Sagstua, Nord-Odal: I enden av en én og en halv times biltur fra Oslo, til dels på svingete og smale veier, finner vi Mapei AS.
I det lett kuperte jordbruks- og skoglandskapet er det langt mellom industribedriftene, universiteter og høyskoler. Likevel har Mapei utviklet kunnskap og produkter i verdensklasse.
Mapei jobber målrettet for å skaffe seg og utvikle kompetanse på tilsetningsstoffer som gir betong og sement de ønskete egenskaper.
– Deltakelse i forskningsprosjekter med aktører fra flere bransjer er avgjørende for å øke kunnskapen, sier administrerende direktør Trond Hagerud.
Han er sjef for 250 ansatte i Norden, derav 150 ved hovedkontoret og produksjons- og forskningsavdelingen i Nord-Odal. I fjor omsatte selskapet for 640 millioner kroner. Omsetningen vokser jevnt og trutt og kan glede de italienske eierne i Milano med solide overskudd.
Les også: Japanerne skriker etter ren energi - nå vil de hente den fra Finnmark
BIA-prosjekter
Nå deltar Mapei i tre store forskningsprosjekter i tre ulike bransjer. Alle er BIA-program, det vil si brukerstyrt innovasjonsarena med offentlig støtte og deltakelse fra forskningsinstitusjoner og næringslivet.
Målene er å:
- Redusere CO2 utslipp fra sementproduksjon.
- Forbedre tunnelsikkerhet.
- Forbedre frostbestandig betong til bruk innen olje og gassektoren i arktisk og subarktisk klima.

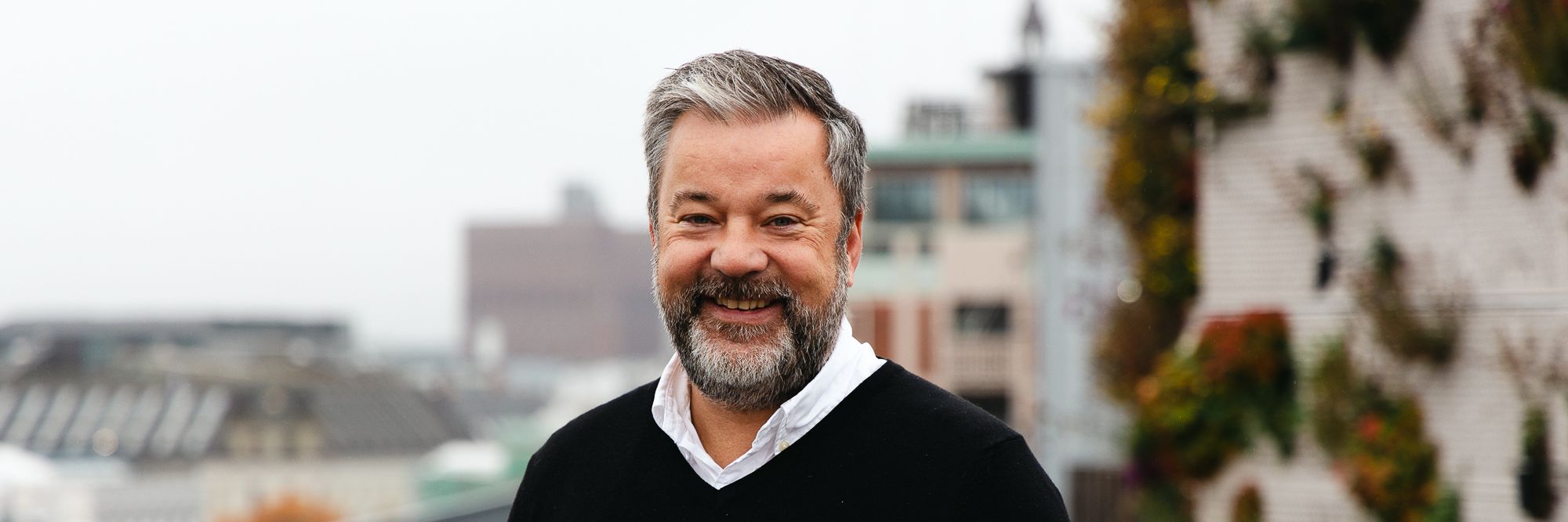
Rundt 14 av de ansatte i Nord-Odalen er involvert i forskningsaktivitetene. Det investeres jevnlig i nye instrumenter og utstyr til de fire laboratoriene i huset.
