Det var rett i overkant av 70 påmeldte kandidater til årets kåring av Norges smarteste industribedrift.
Juryen har fått en liste på 10 kandidater til vurdering. Av dem blir tre plukket ut til superfinalen. Vinneren utropes 9. mai på Industrikonferansen i Oslo.
Finalistene er godt spredt, både geografisk og bransjemessig.
1. Avery Dennison
Produserer transfermerker til sportsklær, arbeidstøy og profilklær. Produksjonen er basert på silketrykk, som er lite egnet til masseproduksjon og stabil kvalitet.
Bedriften har jobbet kontinuerlig i 30 år med forbedring av produksjon og kompetanse. Det er utviklet en digital plattform for interaksjon med kundene, planlegging av produksjon og råvarer, produksjonsprosessen, kvalitetsstyring og forsendelse til kundene.
Den digitale plattformen i kombinasjon med eget kompetansesystem førte i fjor til 14 prosent økt effektivitet, 25 prosent redusert leveringstid og redusert kundereklamasjoner med 40 prosent.
Selskapet, som er amerikanskeid, har fjernet over 1.000.000 papirark fra produksjonen og kan presentere oppdatert og relevant informasjon til operatører, ingeniører og ledelsen til enhver tid.
Holder til i Gaupne i Sogn og Fjordane med 130 ansatte.

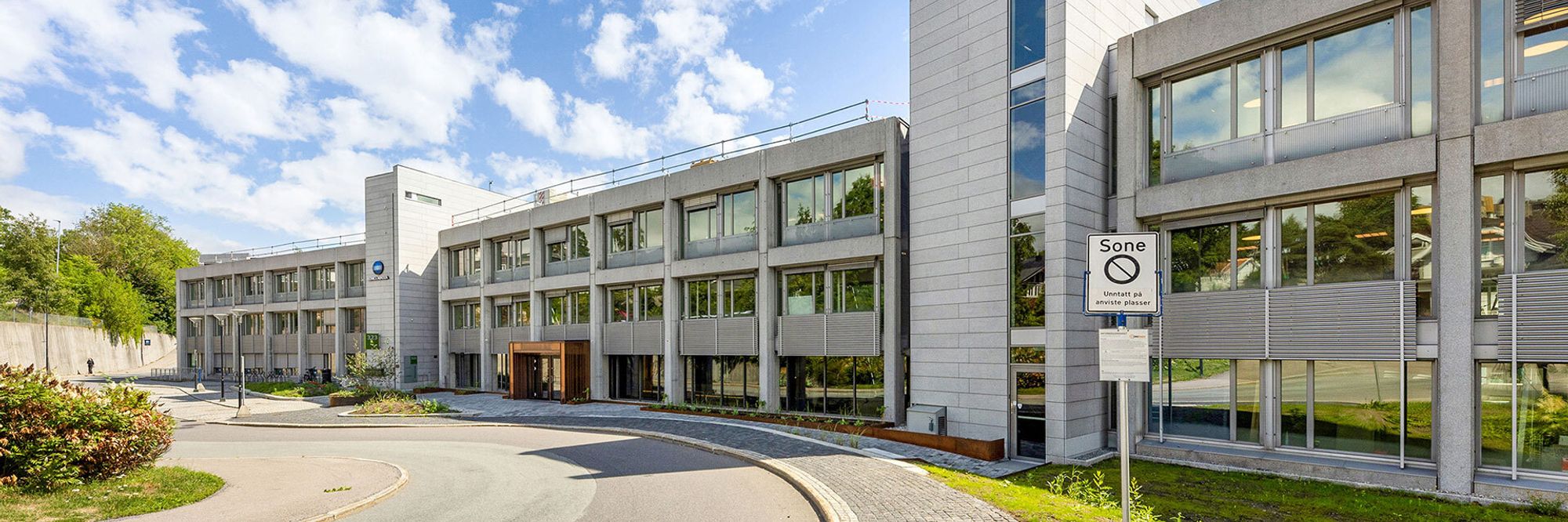
2. Brunvoll
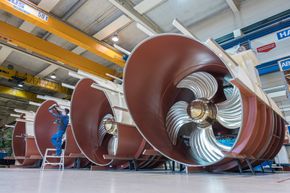
Produserer framdriftssystem og thrustere til avanserte skip.
Brunvoll satset bevisst på effektivisering og investering i nytt og automatisert utstyr for å holde produksjonen i Norge.
Bedriften ser på samspillet mellom engineering og produksjon som en drivkraft i innovasjon og produktutvikling.
