Spar-plattformen i seg selv er ekstrem. Den vil bli 320 meter høy med dekksanlegg. Selve flyteren er 198 meter topp til bunn og blir verdens største.
Aasta Hansteen er en svenneprøve og et stykke teknologikvalifisering Statoil og leverandørene kan dra nytte av for seinere prosjekter.
Feltet ligger 300 kilometer vest for Bodø, nord for Polarsirkelen. For første gang skal det bygges ut på 1200–1300 meters havdyp med store bølger, kraftig strøm, minus 1,5 grader på havbunnen uten eksisterende infrastruktur.
Les også: Kjempeskipet Dockwise Vanguard kan løfte 117.000 tonn. Nå vil eieren bygge enda større
4 x Nordsjøen
Sammenlignet med operasjoner på rundt 300 meters dyp som er vanlig i Nordsjøen, vil alt ta lengre tid. En ROV (ubemannet undervannsfartøy) bruker tre–fire ganger lengre tid opp og ned. Løftewirer vil i seg selv veie 100 tonn og dermed spise av vekten til utstyret som settes ned på havbunnen.
Dette har hatt betydning for oppbyggingen av produksjonsmanifoldene subsea. De bygges opp som «toastrack» – det vil si at moduler senkes ned en for en og plasseres i bunnrammen som om det var ristete brødskiver.
– Dette er noe av det mest spennende som skjer på norsk sokkel. Både vi og våre leverandører lærer veldig mye, sier Helge Hagen, prosjektleder for subsea på Aasta Hansteen.
Les også: Her er 26 av de viktigste teknologiene fra oljebransjen
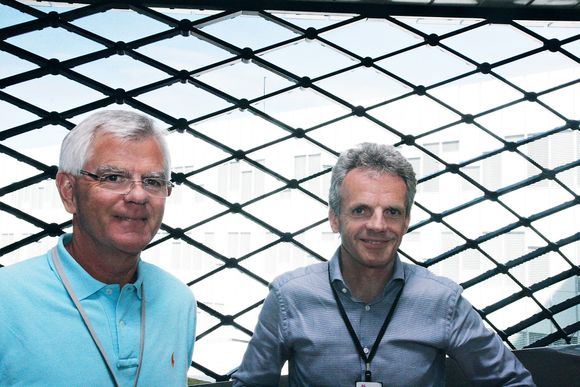
Tilpasset ekstremdyp
I Mexicogolfen, utenfor Vest-Afrika og utenfor Brasil har det i mange år vært produsert fra felt med havdyp ned til 1500 meter. Den erfaringen er ikke direkte overførbar. Temperaturer i vannet, kraftig strøm, høye bølger, polare lavtrykk og annet ekstremvær – alt samtidig, har de ikke der.
Statoil har omfattende teknologikvalifiseringsprogram (TQP) for utstyret.
– Vi kjører TQP i henhold til DNV GL-krav og prosedyrer. Vi er straks i mål, sier Hagen.
Han trekker spesielt fram subsea produksjonssystemer.
– Aker Solutions utvikler en ny dypvannsstandard, med installasjon uten bruk av «guide wire» og med et sikrere og mer kostnadsbesparende brønnkontrollsystem, sier Hagen.
Havbunnsinstallasjonene består av tre undervanns produksjonsanlegg, Luva, Haklang og Snefrid med til sammen sju brønner. Brønnrammene produseres av Aker Solutions i Sandnessjøen. Manifolder bygges i Egersund, juletrær på Tranby og kontrollsystem i Aberdeen.
Les også: Dette er Norges ukjente milliardbutikk
.png)
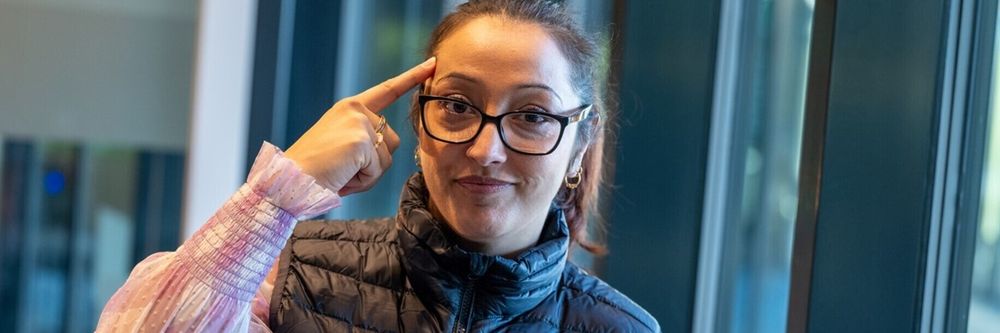
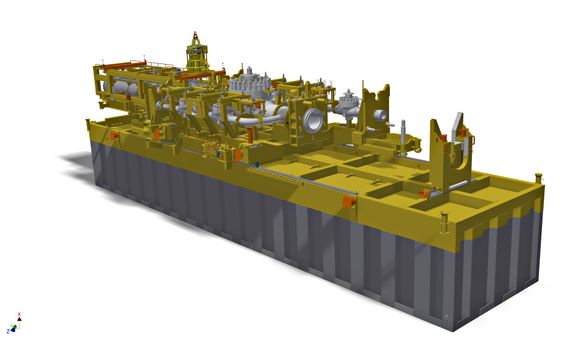
Stiv og fleksibel
Spar-plattformen har svært lite bevegelse.
Dette skyldes utformingen og 17 stramme ankerliner. På havbunnen festes linene til store sugeankere, bygget og levert fra Momek i Mo i Rana som underleveranse til Subsea 7.
Sugeankrene er hver på 145 tonn, 20 meter lange og diameter på seks meter. Ankerlinene er av polyester med kjetting i hver ende for innfesting mot plattform og mot sugeankrene.
– Dermed kan vi bruke stive stigerør, noe vi ikke har brukt i Norge tidligere, sier Hagen.
På grunn av lengden vil stigerørene være tilstrekkelig fleksible til å tåle plattformens bevegelser. For å unngå strøminduserte svingninger er det påmontert finner på stigerørene.
Minusgrader i vannet og trykk på 120–130 bar stiller en del nye krav til utstyr, blant annet materialer og pakninger.
Les også: Denne monsterkatamaranen skal løfte Yme på åtte sekunder
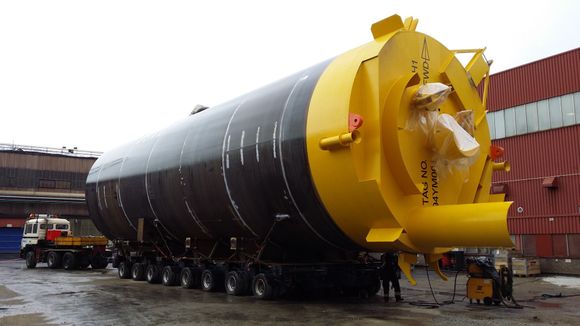
Bubirør
Subsea 7 er engasjert til marine operasjoner. De skal forhåndsinstallere fortøying, legge ut de 17 ankerlinene og fire stigerør. Brønnrammene installeres av Emas.
Subsea 7 skal legge flere kilometer produksjonsrør (flowline). Rørene lages på en spesiell måte som ikke tidligere er lagt på spole.
Bubi-rør består av en slags rør-i-rør-løsning. Det går ut på å varme det ytre røret, tre inn innerrøret i rustfritt stål og sette på trykk. Diameter på innerrør ekspanderer til det treffer ytterrør. Begge utvider litt, kjøles og krymper.
Les også:
DNV GL vil bruke «Prius-teknologi» på oljeplattformer