Les også: Eierne flytter halve maskinparken - resten kan bli starten på et norsk industrieventyr
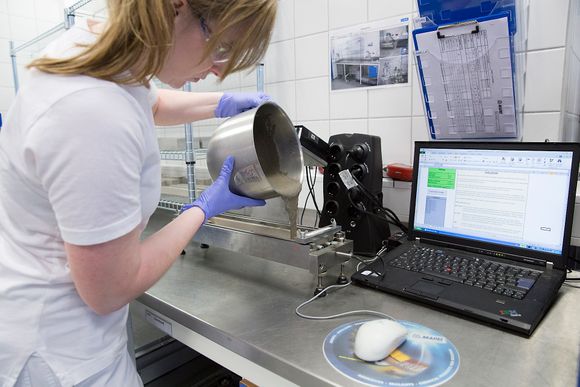
Investerer i FoU
– Mapei-konsernet bruker fem prosent av omsetningen på forskning. Om lag 12 prosent av samtlige ansatte globalt er involvert i FoU-aktivitetene, sier Hagerud.
I 2007 investerte Mapei, som tidligere het Rescon, i et nytt bygg med tre produktrettete laboratorier og nytt anlegg for produksjon av tilsetningsstoffer til betong. I 2012 ble laboratoriet for kvalitetskontroll oppgradert. Der kontrolleres råvarer inn og ferdig produserte varer kvalitetssikres.
Ettersom Nord-Odal ikke er et akademisk knutepunkt, jobber Mapei med lokal rekruttering ved å støtte realfagsutdannelse og arrangerer en årlig mattekonkurranse for Glåmdal-regionens ti ungdomsskoler. Ansvarlig for konkurransen nå, Nodar Al-Manasir, har ikke sin opprinnelse fra Nord-Odal.
– Jeg har doktorgrad i kjemi fra Universitetet i Oslo, sier Al-Manasir, som tidligere har jobbet i DNV og leder nå forskning på tilsetningsstoffer i betong.

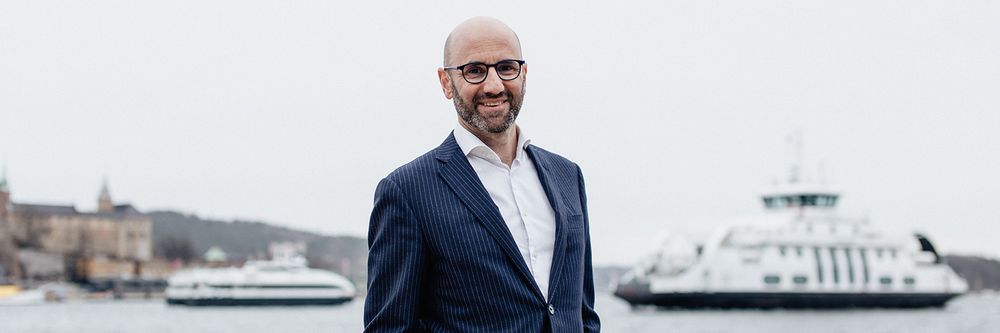
Les om det norske gjennombruddet:Norsk gjennombrudd: Produserer 40 ganger raskere enn vanlige metoder
Fra vugge til videregående
– Vi begynner omtrent med barnehagene, sier Hagerud med et smil.
Selv er han fra Kongsvinger og er dermed ikke langt fra hjemtraktene. Selskapet har i over 10 år arrangert realfagkonkurranser.
– Vi har gått gjennom navnelister og kontaktet tidligere deltakere via Facebook. Det er gledelig mange som har fått inspirasjon til å studere realfag på grunn av konkurransene, sier Hagerud.
Bevis på det finnes hos Mapei. Sivilingeniørene Espen Rudberg og Kine Buchholdt Jonassen gikk i samme realfagklasse på en lokal videregående skole og tok videre kjemi-studier i Trondheim. Etter endt studietid, flyttet de etter hvert tilbake til hjemtraktene.
