på Karmøy, sier teknologidirektør Hans Erik Vatne. Konkurrentene er ikke i nærheten.
KANDIDAT 4: TU TECH AWARD 2016
HVEM: Hydro Karmøy Technology Pilot (KTP)
HVA: Aluminiumsproduksjon med svært lavt energibruk og utslippsnivå
BESKRIVELSE: Hydro besluttet i år å begynne bygging av et fullskala pilotanlegg for aluminiumsproduksjon med egenutviklet, ny elektrolyseteknologi, HAL4e.
Målet er å redusere energiforbruket med 15 prosent per kilo aluminium produsert.
Verdensgjennomsnittet i dag er i overkant av 14 kWh/kg, hoveddelen av pilotanlegget skal klare 12,3 kWh/kg, mens en mindre gruppe celler (12 stk) skal komme ned mot 11,5 kWh/kg. Anlegget vil i full produksjon ha en kapasitet på 75.000 tonn i året. Oppstart andre halvår 2017.
Når pilotfabrikken på Karmøy er kommet i full gang, etter planen i annet halvår neste år, vil den produsere 75.000 tonn årlig. Det er ikke en liten fabrikk, men på størrelse med verket i Høyanger.
Teknologien, kalt HAL4e, innebærer forbedringer på mange punkter i forhold til «vanlig» elektrolyse, som patentet fra 1886 bygger på.
Små skritt blir langt sprang
Siden 2008 har Hydro testet ut og forbedret den nye elektrolyseteknologien HAL4e i Årdal. Hva har de egentlig gjort med den 130 år gamle oppfinnelsen?
Asgeir Bardal har vært sentral i teknologiutviklingen. Han forklarer oppbyggingen av elektrolysecellene.
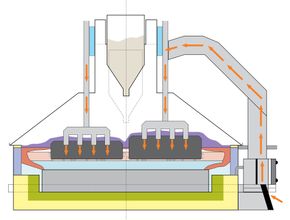
I elektrolysecellene blir aluminiumsoksid og kryolitt varmet opp i en smelte til 960 grader celsius. Strømmen går gjennom anoder og til en katode, det vil si hele cellens bunn og alle sidene er fôret med steinmaterialer og inneholder karbon-blokker som fungerer som katode.
Anodene henger ned i smelten ovenfra. Ved anoden frigjøres gassene karbonmonoksid og karbondioksid, og anoden forbrukes sakte og må erstattes, cirka en gang i måneden. Aluminium synker til bunns og tappes ut, mens aluminiumsoksid fylles etter.
– Det er kombinasjoner av teknologi-elementer, små endringer i oppbyggingen av skinnesystem, anoden og katoden, isolasjonen, materialvalg og geometrien, som spiller sammen. Kan vi hente inn noen millivolt her og der, blir det til sammen store energimengder, påpeker Bardal.
BEGRUNNELSE: Pilotanlegget skal bli verdens mest energi- og klimaeffektive aluminiumsproduksjon.
I Kina slippes det ut 18-20 kg CO2-ekvivalenter pr produsert kilo aluminium når man regner med utslipp knyttet til fremstilling av råstoff, samt produksjon av nødvendig elektrisitet. På Karmøy vil utslippet være nede i 3,5 kg, verdens desidert laveste.
En million tonn aluminium produsert i Norge sparer verden for 15 millioner tonn CO2 når alternativet er kullkraftbasert aluminium fra Kina.
SAMARBEIDSPARTNERE: NTNU, SINTEF, IFE.
Design og drifting av celleteknologien ville ikke vært mulig uten langsiktig oppbygging av grunnleggende forståelse og avanserte matematiske modeller av elektrolyseprosessen i samarbeid med instituttene over mange år.
STØTTE: Enova (1,6 milliarder kroner), Innovasjon Norge (22,5 millioner kroner)
Blant de store utfordringene er enorme magnetfelt som dannes rundt cellene på grunn av den høye strømstyrken. Det påvirker både prosessen i den enkelte celle, og i naboceller.
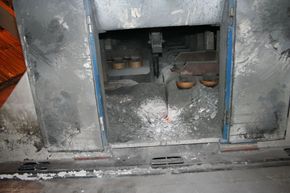
Smeltet aluminium inne i cellene settes i bevegelse av magnetfeltet. Det kan skape uønskede bølger i smelten.
Ujevn overflate betyr forskjellig høyde mellom anode og katode, noe som gir ustabil prosess, økt energiforbruk og økt klimagassutslipp.