- Målrettet jobbing i snart 25 år (abo.): Slik klarer Brunvoll å beholde produksjon og kompetanse i Norge
De har klart å oppnå høy automasjonsgrad og har investert i digitale verktøy og styringssystemer, avanserte programmerte maskineringssentre, som kan kjøre ubemannet på kveld, natt og helg. Effektive produksjonshaller er bygget ut med god internlogistikk, samt avanserte robotceller for sveising og sliping.
Produksjon i Molde og Volda. 470 ansatte.

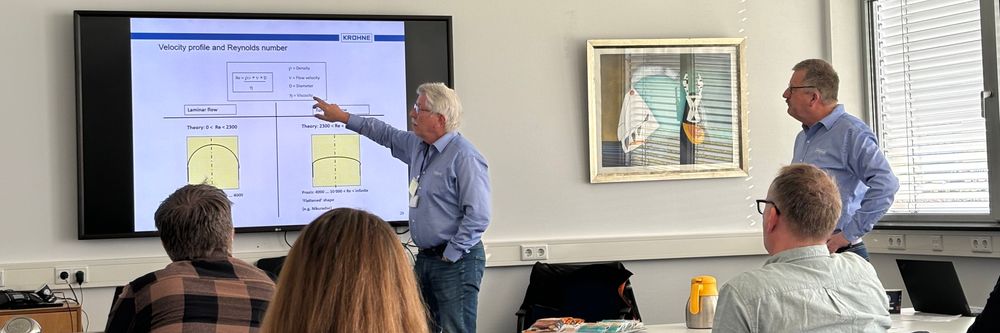
3. Elkem Carbon Fiskaa
Elektrodemasse for smelteverksindustri og aluminiumsprodusenter.
Selskapet har økt effektiviseringen og produksjonskapasiteten ved å ta i bruk ny teknologi og styringssystemer. Det er tatt i bruk energigjenvinningsteknologi og implementert energiledelsessystem som arbeidsmetodikk.
De har gjennomført opplæring og trening av operatører for å påvirke atferd og fremme en kultur for kontinuerlig forbedring. Elkem Carbon Fiskaa har også automatisert arbeidsbelastende prosesser, som medfører redusert timebruk og økt produktivitet. Selskapet har implementert PAD og mobile kontrollromsløsninger.
Effektiviseringstiltakene har ført til økt produksjon, som gjør at bedriften kan betjene en større andel av markedet. De miljømessige tiltakene har gitt tilgang til nye markeder hvor det stilles høyre miljøkrav.
Elkem Carbon Fiskaa holder til i Kristiansand og har 75 ansatte.
- Jakter smart industri: Det er menneskene som overrasker mest
4. Gilje
Vindu- og dørproduksjon.
Gilje har utviklet produksjonen og intern infrastruktur for mest mulig automatisert skreddersøm for å beholde produksjonen i Norge.
Selskapet har utviklet skreddersydd automatisering (GPS - Gilje Produksjons System) som har redusert gjennomløpstid (ledetid) fra 15 dager til 3,5 dager.
Interne feil er redusert med 90 prosent, ledetid med 77 prosent og antall timer i til administrasjon med 600.
All prodsuksjon er ordrestyrt. Gilje har visket bort grensene som finnes mellom produkter, størrelser og funksjoner, alt skal kunne produseres som om det var et standardprodukt.
255 ansatte, fordelt på to produksjonssteder, Gilje Tre i Dirdal og Giljedoor på Moi.
5. Hallingplast
Produserer rør i PE og PP, hovedsakelig til infrastruktur, som drikkevannsrør, avløpsrør kabelrør, industrirør, veiprodukter samt fiskeoppdrett.
Hallingplast har automatisert produksjon døgnkontinuerlig og hele uka. De investerer kontinuerlig for å effektivisere, både maskiner, utstyr, styring og kompetanseheving av ansette.
Bedriften har tatt i bruk ekstruderingsmaskin for automatisk dimensjonsendring fra 90 til 315 millimeter mens produksjonen løper. RFID-merking av produkter og GPS-lokalisering er tatt i bruk på lagre. Hallingplast har også investert i varmegjenvinning og energieffektiviseringstiltak.
Bedriten holder til i Ål i Hallingdal og har 52 ansatte.
- Nominert til Norges smarteste industribedrift: Nå har Plasto flere roboter enn ansatte i produksjonen
6. Plasto
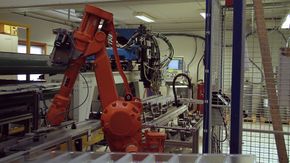
Sprøytestøping av plastprodukter.