De er enige om at Mapei var et naturlig og attraktivt jobbønske da de flyttet hjem. I dag er Rudberg forskningsleder for malehjelpemidler til sementproduksjon og tunnelprodukter. Kine Buchholdt Jonassen er forskningsleder for herdeplast og polymerlaben.
Espen er i tillegg Mapeis prosjektleder for BIA-prosjektet Lavkarbsem. Prosjektet ledes av Norcem som er en del av Heidelberg Cement Group.
Les også: De trosser oljenedgangen - har tidoblet ordreboka
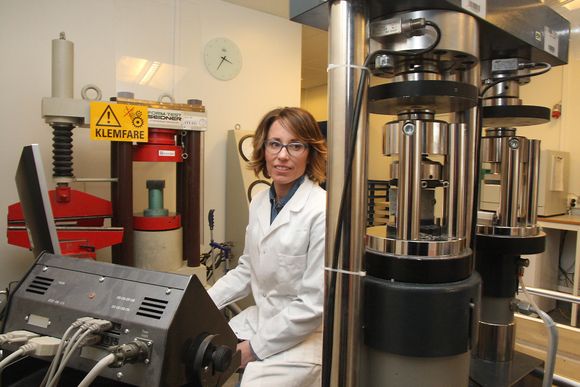
Fra olje til CO2-reduksjon
Verdens sementindustri står for omkring fem prosent av menneskeskapte CO2-utslipp.
Heidelberg Cement Nord-Europa vil være med og redusere det høye prosenttallet. Målet er null CO2-utslipp innen 2030. Ett av virkemidlene på veien er å lage sement som gir lavere karbonavtrykk. De vil utvikle sement der de erstatter karbonintensivt klinker med andre materialer. Slike typer sementer kalles ofte blandingssementer.
I tillegg til Espen Rudberg deltar også Al-Manasir og Buchholdt Jonassen i forskningsprogrammet Lavkarsem for Mapei. Programmet er delt inn i seks delprosjekter som studerer karbonatiseringsmekanismer, råmaterialer og tilsetningsstoffer til klinker- og sementproduksjon, metodeutvikling for måling av karbonatisering, levetidsprosjektering og akseptkriterium innen dagens standarder samt karbonatiseringsbremsende tiltak i betongkonstruksjoner.
– Målet er å redusere CO2-utslippet når sement produseres. Vi ser på hva vi kan erstatte det med og samtidig opprettholde sementens egenskaper. Kalkstein kan for eksempel bidra til dette. Da må også nye tilsetningsstoffer til sement- og betongproduksjon testes. Det gjør vi både her og ved laboratoriet i Milano, sier Al-Manasir.
Les også: Kremen av norsk forsvarsindustri og båtbygging har gått sammen. Dette er resultatet
Holder CO2 ute
Mens den ene laben hos Mapei skal ha ned CO2-utslippet ved bruk av sement og betong, er polymerlaben opptatt av hvordan de kan hindre CO2 å bli tatt opp eller trenge inn i betong basert på blandingssementer.
Det er en oppgave for Buchhold Jonassen og laben for herdeplast og polymer der det utvikles alt fra vannbaserte primere, membraner til epoksy eller polyuretanbaserte malinger og belegg. Hovedformålet for Lavkarbsem-prosjektet er å øke bestandigheten i slike type betonger.
– Vi ser på produkter og produktsystemer for å stoppe eller bremse inntrenging av CO, sier Kine.
CO-indusert karbonatisering i betong med armeringsjern betyr kortere levetid. CO bidrar til senkning av pH i betongens poreløsning. Når pH synker mister armeringsstålet sitt beskyttende passive belegg som igjen fører til korrosjon. Dette vil svekke styrken av betongen.
Les også: 58 bedrifter skal kjempe om å være Norges smarteste
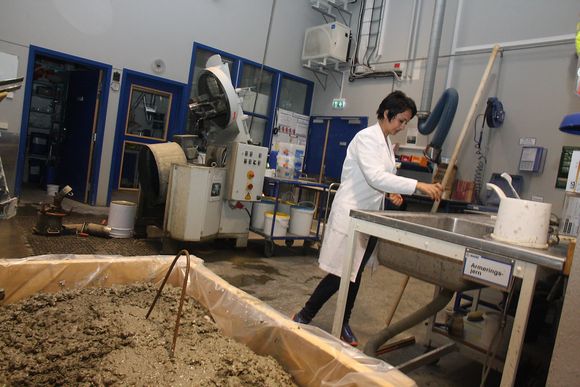
Tetter med mikrosement
I Forskningsropgrammet TIGHT (True Improvement in Grouting High pressure Technology for tunneling) med Sintef som prosjektleder, er målet å øke sikkerheten og levetiden til tunneler ved å utvikle en metode for å stabilisere berggrunnen før tunnelene bygges.