.png)
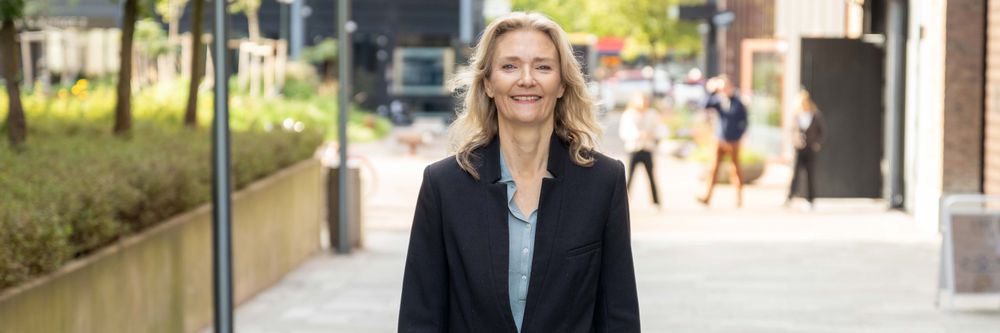
– Kan vi senke anoden noen få millimeter og slippe å justere den på grunn av bevegelser i smelten, er det enormt mye å spare, sier Bardal.
- De vokser fra 1 centimeter til 1,5 meter på fem måneder: Nå kan de bli vår nye milliardindustri
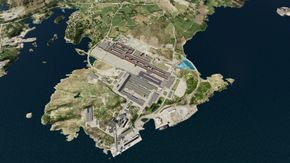
Digitalisering og Industri 4.0
I tillegg til de rent fysiske og materialtekniske forbedringene, har Industri 4.0, eller den digitale revolusjonen, kommet til prosesstyringen til Hydro.
– Vi ser Karmøy Pilot som det første prosjektet hvor vi implementerer en ny kontrollplattform, bygget på digitalisering. Det gir oss nye muligheter, sier Bardal.
Informasjon fra sensorer betyr mulighet for sanntidsstyring. Nå utvikles også plattformen for prediktiv styring.
– Vi skal kunne hente inn måledata, se prosess-indikatorer og modellere hva som kan skje. Det skal benyttes til å foreta justeringer slik at fremtidige feil i prosessen unngås, sier Bardal.
Pilot og mot
I og med at Hydro kaller Karmøy-prosjektet en «pilot», tyder det på at selskapet ikke «tør» å bygge en fullskalafabrikk basert på HAL4e.
– Det er et langt skritt fra testceller til pilot. Blant annet er det nødvendig å se hvordan magnetfeltproblematikken blir i en fabrikk med 60 celler, det vil si ti ganger større enn i testhallen, forklarer Vatne.
Bardal tror pilotproduksjon har stort potensial for å gå bedre enn testproduksjonen.
– Vi får mer stabile driftsforhold. Prosesstyringen bør bli lettere i et stabilt driftsmiljø enn på et testsenter. Under testing er det stadige endringer, ombygginger og forhold som kan forstyrre produksjonen sier Bardal.
Han tror at Karmøy Pilot i løpet av to år vil bevise at HAL4e lykkes med målet om 12,3 kWh per kilo aluminium.
- Norwegian Crystals startet opp i asken av REC: I år forventer de overskudd
.jpg)
FoU tas direkte ut i drift
Hydro har rundt 50 ingeniører og forskere i sving med å forberede HAL4e-teknologien, og en videreutviklet versjon som også skal testes i mindre skala på pilotenHAL4e Ultra. Der er målet å komme ned mot 11,5 kWh/kilo.
– Vi er godt i gang og det ser lovende ut, sier Vatne. Han er glad for at konsernsjef Svein Richard Brandtzæg selv har en doktorgrad i kjemi og skjønner hva forskeren holder på med.
– Målet vårt er enda mer hårete og konsernsjefen har vært med på å sette det. Vi skal ned i 10 kWh/kilo, sier Vatne.
UAVHENGIG VURDERING: Instituttleder for materialteknologi ved NTNU, Jostein Mårdalen, sier at det er vanskelig å finne noen eksperter på aluminiumsproduksjon i Norge som ikke er mer eller mindre inhabil. Det gjelder også ham.
– Det er det tette trekantsamarbeidet Hydro, Sintef og NTNU som har bragt teknologien så langt fram, sier Mårdalen til TU.
Personlig har han ikke direkte tilknytning til Hydro-prosjektet, men to av de ansatte er det. Han har vært i kontakt med andre selskaper. De uttrykker at Hydros arbeid for å energieffektivisere produksjonen er med på å presse hele industrien.
– Konkurrentene ser på Hydro som en pådriver for energieffektivisering. Hydro har allerede verdens laveste gjennomsnittlige energibruk med 13,8 kWh per kilo. Med piloten forbedrer de sin egen verdensrekord og har hårete ambisjoner om 10 kWh, sier Mårdalen.
Han tror at Hydro får et konkurransefortrinn ved å ha et så lavt CO2-fotavtrykk som mulig.
– Vi blir mer og mer opptatt av hvordan produktene vi kjøper er framstilt og at det skal være så miljøvennlig og energieffektivt som mulig. Der scorer Hydro høyt allerede, og med pilotprosjektet blir det enda bedre, sier Mårdalen.
Hydro trenger ikke vente i mange år på å realiserer resultater fra HAL4e og HAL4e Ultra.
– Vi lærer og oppdager stadig noe vi kan overføre til alle våre verk, sier Vatne.
Hver celle må rives og bygges opp igjen med blant annet ny katode og isolasjon om lag hvert sjette år. I store verk med flere hundre celler er det alltid noen som bygges opp igjen.