Bedriften har automatisert og digitalisert verdikjeden, fra produktutvikling til produksjon.
Plasto produserer døgnkontinuerlig på seks produksjonsceller med 26 roboter. Prosessovervåkningningen deres kommuniserer med smarttelefon, og bedriften kan derfor ha ubemannet produksjon og kvalitetskontroll utenom arbeidstid.
Målt mot tilsvarende produksjon i Kina (benchmarking), kan kunden oppnå 20 prosent direkte besparelser. Det inkluderer kortere leveringstid, ingen lagerkostnad, lav fraktpris, og høy kvalitet.
Produksjon i Åndalsnes. 32 ansatte.
7. Promaps Technology
Teknologi og program som beregner risiko og kostnad i nær sanntid for komplekse transportsystem, blant annet kraftsystem, spesielt med tanke på smart-grid og variasjoner med fornybar kraft.
Promaps gjør det mulig å overvåke og fatte tiltak basert på observasjon av systemets iboende systemegenskap i nær sanntid.
Ifølge selskapet vil det muliggjøre å kjøre systemet mer optimalt med lavere kostnad, sammen med å kunne drifte kraftsystemet nærmere sin kapasitetsgrense.
Bedriften holder til i Bergen og har 4 ansatte.
- Smelteverket i Troms bruker restvarmen til å dyrke alger: Som spiser CO2
8. Raufoss Technology
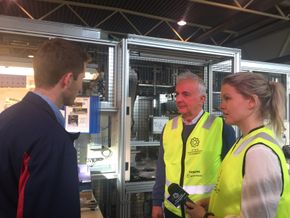
Utvikling og produksjon av bildeler, deriblant hjuloppheng.
Raufoss har digitalisert og automatisert produksjonen med flere roboter.
Bedriften bruker simuleringsverktøy i produkt- og prosessutvikling, både for å forutse produktenes ytelse på bilen og for planlegge effektive produksjons- og formeprosesser samt materialflyt og lagerstyring.
Produksjon på Raufoss og Gjøvik i Norge samt i Kina, Canada og Østerrike. 115 ansatte.
9. Rufo
Kofferter og transportkasser for proffmiljøet.
Rufo Digitaliserer hele prosessen, fra design i 3D til salg, produksjonsstyring og produksjon med roboter, og er på vei mot et mål om å øke effektiviteten med minst 50 prosent.
Bedriften var tidlig ute med digitalisering. Ingen konkurrenter har automatisert og effektivisert produksjonen i samme grad. I løpet av 2017 skal en selger kunne kalkulere et produkt via mobiltelefon, få fram 3D-tegning, pris og leveringstid og deretter sette i gang produksjonen.
De har mål om å bli Europas største leverandør av spesialtilpassede transportkasser og utstyr innen 10 år.
Bedriften har 15 ansatte og older til i Hovdebygda, rett ved ved Ørsta-Volda lufthavn.
10. Thermo Fisher Scientific
Bioteknologi. Har utviklet monodisperse plastkuler, kjent som Ugelstad-kuler eller Dynabeads, som brukes til separasjon, isolering og manipulering av biologiske materialer.
Bedriften er en kandidat på grunn av nyutvikling for raskere og billigere sekvensering av DNA.
Tidligere tok det tre uker for 10-15 personer å produsere nok kuler. Nå klarer én person å lage 10 ganger flere kuler på én dag med ny produksjonsteknologi, utviklet in-house.
180 ansatte. Produksjon i Oslo og Lillestrøm.
Deles ut for fjerde gang
.jpg)
Prisen Norges smarteste industribedrift skal i år deles ut for fjerde gang. Det er Norsk Industri og Siemens som står bak kåringen.
I år ble konkurransen promotert av Tronrud-gründer og industrimann Ola Tronrud og fjerdeårs sivilingeniørstudent Frida Berglund.
I løpet av fire uker besøkt de åtte bedrifter i forskjellige bransjer. Fellesnevner er at de har gjort smarte tiltak og effektivisert, enten i form av automatisering, robotisering eller digitalisering.
Både statsminister Erna Solberg og Arbeiderpartileder Jonas Gahr Støre vil være til stede på konferansen.
Vi gjør oppmerksom på at administrerende direktør og ansvarlig redaktør i TU Media, Jan M. Moberg, sitter i juryen.
- Tjeldbergodden: Nå er pilotanlegget i gang med å produsere hydrogen