– Ved å injisere sementmasse inn i berggrunnen som herder i bergsprekkene hindres vann fra å trenge inn i tunneler og bergrom. I dag er metodene for tunnelbygging i Norge lite standardisert. Prosjektet som har derfor som mål å utvikle metoder, standarder, kompetanse og teknologi for berginjeksjon med høyt trykk, sier Bjarne Ruud.
Han var med på å sikre Romeriksporten, jernbanetunnelen som fungerte som en sil for Romeriksåsen og tømte Puttjern. Mapei var en av flere aktører som fikk teste og prøve ut produkter for å tette.
– Det er mye dyrere å gjøre en tunnel tett i etterkant. I TIGHT ser vi på hvordan vi kan tette sprekker og riss i forkant. Vi ser på ulike materialer, deriblant ulike sementer, blant annet mikrosement, sier Ruud med mer enn 30 års fartstid i Mapei.
Injeksjonshull bores i en skjerm i 12–15 graders vinkel cirka 24 meter inn i tunnelprofilen og mikrosement eller andre materialer kan pumpes inn og herde før sprenging eller tunnelboremaskin spiser seg nye 12–15 meter innover.
Norges Geologiske Institutt (NGI) er med i prosjektet. De har spesialutstyr for å teste og måle virkningen av materialene som skal testes. En doktorgradsstipendiat er knyttet til arbeidet.
Les også: Bilindustrien skriker etter aluminium: Hydro klarer ikke å levere nok
Til Follo og ut i verden
Dette er svært aktuelt for driving av tunnel til Follobanen.
– Det prosjektet har hele anleggsverdenens øyne rettet mot seg. Interessen fra utlandet er formidabel, sier Ruud.
Ett av feltene Mapei ser på er partikkelstørrelse på mikrosementen for å få den til å tette risser og sprekker. I dag er vanlig partikkelnivå ned mot 20 mikrometer (µm). Antakelig må man ned i 12 µm.
– Hvordan opptrer de i sprekkene, hva er den rette størrelsen og hvor fort kan sementen herdes. Det er slike ting vi må finne ut av i prosjektet, sier Ruud.
Selv om skoger og åser omgir Nord-Odalens mest avanserte laboratorier, er det saltvann og olje- og gassutvinning som preger arbeidet til Trond Helgedagsrud.
Han er Mapeis leder for arbeidet i forskningsprogrammet DaCS (Durable advanced Concrete Solutions) er målet å utvikle betongteknologi og reparasjons-produkter som tåler ekstreme forhold i arktisk klima.
Prosjektet er delt inn i følgende delprosjekter:
• Early age cracking and crack calculation in design
• Production and documentation of frost durable concrete
• Concrete ice abrasion
• Ductile Lightweight Aggregate Concrete (LWAC)
Mapei deltar i tre av de fire delprosjekter i DaCS. Al-Manasir er ansvarlig for to av delprosjektene på vegne av Mapei. Totalbudsjettet er 41 millioner kroner over fire år. Det er knyttet flere doktorgradsstipendiater til programmet.
Blant temaene er å se på hvordan riss og sprekker kan oppstå, og hvordan det kan repareres, spesielt i kaldt vær. I henhold til databladene bør det være 5 plussgrader. Det kan være vanskelig i Arktis. I tillegg skal det utvikles betong som tåler is og isskuring bedre. Hvilke tilsetningsstoffer må til og hvordan dosere riktig.
Det er ikke bare innen offshore, men også på bruer det er aktuelt å øke bestandighet på betong i kalde årstider med frost. Økt levetid og lavere vedlikeholdskostnader er viktig for de fleste prosjekter, ikke minst for bruer og tunneler.
Les også: Tunnelboremaskinene har gravd ut seks millioner tonn masse - dette brukes den til