Dermed oppgraderes alle verk sakte, men sikkert.
- Yara mangler råstoff: Nå har de funnet løsningen i et miljøproblem
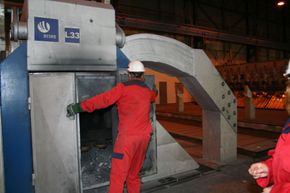
Energi og effektivitet
Det kreves store mengder energi for å omdanne bauxitt til aluminium. Hydro regner med energi utgjør rundt 50 prosent av produksjonskostnaden fra gruve til sluttprodukt. Billig norsk vannkraft og stadige teknologiforbedringer, gjør aluminium til et miljøvennlig materiale. Norsk aluminium er kalt grønn energi i fast form.
– Frem mot 2025 forventer vi at aluminiums-etterspørselen øker med fire til fem prosent i året. Materialet er med på å gjøre industriprodukter, biler, tog og annet lettere. Etterspørselen er også geografisk nær. Vi ser ikke at pilotanlegget på Karmøy vil skape overskudd i markedet i Europa, sier Vatne.
.jpg)
Nå er pilotfabrikken til 4,3 milliarder kroner besluttet bygget. Det er det største industriutbyggingsprosjektet på fastlandet siden Sunndalsøra ble bygget ut i 2002.
Enova støtter prosjektet med cirka 1,55 milliarder kroner. Tanken er at mer miljøvennlig aluminiumsproduksjon i Norge, bidrar til globalt mindre utslipp.
Økt produksjon i Norge, basert på vannkraft og mer energieffektiv teknologi, har effekt langt ut over landets grenser. Trekker vi argumentasjonen enda lengre, medfører aluminium i biler, fly og annet at drivstofforbruket går ned.
Hans Erik Vatne har ingen problemer med å innrømme at driveren til å satse på den nye teknologien er å få ned energibruken.
– Da får vi ned kostnader. Men vi får veldig mye oppmerksomhet rundt miljøgevinsten på flere plan, sier Vatne.
Grønn energi fast form
I og med at aluminium i Norge produseres av ren vannkraft, kunne Hydro slått seg til ro med det.
– Vår produksjon går inn i et globalt regnestykke. Kan norskprodusert aluminium erstatte kullbasert produksjon i andre land, er det positivt, sier Vatne.
Han sammenligner med aluminium fra Kina. Under produksjon av aluminium slippes det ut CO2.
– Norskprodusert aluminium slipper ut omtrent 3,5 kg CO2 per produsert kilo når vi tar med hele verdikjeden fra gruve til ferdig produkt. Tilsvarende i Kina er 18-20 kilo CO2. Det stammer både fra mindre effektiv produksjon og at kraftbehovet dekkes av kull. Isolert sett øker Norges CO2-utslipp når vi øker produksjonen her. Men når en kilo norsk Hydro-aluminium går inn i markedet i stedet for kinesisk, sparer vi 15-16 kilo CO2, påpeker Vatne.
- Produktet kom i 2011. Året etter var det norske selskapet lønnsomt: Nå er de størst i verden
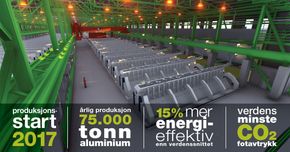
Fakta: Slik lages aluminium
- Aluminiumsoksid framstilles fra aluminiumsholdig mineral (bauxitt).
- Det må 4–5 kg bauxitt til for å lage 2 kg aluminiumsoksid, som via elektrolyse med tilsetning av karbon (0,4 kg), aluminiumsfluorid (50 g) og kryolitt (50 g), blir til 1 kg aluminium.
- Det går med ca. 13–15 kWh energi for hver kilo aluminium. Det dannes ca. 1,6 kg CO2. Ved resirkulering, trengs bare 5 % av energien. Aluminium kan resirkuleres så å si i det uendelige.
- Med HAL4e skal Hydro presse grensen for energiforbruk ned til 12,3 kilowattimer per kilo produsert aluminium (kWh/kilo), samtidig som produktiviteten ved cellen holdes på et veldig høyt nivå. I dag ligger verdensgjennomsnittet på 14 kilowattimer per kilo produsert, med en strømtetthet og dermed produktivitet, som er mye lavere enn den som Hydro jobber med å realisere.
- CO2-utslippene skal samtidig ned til omtrent 1,5 tonn per tonn aluminium, noe som er verdensledende. Allerede før teknologien er implementert i ordinær drift, jobber forskerne med neste versjon av teknologien, HAL4e Ultra. Der er målet å komme ned mot 11,5 kWh/kilo og 1,5 tonn CO2.
- Aluminiumproduksjon er meget energikrevende. Prosessforbedringer har medført reduksjon i energiforbruket fra cirka 50 kWh per kg aluminium i 1900, til 20 kWh i 1940, ned i cirka 13–14 kWh per kg i dag.
- Har ikke tatt opp en dråpe olje: Hevder dette bildet viser starten på hele milliardskandalen